Combine manufacturers have been demonstrating some of the new features added to their models to help make harvest a little easier. CPM rounds up the stand-out improvements.
Significant enhancements include a higher capacity six-auger bed to transfer clean grain from the sieves.
By David Jones
By all accounts, harvest 2017 has had its fair share of testing moments. As the heavy rain drummed down, chances are many operators will have used the downtime to reflect on features they’d like to see in the next combine that cuts through their crop.
Nor have manufacturers been slack to respond – whether it’s new technology in the cab that eases the job of fine-tuning settings, or functionality that masters a hilly terrain, the 2018 line-up of new machines is bound to have something to appeal to even the most demanding operator.
Rotary on a road trip
New Holland’s harvesting team has been on the road in recent weeks, demonstrating – when the weather allowed – its new CR Revelation twin rotary combine around the country. The company claims a 10% boost in productivity from the 2018 CR models, delivered in part by new NEF engines that raise the power output by 50hp to 700hp on the range-topping CR10.90 and to 517hp on the CR8.80.
A re-designed residue-management system provides a spreading width of 13.7m , at the same time delivering a finer chopper sample. In addition, the paintwork throughout the machine has been changed to provide greater colour contrast between the various parts in key areas of the machine, so enhancing functional identification for daily maintenance through the harvest period.
The mainframe, grain pan and beater grate are now yellow, to provide improved visibility in the cleaning shoe – the capacity of which has also been boosted by 15%. The grain tank has had the yellow treatment, too, in order to make it easier for the operator to monitor and check grain quality on the move.
NH’s Nigel Honeyman explains that more machine functions can now be controlled from the cab, with options including adjustment of the rotor vanes, which is now infinitely variable between slow and fast. “The in-cab concave reset facility also boosts the machine’s productivity, significantly reducing downtime in the event of a concave breakaway,” he states, drawing attention to the 20-position rotor vane covers which can take account of differing crop conditions through the course of the working day.
“Re-setting the concave is now a very quick process carried out from the cab,” Nigel continues. “The operator just empties the rotors, stops the combine, re-arms the concaves automatically and carries on with the job, saving a good 20-30mins that doing it manually would have taken.”
The three models at the top of the new CR range are specified with TwinPitch Plus rotors, with 7.5cm rasp-bars, which provide power efficiency gains from 20kW on the CR8.90 to 28kW on the range-topping CR10.90.
Improvements in the residue-management function include a new chaff spreader design, which incorporates an air blast, and enhanced chop quality thanks to longer counter knives and an increased rotor speed – up to 4000rpm (from 3500rpm). The horsepower requirement for this system is now, in fact, slightly lower than previously at 110, down from 113.
Together, it’s claimed, these features promote a finer chop sample and a 50% reduction in long straw. A patented air crop-flow system has replaced the conventional impact-bases design. Spreading width has been broadened to 13.7m and can now be adjusted from the cab, assisted by the Opti-Spread straw management system which, itself, has received a 25% strengthening boost to the hydromotors, v-shaped paddles and cleaning scrapers.
Accompanying the twin-rotary newcomer on its nationwide tour, the 2018 model CX5 and CX6 straw-walker machines have been showing off their upgrades and new features. Comprising four models in seven versions, common to all is the Harvest Suite cab – the result, New Holland says, of extensive user consultation.
Already claimed as having the largest cab in its class, with 3.7 cu m of space, the CX cab now provides a 7% increase in the area of glass, including a full width rear window and forward vision that spans the widest headers. There’s a new deluxe air seat and adjustable side console, while the steering column is now slimmer.
Acknowledging that not all cereal growers farm on level ground, the two CX models are offered in Laterale and Hillside formats. Laterale’s automatic levelling system provides transverse slope compensation of up to 18% on both sides, allowing even distribution of grain to optimise grain cleaning.
In those local situations where the topography poses even more of a challenge, the CX5.90 Hillside version’s two independent hydraulic systems compensate for both lateral and longitudinal inclines. This, the company says, ensures the machine’s separation and cleaning systems are operating at optimum efficiency.
Nigel makes the point that the Opti-Speed straw management system on the CR7 and CR8 combines is now available as an option on the new CX5 and CX6 machines.
Axial-Flow upgrades
The focus of progress at Case IH remains on simplicity of design and the gentle threshing action for its 2018 Axial-Flow combine range. This retains the system that doesn’t feature a drum or a concave, relying solely on the rotor for both threshing and separation.
