John Deere is a company selling machines and technology, right? Wrong! The green and yellow giant instead wants to sell farmers sustainability. CPM headed to Germany to find out just what this means and how it can be achieved.
“It’s about innovations that are already available that can improve the sustainability of businesses in-line with the environment.”
By Melanie Jenkins
It’s early September in Magdeburg, Germany, and John Deere is hosting its second Sustainability Day. As the press bus pulls up the host farm’s track, it’s quite obvious that John Deere wants farmers to look beyond its own branded arsenal when considering sustainable production, as towering all around, in every direction, are a multitude of wind turbines. And the rest of the day followed this trend.
“This day isn’t about new product information,” announces Carsten Struve of John Deere. “It’s about innovations that are already available that can improve the sustainability of businesses in-line with the environment.”
In Germany, much the same as for growers in the UK, the pressures of climate change, food security and changing regulations are impacting farmers. According to Ralf Lenge of John Deere, the area where the host farm is located should be perfect for arable farming, but even there, harvest patterns are shifting because of climate change.
“There are a lot of requirements for German farmers to lower their emissions and the impact of their inputs – from both society and the government,” says Ralf. “So we, at John Deere, asked: what can we do to help lower emissions and make the industry more sustainable? And at the same time, we have to be able to help farmers produce the same outputs with minimal inputs.”
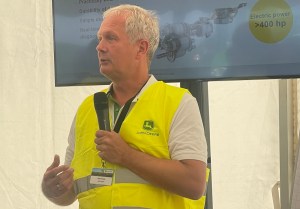
Peter Pickle believes that John Deere wants to provide solutions under the umbrella of digitalisation to help farmers optimise their decision making.
But even since the planning of this second Sustainability Day began, things have changed dramatically, says the firm’s Peter Pickle. “We thought that agriculture could easily solve the problem of food security, but this has altered. Food security has become an even more critical topic in our society and for our policy makers.”
And on top of this, farmers are dealing with acute water shortages or uncharacteristically heavy rainfall, he adds. “It’s clear that agriculture is in a special situation. On the one hand, agriculture is the solution to climate change and food security, but on the other it’s a large emitter of CO₂.”
To tackle this, John Deere believes that all players involved in food production have a responsibility, says Peter. “So as manufacturers, we want to change ourselves to better support food producers as we can help them produce more with fewer inputs.
“One day, in the future, we want to be able to treat each plant as an individual,” he says. “To give it exactly what it needs in terms of water and nutrients – to maximise yield with minimal inputs. We want to do this at the same time as increasing the income for the farmer. And the basic requirement for this precise application is data. Information is of extreme importance as it means the individual steps of production can be connected and allows data to become tangible.”
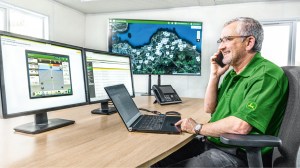
By 2026 John Deere wants all of its agricultural machinery to be 100% connected.
And this is about looking at the complete production system, he stresses. “In the process of growing wheat or oilseed rape, a farmer has to make about 140 decisions. These decisions can’t be done optimally without data and information, or without looking at the full system. So we want to provide solutions under the umbrella of digitalisation so that farmers can optimise their decision making. As part of this, by 2026 we want all of our agricultural machinery to be 100% connected, creating a network for farmers which will allow them to work more sustainably.”
Some of the tools John Deere feels can help with this include harvest analysis to optimise returns and map out future decisions, nutrient analysis for better application precision, exact planting with organic manures, precise weeding, tailored chemical use and better adoption of electrification and alternative fuels.
The starting point of every season is also the end point, according to Carsten. “When harvest is over, the question for farmers should be whether they met their yield and quality targets. You might ask whether there was anything you didn’t expect or couldn’t explain. You might also have a huge store full of grain that you thought was fit for quality end users but it ends up being downgraded to feed.
“A lot of farmers probably know what a trailer load of grain has achieved but not where in the field this has come from. And one data point from 20t of grain is not precision farming, it’s just a single data point,” he stresses.
