Although fertilisers have transformed food production, they’re also the bane of agriculture for many reasons – including a high carbon footprint, greenhouse gas emissions, inefficiency of use, pollution of the environment and most recently, high prices. CPM looks at a green technology that could help pave the way to net zero.
Changing to a net zero fertiliser provides agriculture with an opportunity for rapid change without hitting farmers’ pockets.
By Lucy de la Pasture
For the first time in 80 years there’s a real nervousness about UK food security. World stocks of commodity food crops are forecast to be tight and high input prices are causing some growers to carefully consider plans for the next cropping season – is the risk worth the reward in a market that’s so highly volatile?
It’s the price of fertiliser and it’s availability for 2023 that’s one of the main concerns. When asked about fertiliser security earlier this spring Defra secretary of state, George Eustice, caused quite a stir in the farming community by suggesting that growers make use of organic manures instead. He later refined his remarks, suggesting green technologies were becoming available to help farmers which would enable them to utilise waste streams as fertiliser.
It’s true that there’s no shortage of waste from food processing, anaerobic digestion and from the sewage collected by water companies. All carry valuable nutrients, some of which may either end up in landfill or even be discharged into water courses. But how close are we to closing the circle and returning those nutrients to the soil where they can function as fertilisers to help grow crops? The answer is much closer than you may have thought.
Green technology company CCm Technologies will be supplying in excess of 500t of carbon neutral fertiliser to UK farms this spring. The relatively low volume hitting the market is a harbinger of a potential new era in fertiliser production using a novel technology which enables organo-mineral fertilisers to be produced from waste streams, explains CEO Pawel Kisielewski.
“The challenge with the fertiliser is that we have a very carbon intensive technology which is vital for growing food. But it’s created using a 70-year-old process which has a huge carbon footprint. At CCm, we capture carbon dioxide (CO2) and use it stabilise a wide variety of materials from other waste streams (such as ammonia and phosphates) and convert it into resources such as fertilisers or plastics,” he explains.
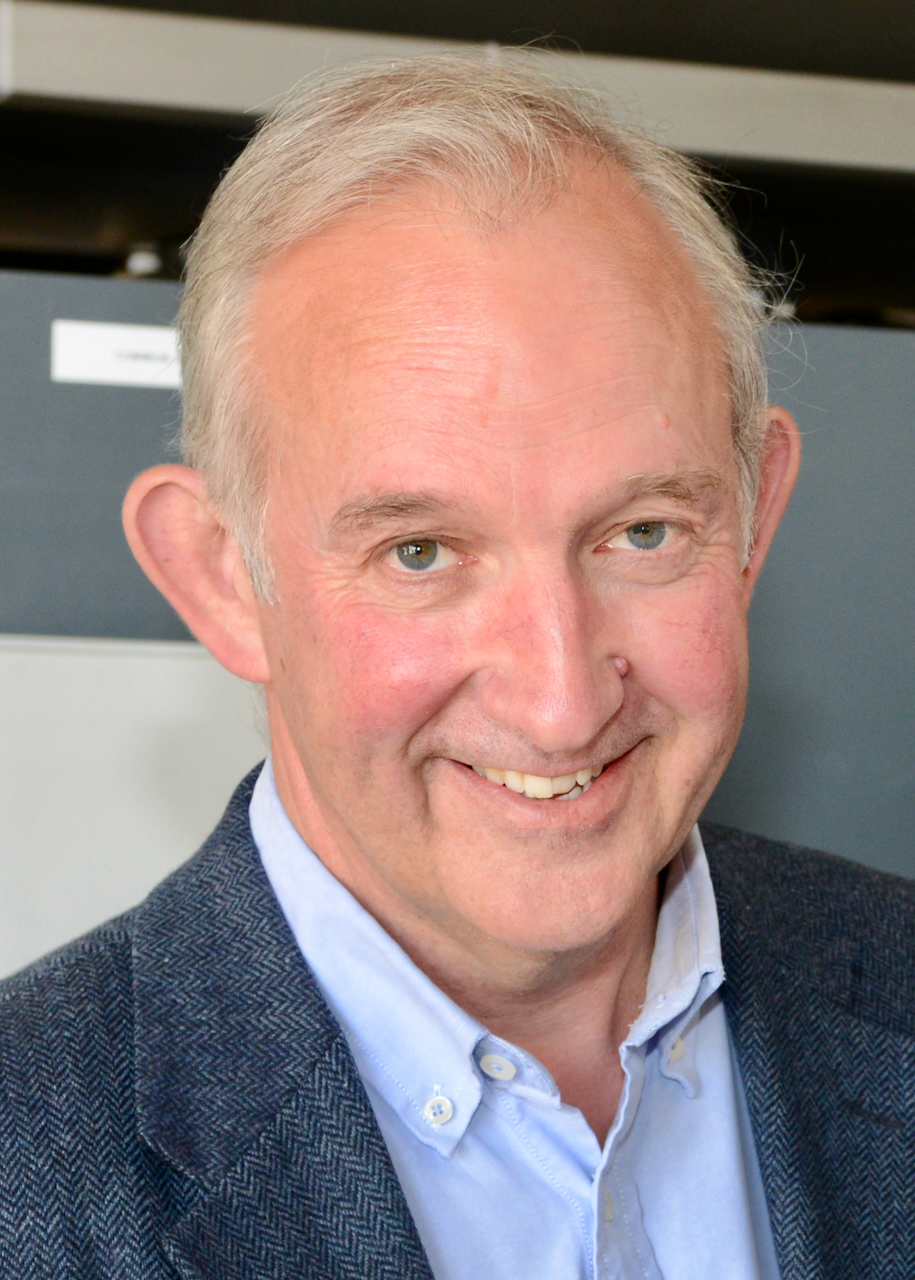
