Twine knotters on big balers have never had to work so hard as manufacturers find ways of packing more material into the same dimensions for increased baling, field clearance and storage efficiency. CPM reports.
By Peter Hill
An extra 5% here, an extra 10% there. Contractors and large farms operating big square balers to clear straw after the combine can benefit from significant increases in density to increase efficiency and reduce costs.
A combination of lengthened bale chamber and uprated pressure systems is the most common way of putting an extra squeeze on straw as the plunger rams home, resulting in more material in every bale, fewer bales and less twine consumed for every hectare, and the potential to clear large fields just that little bit quicker.
Heavier bales
With the new 2370 Ultra HD, the Massey Ferguson big baler range has a new density leader capable of producing bales 20% heavier than previous models, according to engineers at the AGCO factory in Hesston, Kansas where the machine is also turned out in Fendt colours as the Squadra 1290 UD.
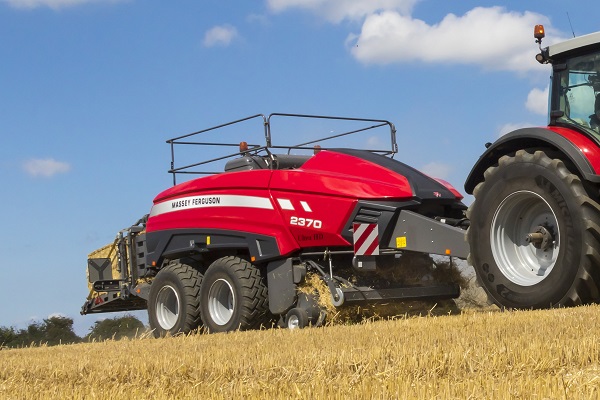
Massey Ferguson 2370 Ultra HD packs up to 20% more material into every bale compared with previous models.
The big but sleek-looking baler is therefore aimed primarily at professional operators, either large farms and estates or contractors, and particularly those involved in biomass harvesting for fuel.
The 2370 Ultra HD weighs in at 13.4 tonnes, which shows how much metal there is in the machine, and operators are advised to put a 350hp tractor on the drawbar.
While the newcomer operates in much the same way as the MF 2270 XD, which produces the same 90cm x 120cm bale dimensions, a flywheel spinning 50% faster and generating 130% more energy, plus a 20% longer bale chamber helps pack more material into every bale.
There’s a purpose-built gearbox for this model and although the plunger has the same 740mm stroke as all other balers in the MF range, it runs 6.5% faster at 50 strokes per minute.
Sensors on the two connecting rods between the gearbox and plunger monitor the load on the face of the reciprocating ram to help produce bales of consistent density and weight in variable conditions by automatically regulating the double-acting hydraulic cylinders on the density ring around the bale chamber.
Extra output
Kuhn claims a 10% increase in performance for its latest square baler compared with the regular models.
The upgrades that create the LSB 1270 DX are said also give this machine the potential to achieve up to 15% more capacity in dry or bulky swaths that can be fed at a more rapid rate into the packing mechanism.
The new ‘DX’ specification is available only on the LSB 1270 assembling a 70cm x 120cm bale, not on the LSB 1290, which produces a deeper package.
Rotor intake is standard – either plain or with the 32-knife Omnicut crop slicing system – and a powered version of the pick-up roller is available to enhance performance with dry, bulky swaths.
The added bale density is derived from fitting bigger diameter hydraulic cylinders exerting pressure on the top and side panels of the chamber.
A revised frame and bale channel, and a new gearbox design with up to 30% extra load capacity compared to the previous model, cope with the added loads and stresses involved.
There’s also a double knotting mechanism in place of the single knot system of the regular Kuhn LSB 1270, which keeps the higher tension load off the twine and knotter assembly until the bale has been completed and the second knot tied.
This system is constantly monitored by sensors sending data to the control box in the tractor cab to manage twine tension and provide an urgent operator alert should a knot failure occur.
Hydro assisted start-up
A similar increase in potential bale density is claimed for the most recent addition to the Krone BiG Pack range.
The 1290 HDP II, which stuffs straw into a 90cm x 120cm package, is geared up to deliver 50-70% higher throughput than previous versions, say Krone engineers.
As with all of the company’s BiG Pack balers, the tractor pto clutch is relieved of undue start-up stress by allocating the task of getting the hefty 608kg flywheel spinning to a baler-mounted hydraulic motor.
Mechanical drive from the tractor then takes over, with an intermediate gearbox stepping up pto speed by 180rpm to reduce the torque load.
Changes needed to the regular 1290 HDP to enable the HDP II to cope with the increased productivity and density goals include strengthened components in the Variable Fill System.
This is the mechanism that accumulates material coming in from the swath before it’s transferred to the main chamber.
Also, no fewer than six hydraulic cylinders – two on each side and two on top – apply the pressure needed to squeeze the bale into a denser package as it’s assembled.
Stress sensing
A new approach to density management is claimed for latest Claas Quadrant balers; it draws on data collected by sensors recording the slightest distortion of the front chassis beam, and also at three or all six of the machine’s knotters.