But having a sensor on the combine can fill this gap. “Combines are now about collecting both kernels and data,” says Carsten. “This means you can get a better understanding of what happens in the field so that you can plan and set up your fertiliser equipment for the next crop.
“Information collected by John Deere’s HarvestLab sensor is shown on the Gen 4 display in the combine before being sent to the Operation Center and then is available on portable devices, such as phones, so everyone from the operator to farm manager can see it,” he explains.
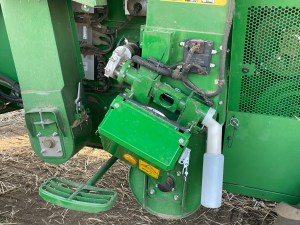
Data collected by HarvestLab can produce yield maps to help farmers identify where in the field crops are getting the right level of nitrogen.
“Data collected by HarvestLab can produce yield maps to help you identify where in the field the wheat crop got the right level of nitrogen based on the protein level at harvest. Using this data you can improve your nutrient use efficiency by optimising N applications in future based on previous performance. You can make savings just by changing your N distribution across the field. Plus this also means less leaching and development of ammonia, as well as more income from crop yield in the end,” adds Carsten.
But in OSR this is slightly different to cereals, says agronomist, Stefan Kübler. “In OSR you’re focusing on oil. Too much protein content is an indicator of too much N. Farmers typically use 150-220kgN/ha on OSR to get a lot of yield, but in some areas of the field the N application might turn into protein and not into oil, which you don’t want.
“So knowing where in the field there’s been a higher, or lower oil content is important as this helps you to apply N better in the future,” he says. “And this can all be done using yield maps produced by analysing OSR as it’s harvested.”
According to Carsten, this helps to improve economic efficiency in combination with sustainability. “It can help keep a farm profitable while farming better for the environment.”
Nutrient analysis is another crucial aspect of sustainable farming, stresses Peter. “Using technology to measure constituents of organic manures can help to close the nutrient cycle and save energy.”
And optimising the use of organic manures has perhaps never been so important, according to Anne Blume of John Deere. “The super high prices and the legal framework around fertiliser use means we have to make changes.”
Looking specifically at maize production and using organic fertiliser, Anne suggests growers first consider their yield expectation for each field individually. “Look at what the soil fertility is like, what you harvested last year and from this estimate what you expect to get this year. From that you can derive your fertiliser requirements.”
But the issue with organic fertiliser is that’s it’s heterogenous, she points out. “So you don’t know what’s in it or how to apply it precisely. This means a risk of over or under fertilising and potentially lost yield, as well as run off or exceeding emissions.”
But using HarvestLab, which has an NIR sensor that can measure N, P, K, NH₄, dry matter and volume – taking over 4000 measurements per second – can help to overcome inconsistencies in organic manure application. This, coupled with Tractor Implement Automation, means the application rate can be automatically altered depending on the constituents of the organic manure, the speed of the tractor and the requirements of that location in the field based on pre-determined maps, explains Anne. “Applications are site specific, based on what plants need. This means more effective applications and potential money savings.”
But what about precisely applying the fertiliser for optimum use by the seed, she asks. “By using strip tillage to only cultivate the area we want to place the maize seed, we keep the structure and soil fertility stable between the rows, which is better in drought and heavy rainfall scenarios.
“So to optimise slurry use, we want to spread it precisely under the maize seed. But this can be a challenge as implements don’t always follow the line straight behind the tractor due to ground conditions, meaning up to 30% of the yield can be lost if operators don’t hit the target slurry line when drilling,” explains Anne.
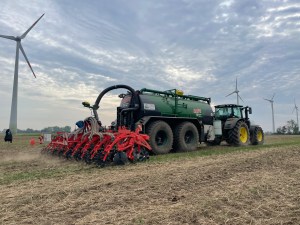
John Deere’s AutoPath system records the exact rows of the slurry tanker.
But a new software feature can help alleviate these potential inaccuracies. “John Deere’s AutoPath system records the exact rows of the slurry tanker and automatically transfers this data via the cloud, meaning the tractor will adjust the drill’s position to follow the precise line of slurry and improve strip-till accuracy,” she says.
