The footprint is huge compared with a tractor on normal row crop wheels.
By Julian Cooksley
It takes a certain level of entrepreneurial verve to turn a farm over completely to energy crops to provide feedstock for your own anaerobic digester. This is just the latest step in the evolution of a family business near Coventry that’s always looking to innovate.
The 3.5MW anaerobic digester was constructed last year by the Aston family on the 486ha Highwood Farm at Brinklow. Another investment, and one that could be seen as equally innovative, was a Case IH Magnum Rowtrac tractor – one of the first delivered to the UK.
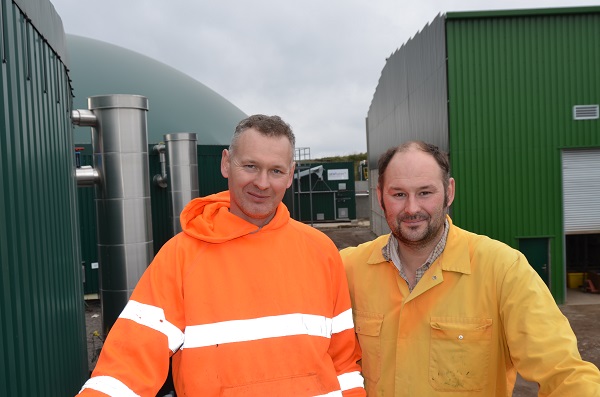
Mark (left) and Dale Aston (right) at the heart of their new AD plant, which produces 1200m3 of raw biogas every hour.
The 340hp Magnum Rowtrac 340 CVX has proved so versatile and adaptable in this complex new farming system that they’ve nicknamed it the “Swiss Army Knife”. And it’s far from being a jack of all trade but master of none comments Dale Aston, who now runs the business with his brother Mark.
“After six months and over 500 hours the Rowtrac has proven itself to be a real all-rounder. It’s so much more versatile and adaptable than we originally anticipated that it’s used for a wide range of tasks,” he explains.
The Aston family has always had an eye for business, ever since the late Tony Aston started with 25ha in 1963. Desperate to avoid the poverty which characterised this mining area after the second world war, he’d started work aged 10 and took on any job to make money, one of them being with an entrepreneurial farmer who became his mentor. Tony Aston liked the idea that the more work he did on the farm the more he got paid.
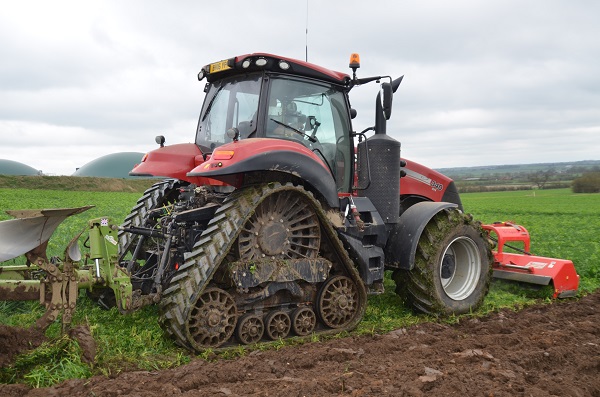
The Astons’ 340hp Case IH Magnum Rowtrac 340 CVX has proved to be far more versatile than the family initially imagined or planned for.
A strong work ethic and entrepreneurial spirit led to him to operate his initial 25ha so that he could also develop other sources of income. Prepared to work all hours, live frugally and make do and mend, he continually reinvested in the business, gained a reputation for hard work and was known for being reliable.
“Father started with absolutely nothing and was determined never to go back. That led him to start a range of businesses, including a major contract spreading slurry for local authorities in the 1980s which helped to pay for the farm. To capitalise on the sand and gravel under the land, the Astons founded Brinklow Quarry, which opened in 1994 and was intended to be a small diversification project.”
Now it’s one of the few independently owned operations in the UK and has contracts with major UK companies to supply materials ranging from building sand to clay. Alongside quarried products the business also supplies a range of recycled quarry products which include quality topsoil, compost, crushed hardcore and washed drainage stone, while also taking in clean hardcore, green waste and topsoil for recycling.
In 1999, when Government legislation was introduced requiring local authorities to increase waste recycling, Coventry City Council approached Tony Aston to compost organic materials. A pilot scheme to recycle green garden waste from domestic premises and the park maintenance department saw material which would previously have been landfilled diverted to the Brinklow facility and turned into a valued compost product for resale or use on the farm. From 1500t in year one, the contract grew to that much every week following the widespread introduction of domestic brown bin collections, and quickly became one of the largest composting sites in the area.
When Tony Aston passed away in 2002, the business employed 25 staff and the quarry had become so busy that the family hadn’t the time to manage their farm, which by then had grown to 486ha, so they decided to rent out 324ha on FBTs and contract out the other 162ha. Two years later, to cope with the increasing scale of their composting operation, they purchased their first Case IH tractor, a four-year-old Quadtrac 9380, from local dealer Startin Tractors at Atherstone.
“It represented a big deal for us because out of necessity we had always farmed with very old machinery and ‘made do and mend,” Dale Aston explains. “That tractor has given exceptional service and even though it’s now 17 years old and has clocked up thousands of hours we’ve only just had to replace the rear tracks – the front ones are original.