The readings effectively provide a measure of stress on the driveline and the twine, which the Automatic Pressure Control software responds to by regulating the hydraulic pressure applied to the bale chamber compression doors.
According to Claas, the aim of the system is to consistently hit a target bale density while allowing even an inexperienced operator to work the machine at peak output.
With all six knotters wired up, this feature of the 70cm x 120cm bale Quadrant 4200 and 5200, and the 90cm x 120cm Quadrant 5300, also provides an immediate alert of twine running out or breaking, as well as steering guidance along narrow swaths to ensure even filling of the chamber.
On the more sophisticated Quadrant 5200 and 5300, hydraulically adjustable pre-chamber control is another aid to performance; there are three settings available to operators to suit different crops.
In contrast to a fixed-cycle mechanism, which requires the operator to balance forward speed and the amount of material in the swath, material is accumulated in the pre-chamber and transferred to the main chamber only when a pressure pre-set has been triggered.
Consistent bales can therefore be produced from relatively thin swaths without having to go at speeds beyond what is sensible in order to compensate.
Working speed control
Automatic adjustment of ground speed along the swath aims to help operators of New Holland balers achieve consistent performance in variable crops while also relieving the workload during a long working day.
IntelliCruise, which is available on the 70cm and 90cm x 80cm and 120cm machines, can also help achieve consistency in the number and size of slices in each bale.
That’s important to some end users in terms of handling and dispensing straw once the bale has been broken apart.
The latter feature, delivering a consistent number and thickness of wafers in each bale, is achieved on Packer and Packer Cutter versions of the latest-spec New Holland BigBaler Plus models (and their Case IH ‘LB’ equivalents) by regulating forward speed in relation to the volume of material in the swath.
Rotor-fed CropCutter versions can also work in the same but also have a ‘maximum capacity’ mode, which uses sensor paddles to measure both the throughput of crop fed into the pre-compression chamber and the time taken to fill this chamber.
Both modes require a feature unlock for the New Holland IntelliView in-cab terminal and also ISOBUS Class 3 electronics on the tractor as they require two-way data flow between the implement and power unit.
The ‘Plus’ version of the range-topping BigBale 1290, which makes a 90cm x 120cm bale, features an 80cm longer chamber than preceding models to deliver up to 10% increased bale density.
Certain driveline and other components have been upgraded accordingly, including the slip clutch, a larger shaft for the packer – increased in diameter from 58mm to 76mm – and an uprated drive chain on PackerCutter models.
Knot for want of thinner twine
It’s all very well packing a denser bale, but productivity can soon slip back if the baler twine snaps. No hold-ups during baling and the ability to go for longer before the need to re-load are two key requirements from baler twine, explains Graham Robson of baler twin and netwrap manufacturer Tama Plastic Industry.
This comes down to the strength of the twine, he says. “Historically, twine has been made stronger by making it thicker, resulting in a heavier ‘runnage’ (metres per kilogramme).
“But this brings inherent problems when trying to keep bales together with the increasing density of modern balers – more so with HDP and XD balers. Thicker twine makes knot formation less stable, with shorter tails that allow the knot to open under pressure.”
There’s now a new technology Tama has introduced into its twine production that the company claims delivers a stronger twine without a heavier runnage. “We’re using a stronger raw material, so the twine can withhold the same pressure of the bale as twine of a much thicker cross-section.”
The new twine has a much greater knotting performance, he adds, making tighter more secure knots, combined with significantly more length in every spool, so increasing output from the baler.
“Our process makes a more compact and refined twine, with greater flexibility. The smaller cross-section twine shape instantly makes the complex knotting procedure easier and less stressful on the moving parts in the knotter. This means tighter knots, while having more length within the spool dimensions to increase bale count. Baler output per day increases as a result.”
There’s a five-segment colour-coded scale, categorised as ‘standard’ or ‘extreme’ and suited to each baler make and model, to help farmers and contractors easily pick out the most suitable twine for the job, says Graham.
Beefed-up balers round off the options
Mid-ranking John Deere round balers have been swept aside in favour of new models said to be built tougher and capable of delivering heavier packages for growers producing 5000-8000 bales a year.
The multi-crop capable V451M and V461M, producing bales up to 1.6m and 1.8m diameter, have replaced the 854 and 864 and feature an all-new heavy-duty welded frame together with an upgraded driveline using heavier duty components for increased durability.
There’s also a new belt-tensioning system and latched tailgate that contribute to a 15% gain in potential bale density, and while the previous designs have just one bale-starting roller and a small initial bale forming space, the new models have a more open intake area with three rollers now encouraging material to get rolling into a neat bale.
This comes with a loss of some core density but absorbs less power, say John Deere engineers; and with less emphasis on belt traction during the initial bale-forming phase, a switch from patterned to half a dozen more durable plain belts has been possible.
The V451M and V461M balers can be had with a 2m or heavier-duty 2.2m pick-up, the latter having five rows of larger tines, and have a parallel-action drop floor as standard to help unplug blockages.