In university trials we’re seeing the potential to reduce nutrient applications by up to 20%. We
believe this is because the product is more stable as nutrients have a more controlled release profile, says Peter Hammond.
The company was founded in 2011 after Pawel met chemical engineer, Prof Peter Hammond, who’s now CCm’s chief technical officer. Peter had found a way to capture CO2 and use it to put circularity back into systems and the marriage of his IP and Pawel’s expertise in finance began to give credence to the adage ‘waste is just a resource in the wrong place’.
In essence it’s a mixing and blending technology with three types of input – fibrous material from grass, straw, woodchip or digestate; NH3 recovered from animal or food waste; and CO2 generally recovered from exhaust streams, such as in biogas separation, explains Peter.
“Carbon dioxide is quite unreactive, and so that makes it a difficult customer to get rid of. However, we’re very lucky in waste materials that one of the chemicals that’s actually relatively freely available in them is ammonia. And that ammonia very much likes to react with carbon dioxide,” explains Peter.
“The first step in the process is capture of CO2 by the ammonia that’s held in the liquid. We have to add some additional materials, particularly ones that are high in calcium, and also some nitrate material, so that the ammonia that’s held there is transformed into ammonium nitrate. And it’s stabilised by the creation of calcium carbonate, that helps literally glue the whole system together.
“We can produce a blend that’s has a nutrient load of up to 30%, but not exceeding 20% N. With access to the right feedstocks, we can reformulate the fertiliser to provide the right nutrient ratios to put back nutrients where it’s needed. And while this could be from all recycled materials, we can also incorporate some conventional P if a higher percentage is required than is obtainable from the feedstock.”
Unlike conventional fertilisers, the CCm product is a pellet – more like a feed nut rather than a prill – but it can be applied through existing farm equipment, adds Pawel, having tested the product’s spreadability extensively.
Where conventional fertiliser production is energy intensive, with 4-7 tonnes of CO2 to produce one tonne of ammonium nitrate fertiliser, the CCm process is carbon neutral or even climate positive. Given that nitrogen fertilisers account for around 60% of greenhouse gas emissions in arable enterprises, it’s not hard to see how this technology could help pave the way for UK farmers to become net zero or better, says Peter.
