In his first season in the combine seat, one Cambs operator was given the newest machine in a fleet of five. CPM joins the operation to see if the new automated systems helped him match the performance of more experienced drivers.
There’s less need to stop, check and adjust as required.
By Martin Rickatson
Externally, high-output combine development would appear recently to have reached a hiatus. Driven largely by the transport constraints posed by both rural and urban roads, width, height and weight have probably found their limits.
But that hasn’t stopped manufacturers from seeking to enhance performance in other ways, not only with regard to output, but also to efficiency and to grain quality. This has tended to mean that the way components are operated, rather than their size, is the current focus in most combine updates.
Last summer, John Deere replaced the second-generation S600 series single-rotor combines it launched in 2012 with four new S700 models. While the two ranges appear very similar on the outside, and are broadly the same internally, differences in the way the combines are controlled – both by the operator and automatically, by the machine itself – were key to increased capability claims.
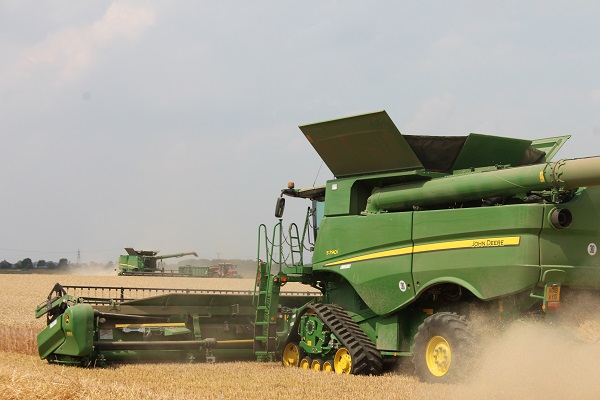
The combines are usually split into a trio and a pair, starting either end of the business’s acreage before meeting in the middle to work as a single team
Centring around automated adjustments that can be configured to meet a desired outcome – a set loss or throughput level, for example – the Integrated Combine Adjustment 2 system uses continuous data analysis from the loss sensors to constantly fine-tune the threshing, separating and cleaning system settings to maintain those set targets. Deere claims ICA2 has the potential to improve utilisation of the combine’s existing componentry, which mirrors that of the S600 series, by an average of 20%.
Meanwhile, in terms of how the driver controls the machine, greater similarities in control systems between the combines and the firm’s tractors are said to have been designed to help operators who are familiar with the latter to quickly also become conversant with the in-cab arrangement of the harvesters when switching from tractor to combine. The main visible difference is the new CommandPro multifunction control lever, almost identical to that which features in the firm’s 6230R and 6250R tractors, which has up to seven individually-programmable shortcut buttons.
Also common to the combines and the firm’s latest tractors is the new GSD 4600 touchscreen, with swipe functionality to scroll between screens and a customisable layout. Operating and field data can be displayed and either stored on a USB stick plugged into the screen or transferred wirelessly to the Operations Centre in Deere’s MyJohnDeere.com web portal. Either transfer format allows data to be downloaded into the farm’s management system and, if required, used to create prescription maps for subsequent operations. Part of the same Combine Advisor package, Deere also added to the options list two ActiveVision cameras, allowing the operator to view the tailings and clean grain elevators via the GSD 4600.
With the S700 models, Deere also added a new Active Yield option, claimed to help improve yield mapping accuracy by automating the process of manually calibrating the combine’s standard mass flow sensor and double-weighing trailers. Inside the grain tank, three weigh cells automatically measure weight change as the tank fills. This data is then compared with that from the combine’s mass flow and moisture sensors and the cumulative data is then used for continuous calibration.
At Waldersey Farms, on the Norfolk/Cambs fenland border, the 5450ha estate requires five 10.5m combines, replaced on a rolling basis, to cut its combinable cropping, consisting primarily of wheat and oilseed rape. The business has used John Deere tractors and harvesters for some time, and its newest combine operator says commonality of functions helped him become quickly familiar this harvest with his new machine. Equipped with a StarFire 6000 receiver and the full suite of automated functions, the S790i’s features have helped David Maybin quickly get close to the outputs of more experienced colleagues on the farm’s other combines, all second-generation S690i models.
A tractor operator for a number of years at Waldersey, in 2018 David spent his first summer switching to a combine at harvest. As operator of one of the farm’s newest 6250R tractors, he was felt to be best-suited to taking charge of the business’ first S790i combine, due partly to its operating similarities.
“As one of the main differences in the cab is the operating layout, farm manager Adrian Kew decided to allow me to operate the new combine as my day-to-day machine is a 6250R, which features the same screen and similar control set-up,” explains David.
“When I went on the operator’s course that John Deere offer for those who are going to be running newly-purchased combines, the trainer there also suggested I should find it relatively easy to learn to operate and get the best from the new machine, even though I had no combine experience. I had no previous operating ideas and habits to ‘unlearn’, and was familiar with controls similar to my 6250R, which I’ve had for a year now.”
An operation the size of Waldersey Farms’ means priority has to be placed on making maximum use of combine capacity by optimising throughput, he suggests.
“That’s obviously not at the expense of lost grain, but we have to press on to get our crops cut in good condition, particularly as we grow a significant area of seed. This is one reason why a combine in which adjustments are made automatically according to the instruction given to it is very helpful, in that there’s less need to stop, check and adjust as required.
Using the same GreenStar 4630 terminal as fitted to his 6250R tractor makes it much easier to quickly become acclimatised when switching from tractor to combine, he says, although a software compatibility issue means that, this season, a GS2630 screen has also been installed alongside it in the cab.