Hardox steel is used for the intake rotor tines and optional Maxicut crop slicing system, while netting from the rear-mounted dispenser can be from 4600m rolls of either regular net or John Deere’s water-resistant B-Wrap microfibre membrane for outdoor weather protection.
Damping at both ends of the new tailgate lift cylinders allow maximum hydraulic flow from the tractor for fast opening and closing to give a productivity boost.
Tailgate automated
Automatic tailgate operation and other automated functions are available on Kuhn’s largest roller baler.
It comes as part of an optional package for the FB 3135, which produces 1.2m x 1.2m bales, designed to reduce the driver’s workload during a high volume baling season.
Autogate, which allows completed bales to be ejected without any operator intervention, is one of three main functions, with Autodeblock automatically retracting the chopping knives and lowering the drop-floor whenever the overload clutch is triggered.
The Autoknife function sets about cleaning the Opticut blades after a pre-defined number of bales have been made to maintain a clean cut and least possible power consumption.
Manual control of all functions remains available, along with a semi-auto mode that requires the operator to press a ‘confirm’ button to get the machine baling again.
Fendt gets Lely balers
As part of Fendt’s new full-line strategy, round balers based on the Lely designs acquired by parent corporation AGCO are now part of the German marque’s product range in the UK.
There are two sizes of the variable chamber belt machine, producing 1.2m wide bales up to 1.6m and 1.8m in diameter and three fixed chamber roll balers with 1.2m x 1.25m bale dimensions.
HydroflexControl features on the belt balers as a means of keeping the intake flow moving when large quantities of material threaten to cause a blockage beneath the rotor.
Ultimately, the spring-loaded floor can briefly be fully opened to let a large volume of material in while baling is paused – a lot less time consuming than having to clear a constipated intake channel.
Five-row heavy duty pick-up reels up to 2.4m wide and with a crop roller helping to feed material beneath the wind guard are designed to gather up swaths cleanly, with a short distance between the reel and intake rotor encouraging a clean flow of straw and/or grass.
Capable machines for mixed farmers
Among developments for McHale Engineering’s V660 variable bale-size balers are a single belt option and a new pick-up and feed-in assembly designed to deliver increased output and greater reliability.
While the McHale F5 steel roller, fixed diameter balers are most commonly used for silage, mixed enterprise farms baling a lot of straw as well as grass are capitalising on the V660 baler to produce the optimum size packages for these materials – typically up to 1.25m in grass, 1.68m in straw.
The full width endless belt is already an option on McHale Fusion Vario baler-wrappers and on the V660 is said to track better in silage than the triple belts installed as standard, with loose crop losses reduced.
The baler’s net application mechanism has been re-designed for latest models but it’s at the front end where most changes are evident.
Larger feed augers on the pick-up, a larger diameter intake/slicing rotor and a ‘flexible’ floor to keep the crop flowing with less risk of plugging are all designed to increase intake capacity and overall output by allowing faster working speeds.
Buyers can also opt for a new camless pick-up reel in place of the traditional design, which has tines regulated by cam tracks at each end of the 2.1m wide assembly.
Balers uprated
Latest generation Case IH round balers have also been uprated for increased productivity, with the 1.25m diameter RB 545 gaining a 2.2m pick-up from the variable bale size models to help gather wide swaths more cleanly.
It comes with five rows of flexible tines controlled by cam tracks and a freely-rotating roller to lightly compress deep swaths before helping the tines collect the material cleanly.
New drive chains for the intake rotor and bale-chamber rollers have been upgraded and the rollers themselves are now profiled with 10 rather than just four ribs to get better traction with light, slippery material such as straw.
Intake rotor drive can now be stopped from the cab when a plug occurs so that the operator can maintain power to the rollers and, if necessary, use the drop floor to clear it.
Using 10 crop-slicing knives at a time means there can be another 10 sharp ones ready to take over to maintain chopping performance while minimising power consumption – or all 20 can be used together for the finest chop length.
ISOBUS electronics are standard, with a visualisation of the baling process, 25-job memory and new settings and diagnostic functions included,
Top crop chop
Lessons learned from the development of market-leading silage wagons helped Pöttinger with the design of its first round balers and, in particular, the crop-slicing arrangement.
For one thing, the 32-knife Flexcut mechanism installed on Pro versions (there are 16 knives on Master models) produces a theoretical chopping length of 36mm, so bulky material such as straw will pack more easily into tight bales and may not need further processing when used in feed rations.
For another, the system uses double-sided blades, which the Austrian manufacturer says are more cost-effective than blades with a single cutting edge.
What’s more, positioning the blades in the top of the intake channel, rather than below it, means they can pulled out to one side in a cassette, giving comfortable and safe bench-height access for reversing or replacing them.
The steel roller fixed chamber Impress 125 F makes bales 1.2m wide, 1.25m diameter while the variable bale size belt balers 155 V and 185 V go to 1.55m and 1.85m, respectively, will all models using a 2.05m or 2.30m pick-up.