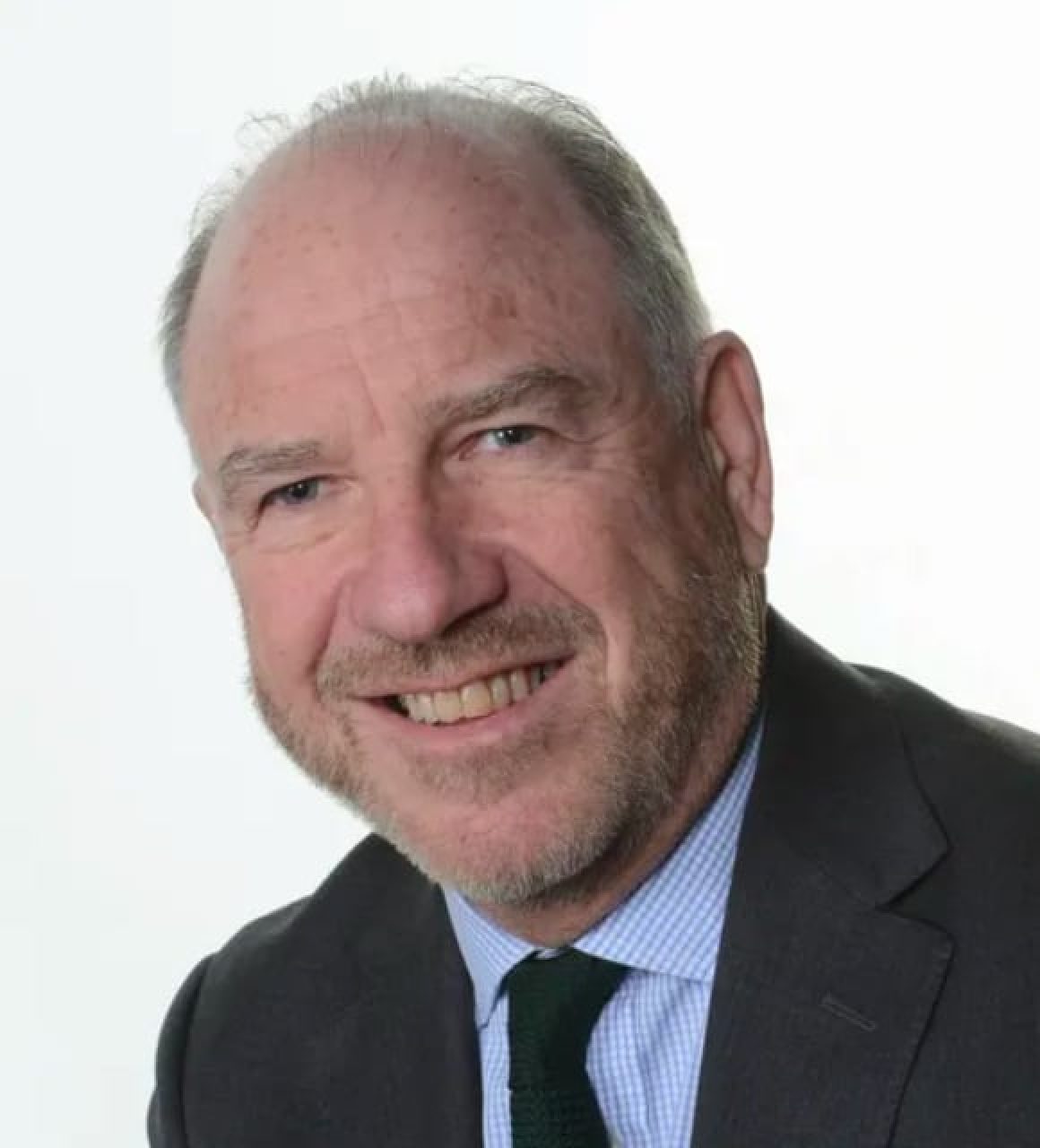
The benefits from applying the stabilised form of carbon in CCm’s fertilisers appear to be long standing, so it becomes a virtuous circle, adds Pawel Kisielewski.
“Changing to a net zero fertiliser provides agriculture with an opportunity for rapid change without hitting farmers’ pockets.”
One of the objectives of the company is to provide this ‘green’ fertiliser at a cost that’s equivalent or more cost-effective to growers than current sources (pre the recent price inflation), adds Pawel.
As proof of concept, CCm has invested time in looking at how its fertiliser products perform in the field – both in replicated plot trials at the Royal Agriculture College at Cirencester and in larger scale trials with Velcourt on multiple crop and soil types.
“We’ve actually been testing it for the past six years,” says Peter. “And we found that across the board, we can attain the same yield and growth patterns that you would see with conventional fertilisers, so the results have been very encouraging from the start.”
But that’s not where the potential benefits end according to work that’s been carried out both in the field and by researchers.