The company’s harvesting product specialist, Paul Freeman, highlights some of the recent developments. “Significant enhancements to the smaller 140 machines include a higher capacity six-auger bed to transfer clean grain from the sieves, together with a Cross-Flow cleaning system that compensates for up to 12° of lateral slope.” he explains.
“In addition, the 140 models also benefit from six smaller concave sections, while the grain tank capacity on the two larger models in this series – the 6140 and 7140 – is now 10,570 litres.”
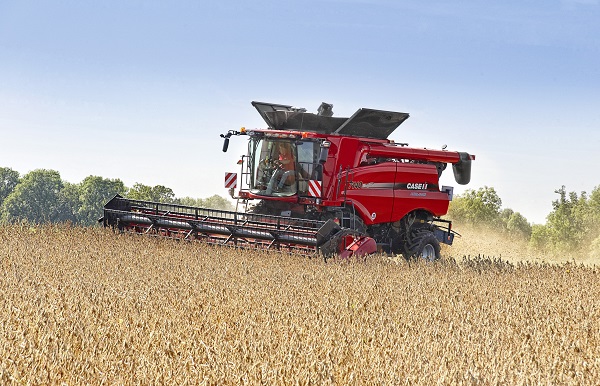
The Cross-Flow cleaning system on the Case compensates for up to 12° of lateral slope.
Case IH is now offering a new Xtra-Chopping package for Axial-Flow 240 models. “This retains the existing integral two-speed Case IH Magna-Cut 120 blade chopper as a discharge beater to pre-chop residue and propel it into the hood-mounted Redekop MAV chopper,” Paul continues.
The patented design, he says, features 12-blade paddle fans at each end of the chopper rotor that generate air flow velocities of up to 145km/hr to draw straw and chaff through the chopper as it leaves the rear of the Axial-Flow rotor.
“This helps present straw lengthways to the 96 reversible carbide-coated blades mounted in eight rows on the rotor. Operating at 3250rpm, these work in conjunction with an adjustable counter knife, helping to slice straw longitudinally – as well as conventionally – for faster breakdown.”
MF range extends
Massey Ferguson is about to introduce two new Activa S ParaLevel models – the 7345 S PL and the 7347 S PL – to complete a range of fully self-levelling combines. Both will be available with the MCS threshing and separation system and with either two-wheel or four-wheel drive rear axles.
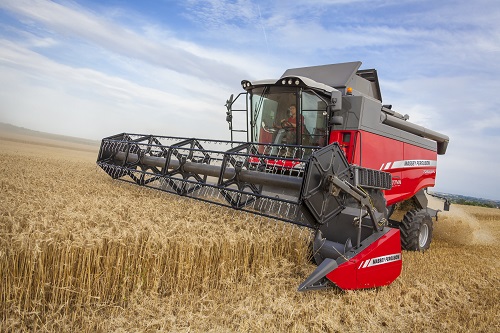
The 7345 S PL will join Massey Ferguson’s range of fully self-levelling combines and will be available with the MCS threshing and separation system.
Harvesting specialist at MF, Joe Ford, believes the ParaLevel system has proved its worth. “The parallelogram design features two strong 10-stud final drives and the ability to level up to 20% on transversal slopes, combined with the rear axle,” he states. “The two-wheel drive version can deal with slopes of up to 15% and the system on both machines is controlled automatically, using an electronic pendulum installed on the front axle.”
The 7345 S PL has a transport width of 3.49m and is fitted with 800/65 R32 front tyres, while the 7347 S PL has 650/75 R32 front tyres.
MF Beta updates for 2018 include the availability of the 7370 model as a rubber tracked version, featuring the Atrak system that’s proved its worth on the larger Centora and Delta combines. Atrak has an integrated final drive, directly bolted to the front axle and provides a maximum ground speed of 25km/hr.
In addition, the Beta’s header reverse system now has hydraulic drive, with a 365cc motor that reverses the lower shaft via a strong belt drive. The system is said to ensure quick and easy unblocking, so enhancing productivity in difficult harvesting conditions.
In the cab, the new passenger seat and refrigerator, introduced on the Centora and Delta combines this year, will be available as a Beta option from 2018.
Identifying further new features destined for Activa, Activa S and Beta combines next year, Joe picks out a new grain pan design. “This will incorporate removable plastic elements to the front, accessed through the opened stone trap, and will make it possible to extract the five, or six, elements for cleaning – which will be very useful when combining oilseed rape or in wet conditions.”
The hydraulic system for the open/close action of the unloading auger, he adds, has also been upgraded in order to boost the speed of the auger’s action.
Operators of the 2018 Activa and Beta models will also be able to select either of two pre-defined harvesting speeds by pushing the multifunction lever to the right while harvesting. The returns volume sensor has also been modified to provide a more precise reading and allow easier operator adjustment of the visualisation in the terminal.
