There’s an impressive level of features and automation on a modern self-propelled harvester, and Grimme’s aimed to bring it all smartly under control with its new Varitron Platinum range. CPM heads to the Yorkshire Wolds for a detailed look.
Everything on the Varitron is hydraulically driven and can be adjusted from the cab through the Ergodrive unit.
By Tom Allen-Stevens
You’d have thought a machine the size of Grimme’s Varitron 220 Platinum would need a headland the width of a football pitch to manoeuvre back into work. But operator Oli Brown deftly swings it through little more than a pirouette and lines it up for another run.
“As big as it looks, it’s surprisingly easy to drive,” he says as he drops the diablos onto the next two ridges and sets off up the field. There’s no waiting for the trailer to line up, either, as the 2t buffer bunker begins to fill up.
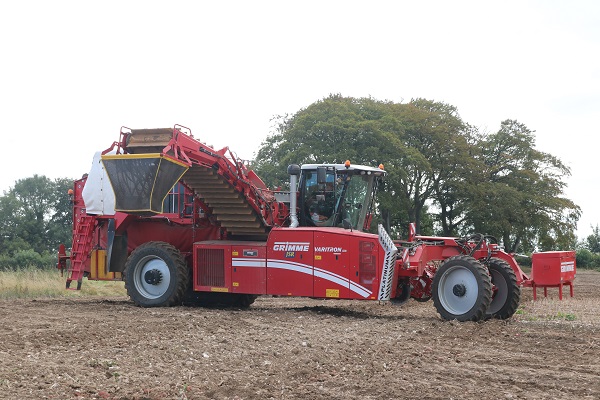
It takes little more than a pirouette to line up the Varitron 220 Platinum for another run.
The harvester is a recent purchase for Yorkshire-based JSR Farming. In total the business has 198ha of potatoes, and it’s a 3.5ha crop of Mozart for seed that’s currently being lifted. “Being a seed crop it’s worth a fair bit, so we have to make sure it’s harvested right,” comments Oli.
This is only his second season driving a self-propelled harvester – he was a relief driver last year with the business’ previous Varitron. “This one’s more focused on the driver. The main difference is the Ergodrive control unit – you can programme the three scroll dials to the settings you use most. That means I can adjust the web speed, for example, without having to click through the screens.”
Another difference is the new Comfort Cab. “It’s not a big change from the previous machine, but potato harvest tends to involve long days, starting at 7:00am and ending around 8:00pm, so you appreciate the little comforts. There are two fridges as well, which means plenty of room for drinks for yourself and the team on the picking table.
“Also new are the LED lights – at night the whole machine is so well lit it’s little different from lifting during the day,” Oli adds.
The lifting and haulm separation works well, he notes. The crop has been pre-topped and killed off about 30-40 days before harvest, taking care to leave stems long enough to be pulled through with ease by the Varitron’s double separator: there’s a choice of a Double MultiSep or Roller Separator/MultiSep combination.
“It’s lifting really well off this Wold land, and there’s a powered drive to the discs at the front that improves crop flow and ensures no blockages,” he notes.
Lifting depth is handled by Terra-Control, which earned Grimme a DLG silver medal when it was unveiled at Agritechnica in 2005. The system uses special hydraulic cylinders, guided by the diablo as it runs over the ridge, to set the depth of the share. A strip of sensor tape inside the ram monitors the diablo position as it moves up and down and passes this information through to the control panel.
There are three functions that can be set – depth control, ridge pressure and depth sensitivity. Oli can adjust the depth control according to field conditions, so if needed he can apply additional pressure to the potato ridge to improve flow without affecting digging depth.
Also useful on the slopes of the Yorkshire Wolds is Share Delta Control. While the diablos move independently, they set the height of the shares on a plane. Share Delta Control allows Oli to adjust one side individually to keep the share level and prevent crop damage.
Despite his relative inexperience, Oli was keen to be the main operator on the new Varitron. “We’ve had really good support from Grimme. I attended a training day and they’ve been out a few times to help set the machine up. That on-going help is useful because you can’t take in everything about a harvester as advanced as this in one go. So every time they come out you learn a bit more about it.”
Everything on the Varitron is hydraulically driven and can be adjusted from the cab through the Ergodrive unit. Monitoring the throughput is also made easy thanks to the six on-board cameras. Oli has the two trained on the main web and the picking table shown on the split-screen display in front of him, and flicks to the cart elevator from time to time to check progress of unloading. Visual Protect is a neat feature on the new machine that automatically switches the display to the relevant part of the machine if Oli makes an adjustment on the move.
Fairly easy harvesting conditions so far have meant no problems with blockages, although Visual Protect also helps if ever a problem occurs: the display is switched to show the blockage and a beep alerts the operator. The drive to the webs can also be reversed to easily clean out any blockages.
Driving Speed Control is a feature of the harvester aimed at minimising problems associated with uneven crop flow, however. The hydraulic drive to the main webs maintains a constant speed, irrespective of forward speed. But if the crop intake becomes lighter, Oli can step up the forward speed and the speed of main intake web self-adjusts to match, allowing for a more constant speed of crop throughput. Likewise the intake slows down if the harvester comes across a thick patch and Oli drops the forward speed.