“We started to see additional benefits in the soil. Essentially, we’re physically returning organic matter to the soil in a stabilised form – 50-70% of CCm fertiliser is organic content – and this helps the soil function more effectively as a growing medium,” explains Peter.
CCm looked more closely at these effects to better understand what was happening. Peer reviewed work carried out by University of Sheffield in 2019 (Journal of CO2 Utilization) found some positive results – including increases in water and nutrient retention of 32-62%, depending on soil type; increases in the soil microbial activity by approx 20%; an increase in crop biomass of 38%; and a soil pH increase of 0.7-1.1 units.
“We’re also seeing the potential to reduce nutrient applications by up to 20%. We believe this is because the product is more stable and as nutrients have a more controlled release profile. Some nutrients which would have otherwise been leached are available to the plant, thereby increasing nutrient-use efficiency,” explains Peter.
Further trials are underway at Cranfield University, says Peter, which are looking even more closely at what’s going on in the soil and determining the emissions from CCm’s product.
“We have two year’s data so far and it’s showing a lowering of losses via emissions to the air and from the leaching of nutrients through the soil. And those things are combining to mean we’re starting to see potential to reduce the amount of nutrients that need to be applied to crops,” he says.
The benefits from applying the stabilised form of carbon in CCm’s fertilisers appear to be long standing, so it becomes a virtuous circle, adds Pawel.
Additional trials using CCm fertiliser have been carried out in work by Tesco and WWF in 2020 on potatoes. The green technology has also attracted Pepsico to become CCm’s leading food customer, with CO2 from potato peelings produced at the Walker’s plant now being used to produce a fertiliser for some of its growers this spring.
Food processors and retailers are interested in this technology for a number of reasons, comments Pawel, including reducing their scope three emissions. These are all indirect emissions (not included in scope 2) that occur in the value chain, including both upstream and downstream of the reporting company.