“I still use the Quadtrac to pull a 40m3 spreader and can handle 900t of compost per day. The Quadtrac opened my eyes to the benefits of tracks in terms of reducing ground pressure while maximising traction and it can outperform much more modern machinery.”
Fast forward a decade, and having already installed a biomass boiler and merchanting of woodchip fuel the family decided to explore the viability of using part of the farm to produce biomass for an AD plant. In 2014, they gained planning permission for a 500m3 gas-to-grid facility and took back control of all of the farmland. Construction began early the following year and now the plant is fed entirely by crops grown on the farm, including 373ha of maize, 130ha of grass, 180ha of wheat, 93ha of fodder beet, 47ha of triticale and 19ha of oats which are used in cover crops.
The plant includes two 5500t digesters and one 6500t gas tight storage tank, a pasteuriser followed by a separator and a belt dryer to reduce the moisture content of the digestate. It produces 1200m3 of raw biogas (54% methane, 46% CO2) every hour. Of this, 200m3 is used to power a 500kW generator that provides enough electricity and heat to operate the plant and offices and of the remaining 1000m3/hr, 540m3 of biomethane is fed into the grid. There are also plans to liquefy the CO2 element enabling it to be used in the food industry in the very near future.
This cycle of growing and processing crops on the farm provides a ‘closed loop’ system which means that the Aston’s businesses generate less carbon than they consume. This will be further enhanced as they plan to use gas to fuel vehicles and machinery used in the quarry and on the farm.
“Using farmland to produce crops as feedstocks for AD plants has come in for criticism because of the fossil fuel energy used to grow and harvest them, but by producing everything on the farm, minimising transport distances over farming cereals, growing cover crops and using everything that’s produced, our process is actually energy and carbon positive,” says Dale Aston.
“I’d always liked the idea of composting, turning what would otherwise be waste products into something that was of environmental and financial value. The AD plant represented a further step forward down that path. Now we grow the crops on our own farm, produce energy in the form of gas and electricity, will sell the surplus CO2 to the food industry and put the digestate back on the land to provide nutrients for following crops.”
The family’s very conscious of the environment, he stresses, and works hard to minimise the impact of its operations, including emissions. “That was one of the reasons for investing in three new Case IH tractors over the past few months – the Magnum Rowtrac 340 CVX and two Puma 240 CVX models. We always consider any potential purchase very carefully and apart from allowing us to benefit from the latest low emission engines and save fuel, any new tractors had to be reliable and have good dealer support, as we tend to keep equipment for many years.”
When it came to buying new wheeled tractors in the 240-250hp range Dale Aston wanted a combination of high power and light weight – less than nine tonnes. “After comparing the Puma 240 CVX with corresponding models from Fendt, John Deere and Valtra, I decided that the Case IH product represented a very attractive package. Two key factors were the excellent service from our local dealer Startin Tractors and the ability to operate a one-make fleet using the same RTK precision farming technology, as this which will become increasingly important.”
One major requirement for the new tractor was inter-row application of digestate on maize, and this led to the Magnum Rowtrac. “We have large volumes to spread and need to maximise the application period. The aim was to minimise compaction in the 750mm maize rows to allow us to get on the land all year round.
“Even on 61cm-wide tracks, used in combination with 380-section front tyres, the footprint is huge compared with a tractor on normal row crop wheels, so the traction is much greater and the ground pressure is remarkably low so it’s perfect for applying digestate with our 14,000-litre Major vacuum tanker while the maize is in the early stages of growth to provide the crop with water and nutrients.
“We also have a set of 76.2cm-wide tracks and 710-section front tyres to maximise traction. That enables us to use the Rowtrac in two ways, either for heavy cultivations where maximum traction is required, or for delicate inter-row operations to extend the spreading season.
“After the NVZ season we use the Rowtrac with a front-mounted pipe reeler and 15m boom to spread digestate and for this job the tractor’s infinitely variable CVX transmission is ideal because it allows us to precisely adjust our travel speed and spread rate.”
In the spring the Rowtrac is also used for ploughing with a 6f Dowdeswell DP145, followed by a seven-leg Philip Watkins subsoiler in combination with a 6m power harrow. After that, it goes back to working with the digestate spreader boom on grassland and after cereals have been harvested in July will be used to establish cover crops, which are a vital part of the Astons’ system.
“Growing maize often gets a negative press because after it’s harvested run-off can be an issue if the land is left bare over winter, so we grow over 400ha of cover crop mix consisting of oats and mustard to safeguard the soil,” says Dale Aston.
“We use an old 12m pneumatic boom spreader behind one of the Pumas to apply the oats and broadcast the mustard at the same time. This year the cover crop grew so well over the winter that we let some to a local producer who grazed 1000 sheep to maximise its value.”
Cover crops that weren’t grazed were mulched using a 2.8m-wide front-mounted Dragone flail mower on Rowtrac’s front linkage and six-furrow Dowdeswell DP145 reversible on the back.
