Forget the Mars rover and turn your attention to the Crover – a new grain-swimming robot that has the potential to eliminate the risk of grain spoilage in store, helping maintain the hard-earned grain quality that cinches premiums. CPM dives in to learn more.
I can see that the Crover is a game changer for the industry.
By Melanie Jenkins
Growers spend most of the year focused on establishing a crop and nurturing it through to harvest, spending hours of time and thousands of pounds on crop care to optimise yield and quality – sometimes for tight margins. And hurrah! It’s come off the field and it’s hit full specification.
The crop’s then put into the shed and sometimes sold months later – only to find the quality has been lost and, rather than earning a premium, it’s lost money. What’s happened in store to change this and what can farmers do about it?
A small team of robotics engineers and software developers have created the world’s first subterranean robot that can burrow through granular materials such as grain, testing for temperature and moisture as it goes.
The Edinburgh-based start-up, Crover – working with Agri-EPI – discovered the first feasible method for locomotion through grain, which it claims could be the answer to improved grain sampling and save farmers anywhere from 80-100% of potential grain losses during the storage process.
“Farmers invest an awful lot of time and money to produce the best crop to meet their target market,” says Duncan Ross of Agri-EPI. “They select the best varieties, sow into correct conditions, choose the right levels of inputs and also spend money on harvesting and drying equipment – it’s an expensive process. So once the crop is harvested, growers want to keep the best level of quality.”
There are some serious financial premiums to be gained from hitting specialist market targets, says Duncan. “If your crop quality drops in store and that grain then gets rejected, you could lose that extra value from your crop.”
So during the storage period it takes concentration, regular monitoring and attention to detail to ensure grain stays in good condition, he adds.
Jon Knight of Crover agrees that this period is all about preserving quality. “But it can be difficult to persuade everyone that they need to be proactive once a crop has gone into store. Some people shut the door and expect the crop to be in the same condition when they take it out again, without necessarily putting in the work to maintain the quality level it goes in at.”