“It’s a significant challenge for them to meet these targets so they’ve been very engaged with how this technology can help.”
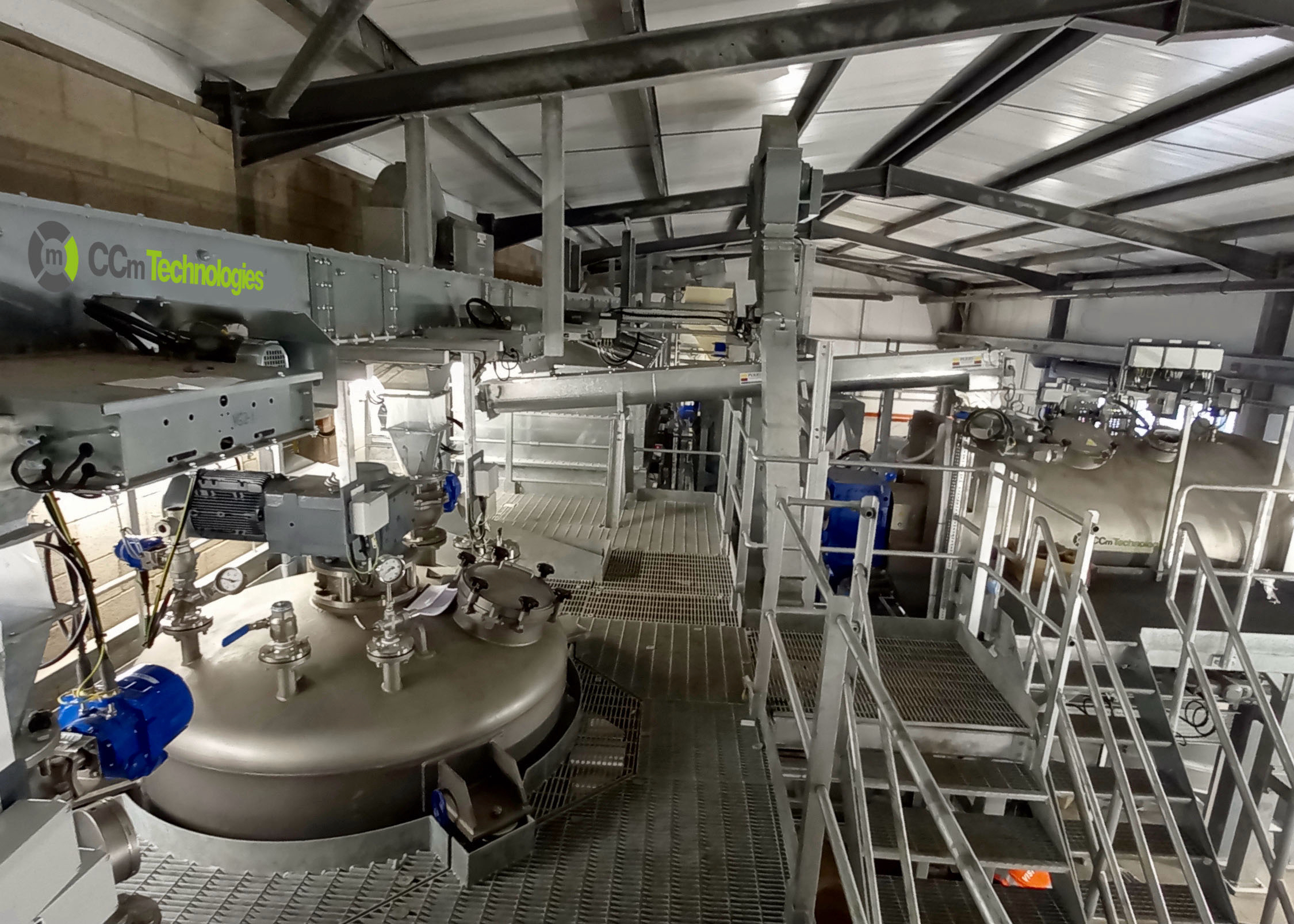
Severn Trent has recently introduced CCm’s technology to its sewage treatment process at Minworth, using captured carbon dioxide to stabilise nitrogen, phosphate and organic chemicals held within waste streams and
turning them into sustainable plant nutrients.
The UK’s second biggest water company, Severn Trent, has recently introduced CCm’s technology to its sewage treatment process, using captured carbon dioxide to stabilise nitrogen, phosphate and organic chemicals held within waste streams and turning them into sustainable plant nutrients.
But as with all virtuous changes, there are always obstacles to overcome. “There’s need for some clarification around the permitting for sewage sludge, which we’re in conversation with Defra about,” explains Pawel. “Currently the legislation around its handling could be a limiting factor to creating this circularity.”
With such endless sources of waste products on hand, and technology that could easily reduce the pressure on the finite resources currently used in fertiliser manufacture, could UK agriculture be on the cusp of a sea change?
Pawel believes that by taking materials at their ‘end of life’ and reintroducing them as plant nutrients, effectively closing the circle, could mobilise agriculture as a tool to fix the environment without fundamentally changing the way crop production is delivered.
He’s confident CCm’s operation could meet a rising demand from growers as it can scale up quickly. “At least 15,000t will be available next year with significantly volumes available in 2024.”
Returning nutrients to the field
The much-loved combination of beer and crisps is being harnessed for the first time to tackle climate change. Crisps firm Walkers is using potato peelings to produce fertiliser and aims to slash its CO2 emissions from its manufacturing process by 70%.