Action has also been taken to avoid the deposit of chaff and straw on top of the rear axle, with the fitting of a canvas to the rear of the shaker shoe. The effect of this will be to guide residue at the rear of the shoe either on to the ground or, where fitted, into the chaff spreader.
Claas fine-tunes
Attention to detail has always been a source of pride for the German machinery giant and this has continued to be the focus this year. No new combines to dazzle the market, but a number of innovative upgrades to the current line-up for 2018.
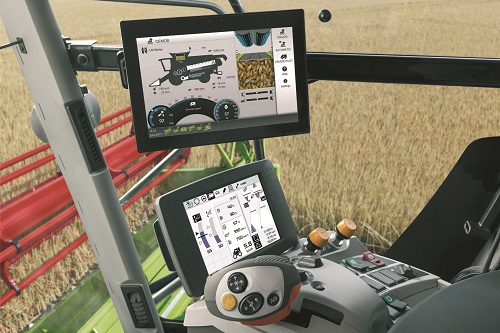
The new CEBIS Mobile 30cm colour touch screen allows the operator to adjust all the assistance system functions simply by touching the screen.
First up is the new CEBIS Mobile system for the Lexion 700 and 600 Series. The manufacturer’s UK Harvest Product Specialist, Adam Hayward, believes this development sets new standards in the operation of the established Cruise Pilot, CEMOS Dialog and CEMOS Automatic operator assistance technology.
“The new CEBIS Mobile 30cm colour touch screen brings the functions of all the current assistance systems together,” he explains. “This enables the operator to adjust all the assistance system functions as required using the standardised, menu-guided interface, simply by touching the screen.”
A high-resolution, large colour screen makes it easier to monitor all aspects of the combine’s performance by means of clearly structured data and an intuitive touchscreen operation, says Adam. “A combine harvester silhouette, which appears in the main screen area displays continuously the settings for all the combine’s principal function areas. These include status feedback on, for example, rotor and fan speed, grain moisture and grain tank fill level.”
The image from the grain quality camera also appears on the screen, allowing the operator to monitor grain quality constantly. This evaluation facility enables the CEMOS Auto-Cleaning system to optimise the cleaned status of the grain. At the same time, the operator can make use of two simple slide controllers on the screen to set the desired balance between the cleanliness of the grain, straw quality and throughput.
“In the lower part of the screen is the ‘cockpit’,” Adam continues. “Displaying the status of the Cruise Pilot, it provides read-outs on forward speed, throughput in the feeder housing – in terms of t/hr – together with the engine load. The system will also draw attention to any factor that may be limiting the combine’s performance under the prevailing operating conditions.”
As an alternative to using CEBIS, the operator may also adjust the parameters of the Cruise Pilot’s functions by using the CEBIS Mobile. Menu navigation for any adjustments that might be required is identical in all three of the assistance systems.
CEMOS Automatic covers all the operator assistance systems, including Auto Separation, Auto Cleaning and Auto Slope, while CEMOS Dialog – the operator’s partner – is ever-active in the background. This facility monitors all work processes, analysing the data and prompting the operator if the machine’s potential isn’t being fully used.
Deutz masters the slopes
Coping with the demands of undulating fields has been the focus of attention this year for Same Deutz-Fahr, with arrival of four new combines in the C7000 and C9000 Series. The company’s marketing manager, Graham Barnwell, quantifies the degree on incline these combines can handle.
“They can compensate gradients of up 28% uphill, 22% laterally and 5% downhill,” he states. “The new rear levelling system (Extra Balance) is controlled from the cab and operates independently of Deutz-Fahr’s proven balance system on the front axle.
“Uniform weight distribution on the traction wheels ensures that the optimum power required for the prevailing ground conditions is transmitted, while maintaining the overall machine width of 3.5m. In addition, the 4wd axle and the intelligent anti-skid system together allow the combine to cope with the most demanding conditions, providing reassuring reliability and, above all, driver safety.”
Elsewhere, the Commander Cab V has been updated, making it even easier for the operator to maintain total machine-function control, in tandem with the new Commander Control Management on-board computer and its 18cm LED touch-screen display. For the first time, it’s now possible to store all machine performance data from each individual harvesting operation as an aid to greater efficiency.
“An additional benefit is that it’s now possible to store machine settings for different crop types,” Graham continues. “This makes it possible for the operator to make a quicker start by selecting factory-programmed settings for each main crop type, the data from which can be uploaded to a second combine, if desired.”