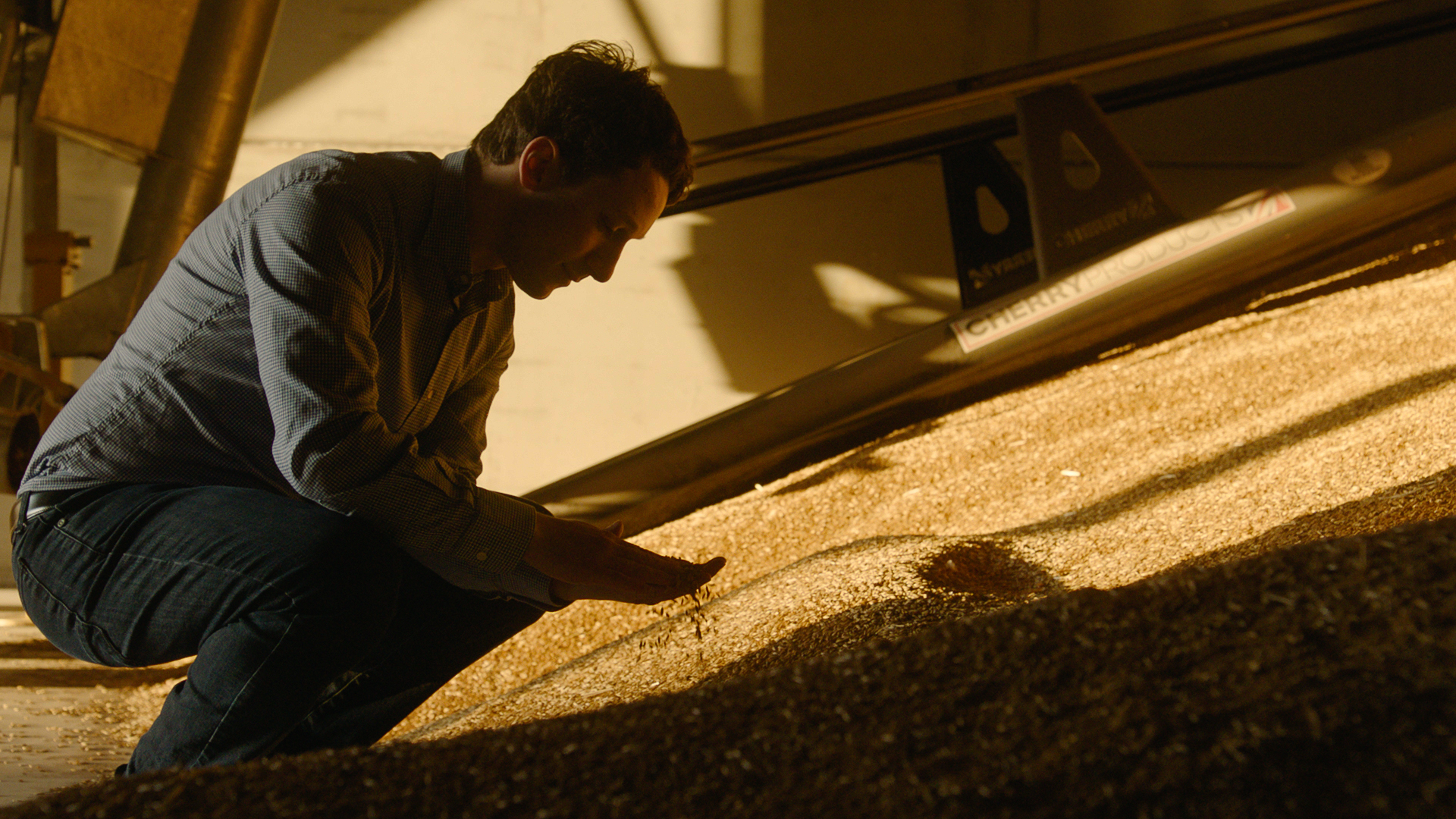
It’s possible the days of wading through the grain store to stick a probe in grain may be numbered.
So it’s about monitoring it and sampling it throughout this period, he explains. But there’s more to it. “Regular testing requires being organised and having a reliable instrument you’re confident will accurately monitor what’s in your store that the buyer will be comfortable with.”
But sampling is only as good as the calibration of equipment, he adds. “A few percent can make a big difference and can cause nightmares if not calibrated properly. You end up wasting your time testing.”
And this all requires a lot of effort, adds Jon. “Especially when farmers are in the midst of harvest and shortly after they’re busy doing autumn cultivations. Sampling is both labour intensive and isn’t always in the safest of conditions. So there can be a tendency to take fewer samples than you intended too, and samples may only get taken from the face of the grain which isn’t representative,” he adds.
An alternative to traipsing around the store to get samples is installing fixed monitoring points, but these are expensive, he says. “And fixed equipment in store can also making loading in and out more difficult and hazardous.
“Millers and maltsters can sample a truck of grain relatively simply, but it might only be at this point you’ll find out if your crop with be accepted or rejected. And rejections can sometimes come as a surprise as sampling on farm isn’t always representative.”
Crover hopes to be able to provide an innovative and cutting-edge solution to the sampling problem so it’s possible the days of wading through the grain store to stick a probe in grain may be numbered.
“We’re trying to improve the amount of information we have on grain and hopefully this will allow for better decision-making and improve outcomes when it comes to maintaining quality,” explains Jon. “Hopefully famers can reduce the subsequent damage after detecting a problem and therefore preserve margins.”
And improving the storage process can come down to data. This is about knowing whether temperatures in the grain are going up or down or if moisture levels are changing or remaining stable, says Jon. “The issue with changes in grain conditions is that they can lead to the development of mould, sprouting and pests.”