AutoPath can also be used to improve the accuracy of mechanical weeding, says John Deere’s Torben Ahrholz. “Previously, auto guidance systems used the AB of the tractor at planting to guide the mechanical hoe, but this didn’t take into account the movement of the drill, so some of the crop might have been destroyed. But with AutoPath, the exact rows of maize are documented at planting. A guidance plan is then used at weeding to instruct the tractor to automatically adjust the hoe’s position in the field. This allows for better accuracy and high working speeds.”
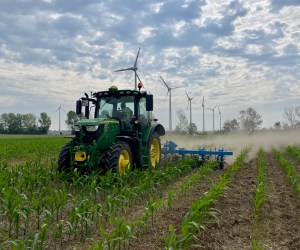
Digital innovation has allowed the efficient return of tools such as mechanical hoes.
It’s digital innovations that have allowed the return of tools, such as mechanical hoes, adds Peter. “We can now mechanically weed at speeds of up to 16km/h, which can help reduce herbicide use. However, the price of this is higher fuel output – so in some cases it may be better to use spot spraying.”
Using spot spraying, farmers can apply herbicides to target specific areas in the field based on maps produced from data gathered using drones or satellite imagery, explains Stijn Kroonen of John Deere. “And whereas a hoe can only work between rows, spot or band spraying can get between each plant within a row.”
Based on trials John Deere has carried out in the US, spot spraying can reduce herbicide use by up to 70%, depending on weed pressure, the crop and weather conditions, says Stijn. “But it really is important to hit the precise place, at the right time and at the correct dose rate, which requires an accurate machine to handle the data, with individual nozzle control and which can record what it has actually done.”
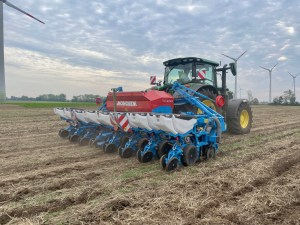
Autopath will adjust the position of the drill to precisely follow the lines of slurry.
As a further step to overcoming the challenge of reducing CO₂ emissions from agriculture, John Deere is investing in electrification, says Peter. “We want to have a fully electric, autonomous tractor in the 100hp range on the market by 2026. Electric drives are highly energy efficient, dynamically controllable, simple, almost wear-free and are quiet.”
But this goal isn’t without its own challenges, he explains. “Today’s battery technology can’t store enough energy for higher horsepower tractors to run for a full day as they just don’t have the capacity. But we believe that by 2035-2040, we should be able to provide a full range of electric solutions.”
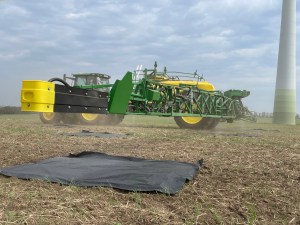
Using spot spraying, farmers can apply herbicides to target specific areas in the field.
But in the interim John Deere is working on another solution: its MultiFuel engine. “We are still dependent on the combustion engine, so our concept means we can run different fuels in one tractor using biproducts from other production systems.”
Able to run on diesel, biodiesel, vegetable and pure plant oils, or various blends of there, John Deere hopes the concept will help reduce CO₂ emissions and break the link to fossil fuels. “Some of the fuels used in this machine can be both produced by farmers and used by them,” says Peter. “On average, farmers would need to use about 8% of their land to produce the same amount of fuel that they would consume.”
Software in the MultiFuel tractor can automatically detect the fuel mixture used and adjust the engine control system so the applicable emissions standards are met. Engine power is also altered according to the different energy content of the fuel used. “We are currently testing the MutliFuel tractor on a trial farm, where it carries out transport and field works,” he explains.
“Although this isn’t on the market yet, it’s another solution to sustainable farming,” says Peter. “It will allow the agricultural sector to supply fuel for itself through plants such as OSR or sunflowers.”
This article was taken from the latest issue of CPM. For more articles like this, subscribe here.