Precision technology is improving all the time – but does that mean it’s getting easier to use, or are we moving further away from the plug and play aspirations of the ISOBUS standard? CPM finds out.
Sometimes the functionality just isn’t there or it has to be unlocked at additional cost.
By Olivia Cooper
It was a commendable target – to create an industry standard with which all manufacturers would comply, meaning that any brand of tractor would work with any other implement. But has ISOBUS really delivered? The answer, it seems, could come straight off a school report: Could do better.
The compatibility of different systems depends on what they have in common, and the worldwide ISO 11783 (ISOBUS) standard defines the communication both between agricultural machinery and between equipment and farm software applications. “It is the most significant and comprehensive standard to date, but it leaves room for interpretation, which has led to a great number of innovative but proprietary ISOBUS solutions,” says the Agricultural Industries Electronic Foundation (AEF), which implements international electronic standards.
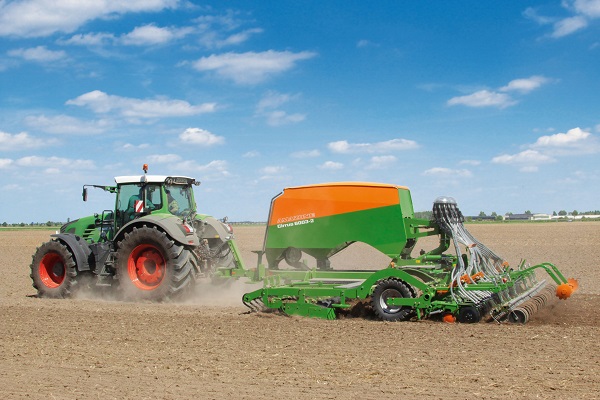
The degree of software sophistication affects how well the precision technique works
All too often, farmers will buy a piece of equipment – like a variable rate spreader – and hook it up to a tractor which is ISOBUS ready. But the task controller may not have the ability to manage variable rates, or that functionality may be locked, says Simon Brown, managing director at Amazone.
The degree of software sophistication also affects how well the precision techniques work, he adds. “If the sprayer boom has 128-section control, but the screen only controls eight, then you’re never going to get more than eight section control. We need better customer awareness about who’s responsible for which bit of the equation – is it the tractor ECU, the task controller or the ISOBUS-ready implement?”
The way in which the computer talks to the implement also varies, says Simon Parrington, commercial director at Soyl. “Historically, we used the RS232 protocol which runs down a dedicated cable, plugged in at both ends. It’s still very common – we have over 1000 customers who are still using it as it’s a low-cost system which works well. But the ISOBUS system is the future, as you need only one cable. The age and brand of equipment will just vary as to how compatible or not it is.”
Simon reckons one of the biggest challenges is the mixed age of machinery. “A tractor might have been around for 15 years, so getting that to talk to a brand new implement through plug and play isn’t really realistic. The technology has moved on so much, and any software upgrade has to be done manually,” he says.
“Farmers normally run mixed fleets and while equipment can be made to work by mixing and matching controls and cables it does require expertise from companies like us. If farmers ran all new kit it would be easier but of course that isn’t practically or economically possible.”
Every brand has its own requirements in terms of file formats, so software providers do a lot of work behind the scenes to service that, explains Simon. “We send out 1.1m ha of application maps a year in 30 different varieties of file format – although most farmers would only need two varieties. Shape and XML files are completely different, but both Gatekeeper and Soyl can generate both file formats quite comfortably.”
The most common applications for those starting out with precision technology are variable fertiliser and spraying rates, says Ben Bell, Fuse product engineer at Agco. “But a common problem is whether the software is up to date – you hook up the equipment and it looks like it will work; the display loads but there are sometimes some functionality issues. If the implement is four or five years old then the software often needs updating.”
This means the farmer has to pay for an engineer to come out and physically update the software, which is less than ideal, he adds. “Your phone and computer update themselves, but none of the machinery or implements do, so it’s added hassle. I think you should be able to update software independently – we need a bit of a step-change there.”
Section control is the most straightforward option, while variable rate application is a bit trickier, says Ben. “There are a variety of ways to get the maps onto a tractor, which can be confusing. If you’re using Farm Works or Gatekeeper you just tell the software what tractor you’re using and it spits out the map in the right format. But with independent companies, there are so many different settings and parameters that issues can arise. You can always get it to work but there’s a lot of incompatibility.”
Jack Howard, product sales specialist at John Deere, agrees that compatibility depends on the creation of the source files. “If you want to vary your fertiliser applications then for John Deere you want a prescription in an RX file type – Gatekeeper works brilliantly, but there are other systems that we’d like more integration with, like Muddy Boots and Greenlight,” he says.
But while ISOBUS hasn’t entirely succeeded in its plug and play aspirations, the next phase might see it deliver more, he adds. “There are some developments going on with ISOBUS TIM (tractor implement management) to improve ISOBUS compatibility. It’s just conceptual at the moment, but AEF and key members are working on delivering it.