There’s also regulatory pressure to move away from fumigating grain towards more integrated pest management (IPM), says Lorenzo Conti, managing director of Crover. “IPM requires measurements every 0.5m2 to be accurate and existing systems can’t provide that.”
A subterranean robot hasn’t been developed before, not because someone hasn’t thought of the idea before, but because up until recently the physics of moving through grain were such a challenge that no one had mastered them, he adds. “Previous iterations of self-propelled robots had moved like snakes, worms or fish to try to travel through grain and had been unsuccessful.”
But while researching his PhD in granular physics, Lorenzo discovered that there was a coupling between rotational and transitional motion in granular material. “Simply, this means that if you’re rotating a cylinder or sphere around a centroid, the rotation and flow generated by this around the object would create enough pressure differential from one side to the other to move through granules. This will work in granular materials but not in fluid and only has a very localised effect.”
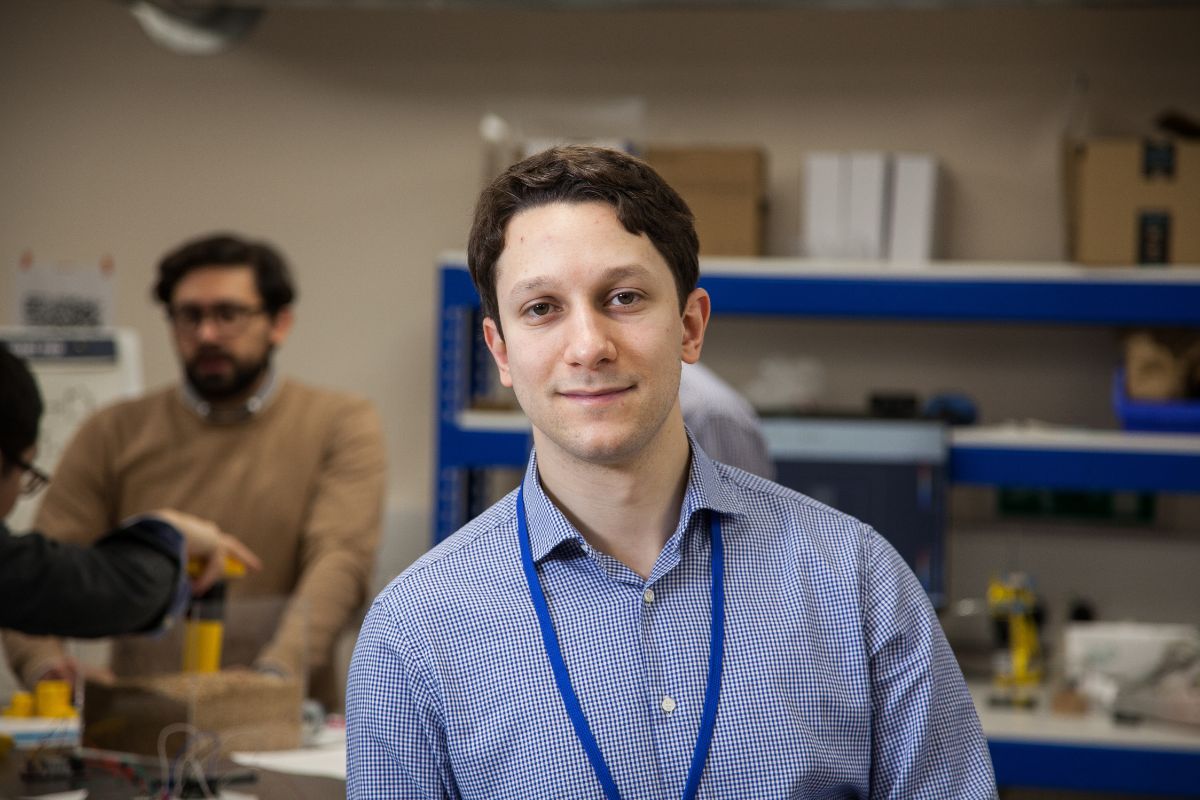
Lorenzo Conti discovered that there was a coupling between rotational and transitional motion in granular material
The Crover robot is equipped with temperature and moisture monitors and as it travels through the grain it builds a 3D map of the bulk. It’s movement also provides a level of mixing of the grain to keep it aerated and avoids a crusting on the surface, explains Lorenzo.