“Other farmers are showing a lot of interest in our system because growing maize in combination with the use of cover crops and digestate is a very effective way to put nutrients and humus back into the soil while reducing levels of blackgrass. The digestate is very high in nutrients and 24-48 hours after application there’s a visible difference in the crops.”
Spreading digestate is such an important part of the operation that they’re currently designing a new purpose-built tanker which will have dual wheels running in adjacent rows to spread the load and minimise ground pressure, as well as high under-axle clearance which will allow a few weeks of extra spreading time, he continues. “We’re also very keen to buy an inter-row sprayer which will allow herbicides to be applied only where they’re required, reduce our use of ag-chems and minimise crop scorch.
“The Rowtrac has proved to be so much more versatile than we originally realised and become a key part of our system. It’s light and agile when we need to minimise ground pressure for spreading, secondary cultivations and drilling, but we can use it with more ballast and wider tracks to maximise traction for ploughing and heavy cultivations. We’ve even used it with a 3m buck rake on the silage clamp. It has plenty of power, loads of grip and the even distribution of weight across the tracks provides more even consolidation than a wheeled machine.
“Like our other Case IH tractors, the Rowtrac is very easy to drive thanks to its CVX transmission, extremely fuel efficient, offers the latest in guidance technology and is well liked by our operators, which helps us to attract good staff.”
Dale Aston is now considering replacing the Claas Xerion with a new Case IH Magnum 380 CVX with a specially-adapted turnaround seat, building a novel chaser bin system based around the Rowtrac to reduce soil compaction and mud transfer to the road when harvesting maize and purchasing another Rowtrac to replace the original Quadtrac 9380, which will eventually be retired after a long, productive and reliable career.
Tech Specs –Case IH Magnum Rowtrac
The Magnum Rowtrac combines the benefits of wheeled and tracked tractors, yet outperforms both, says Case IH.
Launched in 2015, the initial Magnum Rowtrac 380 CVX was based on the Magnum 380 CVX. Since then, the Rowtrac has proved a popular addition to the company’s tractor range and today’s expanded line-up includes five versions, all powered by an FPT 8.7-litre, six-cylinder engine.
The 310hp Magnum 310 Rowtrac and 340hp Magnum 340 Rowtrac feature a 19×4 Full Powershift 50km/h transmission, with the option of a 40km/h 23×6 full Powershift with creeper. They’re joined by the 310hp Magnum 310 Rowtrac CVX, 340hp Magnum 340 Rowtrac CVX and 379hp Magnum 380 Rowtrac CVX, which incorporate a continuously variable 40km/h CVX transmission.
The Magnum Rowtrac combines the manoeuvrability, handling and versatility of a wheeled tractor, and low ground pressure of a tracked machine. Positive-drive tracks are claimed to deliver power to the ground 100% of the time even when turning, resulting in minimum soil disturbance, enhanced stability and a smoother ride, says Case IH.
The tracks draw on the same design Case IH introduced with the Quadtrac in 1997. Maintaining the principle of using four contact points to transmit power, it features tracks which are 61cm or 76.2cm wide and operate at 193cm, 203.2cm or 223.5cm spacing.
Power transmission is optimised by the fact that the rear tracks oscillate and pivot to maintain a flat footprint, ensuring that traction remains unaffected by either the load on the three-point linkage or drawbar. Unlike a twin-track machine, the Rowtrac produces very little soil scuffing even when turning sharply, leaving the surface level and reducing the need for additional passes to correct damage.
Another claimed advantage over a twin-track machine is that the Rowtrac’s design greatly reduces pressure on the soil, the amount of weight transfer from front to rear and forward/backwards pitching movement. It also enables the use of differential locks, which are standard, to maximise traction, a feature which isn’t possible on twin-track machines.
The Rowtrac is available with Case IH Advanced Farming Systems (AFS) technologies, including advanced vehicle control and guidance systems, farm management software and AFS Connect telematics.
Keep on track
When ploughing, the Case IH designed and built tracks run on the land to maximise grip. The track assembly consists of a positive drive wheel, two idlers and three rollers at the bottom. The rollers are isomounted to absorb shock and compensate a rolling terrain of a road.
The track is automatically tensioned, like the Quadtrac design. This design eliminates slippage between the drive wheel and track because the positive drive is continuous in all conditions, all the time.
The rear track oscillates and pivots to maintain a flat footprint that keeps the power on the ground, so traction is unaffected by linkage or drawbar load, while the ride over uneven terrain is improved.
Farm facts
Highwood Farm, Brinklow, Coventry
- Area Farmed: 486ha plus approx. 360ha rented
- Cropping: Maize (374ha), Winter wheat (180ha), Grass (130ha), Fodder beet (93ha), Triticale (46ha), Oats (19ha), Cover crops (400ha)
- Soil Type: Medium loam (360ha); Heavy clay (60ha); Light/sand 60ha
- Mainline tractors: Case IH Quadtrac 9380; Case IH Rowtrac 340 CVX; Case IH Puma 240 CVX; Case IH Puma 240 CVX; Case IH Puma 210
- AD plant: 2x 5500-tonne digester tanks; 6500-tonne gas tight storage tank; 2x off-site satellite slurry stores of 5000t each