“It will be a universal platform where you can plug in a Greenstar guidance system to a red, blue or green tractor and not have to install any sort of new software or controllers. But when it will be delivered depends on how high up it is in the different companies’ priorities.”
Variable rate technology does seem to be the biggest sticking point, says Oliver Wood, precision technology manager at Hutchinsons. “Sometimes the functionality just isn’t there or it has to be unlocked at additional cost, despite paying a premium for ISOBUS ready kit.”
The software side of things is similarly mixed. “With Omnia we produce a range of different file types so we can communicate with the vast majority of new equipment that’s being sold. But the ISO XML file type has a number of different versions – you may assume there’s a standard file type that works across the board but that’s not the case.”
So what needs to happen? “We need the industry to come together and agree some standards that everyone will use. ISOBUS should have been the vehicle that did that but ultimately it’s down to every manufacturer to adopt those standards,” says Oliver.
Omnia already has agreed file types between itself, Gatekeeper and Muddy Boots, and is working on doing the same with Greenlight Grower Management System. “Our farmers and agronomists expect us to make it easier for them. The whole reason we made the Connect product for variable rate control was because of the difficulties in getting prescription plans from the office to the machine,” explains Oliver.
Users found it frustrating to put the map onto a USB drive in the office, then plug it into the tractor, unzip the file and so on, so now they can transfer the information wirelessly through the cloud. “The farmer doesn’t have to worry about moving data around.”
The next challenge the industry faces is how to move into the digital era with datasets in different formats, from other parts of the industry, says Vince Gillingham, director at AgSpace. “How do we make all the data sources talk to each other?”
He believes the answer may come from outside of the industry. “Amazon Web Services is trying to find ways to manage data in different, shareable, formats. Facebook, Twitter and Instagram can all be connected through one password and you can freely move information from one to another, so the security and permissions can bridge the gap. Farmers’ biggest bugbear is having data in different places which they can’t connect.”
Farmers’ datasets are ballooning and companies like AgSpace are spending huge amounts of money on simply storing that data, adds Vince. “We need to find a way for farmers to extract more value from that data and become more efficient with the way we use and share it. I think we will start to see a real shift among software companies to become more integrated – it’s about finding a common platform and set of rules that we can all sign up to and deliver against. But we’re probably 10 years away from seeing a truly seamless solution.”
All one brand
Ryan McCormack, farm manager at Burden Bros in Kent, uses a lot of precision technology both on the farm and contracting operations. “We use GPS and autotrac for steering, variable rate drilling and fertiliser, GPS shutoff on the sprayer and spreader, and all the harvest monitors on the combine for yield mapping and speed adjustment depending on the crop density,” he says. “We have also spent a lot of money on telematics so we can monitor the machine settings, and see their activity and fuel consumption, so that we have a better understanding of what our costs truly are.”
As a John Deere dealer, most of the farm kit is green and yellow, with the exception of an Amazone ZAM Hydro fertiliser spreader, and most of the precision software and hardware runs seamlessly, explains Ryan. “The Amazone isn’t quite as easy as it runs two separate screens – but I’ve decided to go to liquid fertiliser anyway so we will use the John Deere sprayer.”
He runs Gatekeeper and MyJohnDeere as separate systems – the former for budgeting and cost of production and the latter for machinery costings, fuel efficiency and so on. “We also developed our own timekeeping app which has all our customers, machines and jobs on it – operators can see and record everything on their phone, which syncs to the office and links into our invoicing and cost analysis. I want to have a paperless farming system, with wireless transfer between the office and machines. We have good backup through the dealership so if they can’t get it right, nobody can.”
Ryan’s only bugbear is that the combine and forage harvester only send yield maps when you close the field or start the next field. “That means the last field never sends over and you have to go out and shut it down. Also, agricultural colleges are 10 years behind – precision farming is a must have nowadays but students are coming out who don’t have a clue how to use it.”
A mixed approach
McGregor Farms, near Coldstream in the Scottish Borders, is another keen embracer of precision technology, applying variable rate fertiliser, agrochemicals and seed. They have recently started working with Trimble to standardise the technology. “We have John Deere and Case tractors, Väderstad and Claydon drills, two Agrifac sprayers and three Claas combines,” says secretary Sarah Carr. “We have a Trimble TMX-2050 display on all the tractors and it works very well across every brand of equipment.”
Sarah deals with importing and exporting the variable rate maps, which are created in Gatekeeper and then sent to the tractors via the Trimble screens.
“There’s a lot of work behind the scenes, putting together variable rate plans and getting machines to speak to one another, but once those hurdles are overcome, it’s fairly seamless,” says Colin McGregor. In the past five years this has become easier as machine connectivity has improved, and the cloud has become widely accessible. “Now it’s so easy to transfer data between machines and back to the office.”