The data the robot collects is sent to a server and can be viewed on an app or web-based platform. “Users can access an overview of their bays and can see visual historical data so they can see how the grain conditions have changed over time, helping them identify trends or to stop problems at early onset.”
At the moment the robot is tethered via a cable to stop it getting lost in the grain bulk, but the hope in the long run is that it will be commercialised as a remote drone, says Lorenzo. The robot is currently able to burrow up to 1m deep into the grain bulk but in time Lorenzo plans for it to be able to go as deep as 8m.
“The robot isn’t commercially available yet as we’re still working on the pilot, but the hope is that it will be ready for sale towards the end of the summer,” he says.
“Our plans is to offer the product as either a yearly service license model, where users sign up to a minimum term of three to five years and pay a license fee yearly for the management of data, access to the web server and support – which won’t mean a large upfront cost.
“Otherwise, there will be an option to buy the hardware and a license for the data and web app,” explains Lorenzo. “It’ll depend on what’s more suitable for the customer.”
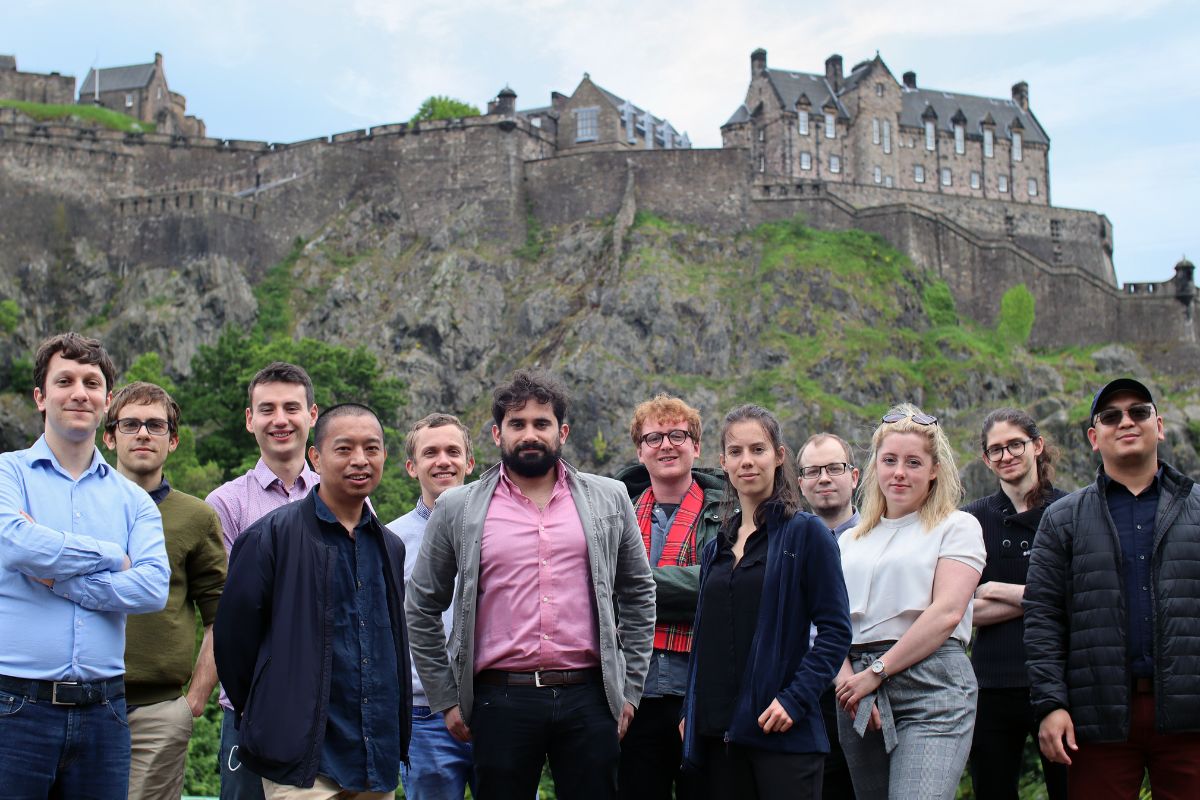
The Edinburgh-based start-up, Crover – working with Agri-EPI – discovered the first feasible method for locomotion through grain.