This level of automation takes much of the pressure off the harvester operator, notes Grimme UK marketing manager Adam Johnson. “But there’s also a high level of control from the cab with the Varitron. The main difference you’d find in a Varitron Platinum harvester over a trailed machine is that the hydraulic drive to all webs and separators is fully controllable from the cab via the Ergodrive control unit,” he notes.
“The web angle in a self-propelled is completely different to a trailed machine. Increased web angle plus a third web and extra separator gives the added cleaning necessary to match its output. On the new Platinum the hydraulics have also been completely redesigned to make maintenance simpler. Another key difference of a self-propelled harvester is that it leaves the land in far better condition than a trailed machine, getting the job done in wet, challenging conditions.”
This is thanks to the 900mm Terra Trac unit on the Varitron that now has treaded idler rollers while the tension of the track can be set from the cab. “It’s quite common for the pressure to reduce during the day,” Adam explains. “The track unit has also been moved a few cm. You’d hardly notice the change but it makes quite a difference to the turning circle and stability.”
Another recent addition to the Varitron range is telematics, continues Adam. “It’s completely free of charge and transfers all manner of data direct from the machine to the MyGrimme web portal. This can then be viewed from the farm office or your mobile phone for monitoring harvest, while it also allows remote access by technicians to diagnose a problem.”
What’s more, there’s also a geo-fencing feature. “If your harvester passes outside a certain radius from your farm, it sends you an alert. So you know that your machine is always where it should be,” concludes Adam.
50-year evolution of a self-propelled leader
This year marks 50 years since Franz Grimme senior combined the front part of a Deutz tractor with a single-row Europa Standard potato harvester, creating the company’s first self-propelled machine.
The prototype was presented at the exhibition of the DLG and also came over to Britain in the same year. But it never returned – as it was being lifted with a crane onto the boat on its return journey, the fastenings broke and the machine plunged to the bottom of the harbour, where it still lies today.
Nevertheless, the concept proved popular with potato growers, including those in the UK, and the DS series was introduced to the market. The DS 80 was an elevator harvester with an 80hp Deutz engine.
The SF harvesters were introduced in 1998, based on the SE trailed range, that introduced an inclined elevator with haulm separation. The SF 3000 was a four-row unit with a 326hp engine.
It was the Tectron, introduced in 2001, that was claimed as a milestone in self-propelled harvesting technology and was voted by DLG as Machine of the Year in 2002. This was the first Grimme harvester with a rubber track, while the Tectron 415 had a 490hp engine and a 15t bunker. Soon after, Grimme entered the beet-harvesting market with the Maxtron, and the Rexor following in 2009.
“Self-propelled harvesters have always been very popular with British growers, but they have very particular requirements of their machines,” notes Grimme UK’s Adam Johnson. “The main one is an all in-line separation system with no direction changes that could increase damage to tubers. British growers also uniquely look for a harvester that can unload straight into boxes.”
A number of Grimme self-propelled harvesters have been developed specifically for the British grower, suffixed with GBS, such as the two-row SF1700 GBS, built until 2009, that featured a 280hp engine and cart elevator.
The Varitron series was introduced in 2007 as a basic two-row machine. Uniquely it offers a large range of different combinations of various separators within one machine. These are offered across three versions: an overloading version without a bunker, a version with a 2t intermediate bunker or a larger 7t overloading bunker. At Agritechnica in 2011, the four-row version with a 7t bunker was presented.
“The Varitron 220 is unique to the UK market, with its cart elevator and 2t bunker making it suitable for box-filling. The Platinum range was shown in the UK for the first time at LAMMA in Jan 2017 and this second generation, featuring the Ergodrive, is available across the Varitron and Rexor ranges,” he continues.
“For 50 years Grimme has been delivering outstanding innovation and technology in self-propelled harvesters, but it’s tailored to the grower, and they know they also receive unrivalled back-up and support. That’s why Grimme has 78% of the potato self-propelled market,” notes Adam.
Extended warranty
Grimme will be offering extended warranties on all of its self-propelled harvesters from this November. Set for launch at British Potato, the standard warranty will be extended from one to two years. This can then be further extended to up to five years for those who opt for the Protect warranty package.
“A self-propelled harvester represents a considerable investment,” notes Grimme’s Adam Johnson. “The extended warranty offers peace of mind, and underpins the confidence Grimme has in the machines.”
Machinery Masterclass
Technology is advancing fast, and the capabilities of equipment found on farm far outstrips what was available just five years ago. For growers who embrace the change, the potential to cut cost, refine production systems and boost output is immense. But how can you make an informed choice about whether an innovation will deliver the refinements you seek if you’ve not operated it before?
This is where Machinery Masterclass comes in. In this article, sponsored by Grimme, CPM has worked with the manufacturer to get a true user experience and an insight into the technology advances it has introduced. We hope this will bring you a ‘try before you buy’ feel for specific features found on this item of machinery and help you remain at the forefront of progression in crop production.