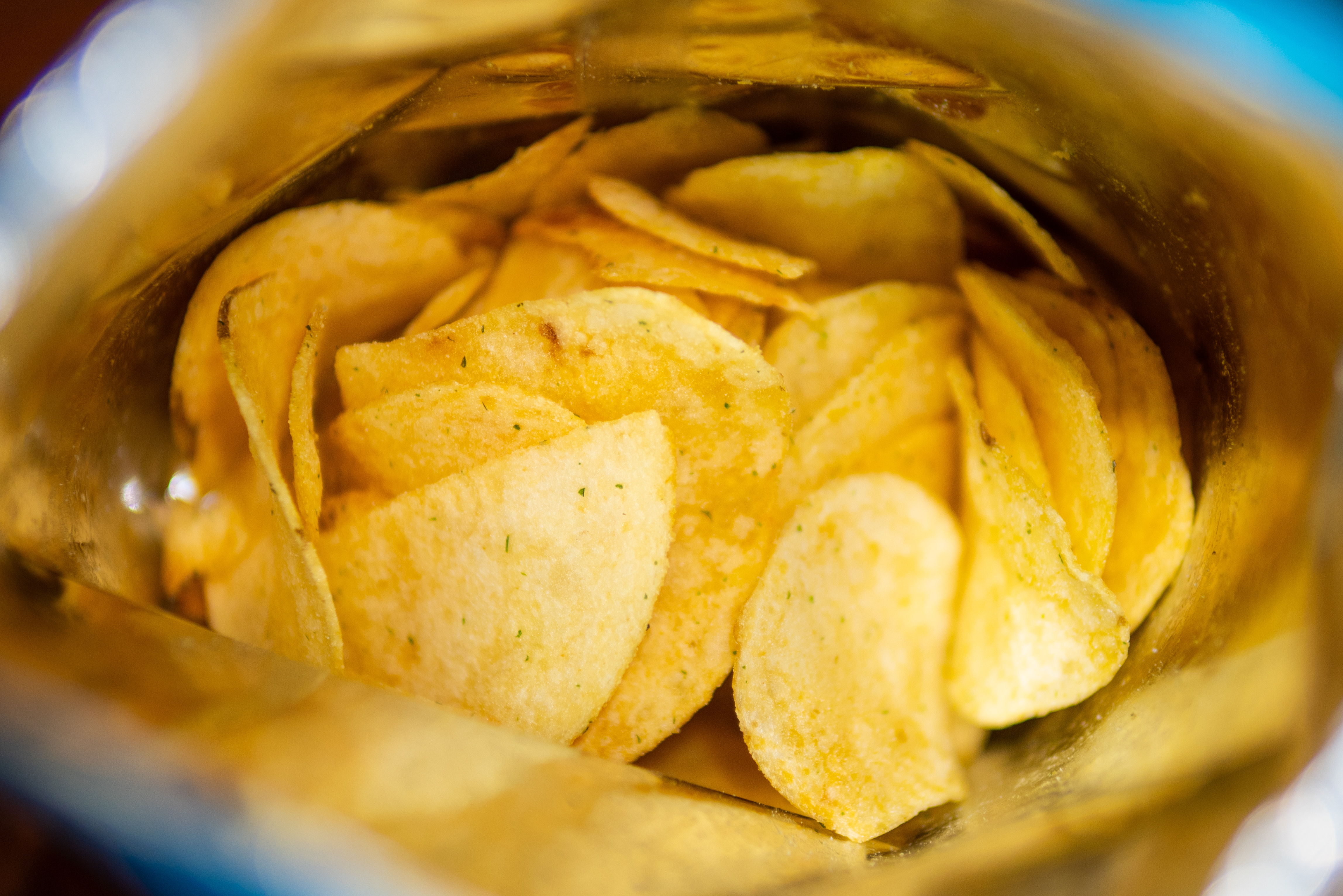
PepsiCo potato growers should
be among the first to use the net zero fertiliser made from
peelings from the company’s Leicester factory.
Using CCm’s carbon-capture technology, potato peelings leftover from making crisps will be transformed into low-carbon fertiliser and returned to farms where potatoes for Walkers crisps are grown across the UK, according to Pepsico.
The technology is designed to connect to the factory’s anaerobic digestor, which already uses food waste to generate nearly 75% of the electricity used at the plant. The equipment will use the by-product waste from the anaerobic digestion process to create the fertiliser.
By turning potato waste into a reusable resource, Walkers is driving more circularity in the potato growing process, claims the firm, helping farmers reduce their impact on the environment. The new initiative is hoped to set Walkers on a path to becoming carbon-negative in its potato production over the next decade.
Walkers brand owner, PepsiCo, is also looking to bring the benefits of the organo-mineral circular fertiliser to further European markets and other crops, such as oats and corn.
David Wilkinson, PepsiCo’s senior director of European agriculture comments: “From circular potatoes to circular crops, this innovation with CCm Technologies could provide learnings for the whole of the food system, enabling the agriculture sector to play its part in combating climate change. This is just the beginning of an ambitious journey, we’re incredibly excited to trial the fertiliser on a bigger scale and discover its full potential.
“This initiative is a step in the right direction, and we will continue working hard to lower the carbonimpact of our products from field, through manufacturing sites, to consumption.”
Pawel Kisielewski adds: “By enabling the sustainable reuse of waste resources and the locking of captured carbon back into the soil, our partnership represents a significant step forward in proving that agriculture can play a role in carbon reduction and the circular economy.”
This article was taken from the latest issue of CPM. For more articles like this, subscribe here.