Crover is also working on a future model of the robot which will be able to take advanced grain sample for quality and will be fully autonomous. “We’re trying to develop a novel sensor that can take readings that have previously only been possible in laboratories. We’re also trying to improve the response time to make the readings even more instantaneous.”
Although the Crover robot looks to have potential to solve some of the monitoring issues in store, Jon warns that it’s not an alternative to storing grain well. “It’s still important to have a good store that’s well equipped for intake, drying, cooling and aeration to maintain proper storage conditions. If something goes wrong in store, it’s vital to be ready to react.”
Beyond sampling grain, the Crover robot could be used for exploration on Mars, helping in the mineral or chemical industry and anywhere where there are bulk solids or powders, adds Lorenzo.
Farmer’s-eye view
Farming at Upper Nisbet Farm in the Scottish Borders, Robert Neill, his wife Jacqueline and sons, Andrew and Harry, run a mixed operation with 400ha of cereals and 290ha of grass. He’s an Agri-EPI satellite farm, meaning he allows projects to be tried in real conditions on site and the Crover team has spent the past few years testing the robot in his grain store.
“Our 3000t capacity grain store was purpose built in 2011. It’s split into three bays of 1000t each and we have a 30t batch drier and weighbridge,” explains Robert. “With this system, we’re in control. If we average 7.4t/ha, I can keep it all in store and market it throughout the year, whenever I feel we need to shift it or when I think we can get the best price.
“But harvest is a really busy time of year for us and putting grain into store is paramount. Corners might be cut, or things not done as they should be and looking after the grain is a challenge,” he admits.
Early in the season is where he finds it hardest as the grain coming off the combine if often at a higher temperature. “This isn’t always an issue in Scotland, but last year the temperatures were high and though drying wasn’t an issue, we had trouble reducing the temperature of the grain going into store. Monitoring the grain to make sure the temperature was dropping was a time consuming, laborious task for myself and my staff. We had to climb over grain heaps, taking samples and checking temperature and moisture.”
Roberts feels that it’s easy for people to get caught out in this situation. “You might think that once the grain is in store it’ll be fine when it comes out again, but store issues can escalate out of control.”
And with the current high prices and threat to global food security, wastage is something Robert feels no one can afford to have. “This country isn’t self-sufficient, so the days for food waste and grain loss are gone in my opinion. We need every tool in the toolbox to look after and monitor what’s in store to get the full potential and profitability out of what we’ve harvested.”
And this is why he feels the developments from the Crover team are so important. “During the trials they had full access to our store and came in on a monthly basis to test their product.”
Having had an issue with his grain store where the roof leaked and the grain sprouted, Robert is doubly convinced by the benefits of regular monitoring. “The grain started to heat up and bugs invaded, so we had to act quickly to remove this grain. Luckily, we have our drier on site so we reconditioned the grain and put it back into store, nipping the problem in the bud. But with the best will in the world, problems will still arise,” he says.
“I can see that the Crover is a game changer for the industry,” he says. “I would like to see this product come to the market to make is possible to sample grain in real-time. I want this information on my desktop or mobile so that if there are issues, I can rectify them – and I think this is something the younger generation wants too.”
This article was taken from the latest issue of CPM. For more articles like this, subscribe here.