“Farmplan’s Gatekeeper is used for our farm records management, but the software to enable this to run on the GS4630 screen is still in development, so for harvest 2018 I used the GS4630 for combine management and the 2630 for yield mapping through Gatekeeper. Next season it may be possible to run everything through the one screen. But it hasn’t been a problem as such – although it’s easy to swipe between screens on the GS4630, having the GS2630 alongside it doesn’t take up much room.
“We use conventional data transfer, with a USB stick that has all field jobs and maps uploaded onto it inserted into the GS2630 terminal at the beginning of the season, and the data then transferred to the office via the stick once harvest is over. I spread much of the fertiliser using an N-Sensor, and do a lot of the wheat drilling via a variable rate system. So it’s handy to be able to see how the combine yield maps and soil maps can be overlaid at the end of the season to help determine how we should vary seed rate. We’ve been using this technology for a few years now and we’re starting to notice the difference in reduced variation.”
One of the other benefits of the S700 upgrades over the S600 series is the ability to better exploit the full torque capabilities of the engine, believes David. While the engine itself remains the same, some remapping has seen the torque band adjusted to mean that, while the best blend of fuel efficiency and throughput on the S690i models is found by operating at 100% engine load, with the S790i the combine’s ‘sweet spot’ is found at 110% load, he suggests.
“But as we employ quite a few temporary carting staff in summer, if we need to travel a little slower on occasion then we can do so in the knowledge that that the machine should automatically compensate for this.”
The combines are usually split into a trio and a pair, and in each crop start either end of the business’ acreage before meeting in the middle to work as a single team. This year, harvest began with OSR in the first week of July, and by late that month the wheat area was almost half completed. Once the S790i had been installed and set up on farm by local dealer Ben Burgess, David was able to begin fine-tuning his machine, with the aim of quickly getting up to the output levels and down to the loss levels of colleagues on the other combines.
“Setting the ICA 2 system to target 45t/hr output in wheat, at losses of 1.5-3.0%, I was able to fairly quickly get up close to the other drivers’ outputs. Having the same multifunction controller as my tractor helped to quickly get used to operating the machine, and being able to configure the shortcut buttons to do what I want them to do also proved really useful. For example, I’ve set one for the moveable knife, and one for the hydraulic fore/aft feeder house/elevator tilt. The latter is a feature that’s not on our other combines, and although, being on flat land and growing mainly long-strawed crops, I don’t use it so much when cutting, it is very handy when hooking on the header.
“With the Active Yield grain tank weigh cell system which was specified for our S790i, we’ve been able to reduce recorded errors of about 2.1% between what the combine yield meter and the weighbridge have been telling us, and get them down to almost zero. It’s really handy for ensuring weighing accuracy and accounting for changes in bushel weights between different fields and varieties.”
Rather than running the widest-possible 12.2m cutterbars, the farm has standardised operating 10.7m headers at a slightly faster forward speed, these being the maximum width available when the business bought its first S690. There are, however, a number of different types in the fleet, ranging from 600R conventional units to John Deere’s 700 Premium Flow belt header.
“The Premium Flow unit is a great header – it’s been reliable and low maintenance, and does an excellent job of feeding the crop to the auger head first,” says Matt Starling, farm foreman at Waldersey, who runs the unit on his S690i.
“However, it’s obviously not a cheap option, and when the S790i was ordered it was decided that the additional investment probably couldn’t be justified this time. But the new combine was specified with a 600X extendable knife unit, to make oilseed rape cutting easier and reduce losses.”
While the header itself has given few problems, there has been an issue with the drawbar length of the Zürn header trailer. Importer Risborough Agricultural Services and dealer Ben Burgess have been quick to respond and address the problem, though. This has been a relatively minor glitch in a reasonably challenging first season, believes David.
“While the grain quickly became fit in the drought, some of our wheat straw stayed a bit green – some of it is for seed, so isn’t sprayed off – and that makes the combine work harder. But there’s plenty of power, and that greater torque at lower rpm is a definite bonus. We don’t chop a great deal of our straw, as our farm manager, Adrian Kew, has secured a ready market for it, so that also helps limit horsepower requirement and fuel use.”
With each combine at Waldersey putting an annual average of 4-500 separator hours on its clock over a four to five week season – although harvest 2018 looked likely to be shorter – another S790i is probably destined to ultimately be the replacement for the eldest S690i models.
Farm facts
Waldersey Farms, Downham Market, Norfolk
- Farm size: 5450ha
- Cropping mix: Winter wheat, oilseed rape, peas, potatoes, onions, sugar beet, linseed, maize, carrots
- Soils: Grade 1 black fen, silt
- Farm staff: farm manager and assistant manager plus 12-15 staff
- Mainline tractors: John Deere 9560RX, 2x 8370RT, 8370R, 6250R, 5x 6215R, 4x 6155R, 6830
- Combines: 1x John Deere S790i, 4x John Deere S690i (all 10.5m)
- Potato eqpt: 4-row Miedema planter with AVR bedtiller, 2x DeWulf self-propelled harvesters
- Drills: 9m Pöttinger Terrasem, sugar beet drill, 6m power-harrow combination
- Ploughs: 14f Gregoire Besson; 2x 8f Lemken; 2x 6f Pöttinger
- Other cultivation: Maschio 6m power harrow; 2x Dal-Bo rolls (9.5m/12.5m)
- Spreaders/applicators: 8t trailed Amazone with N Sensor, Techneat Avacast 24m
- Sprayers: 2x 36m John Deere 5430i self-propelled, 1x John Deere 8401 trailed
- Materials handlers: 6x JCB Loadall