At Agritechnica 2019, Sky revealed multiple revisions to its EasyDrill direct disc drills. CPM visits an Oxfordshire farm with experience of both pre- and post-upgrade models, to discover what influenced the decision to stay with the maker when upgrading and how the changes have improved the machines.
“One of the key lessons we’ve learned is that you can’t go half-heartedly down this road, and there’s no doubt we’re still learning.”
By Martin Rickatson
“I don’t think we could have picked a worse year to begin,” says Peter Deeley, able to smile now after the passage of time as he recalls his earliest experiences moving to direct drilling in the wet autumn of 2019.
“And the following year wasn’t much better. It’s easy to forget given how dry things were when starting the most recent autumn drilling.”
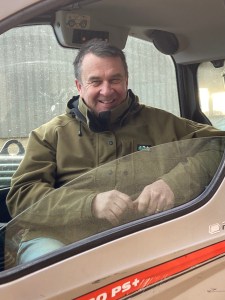
Peter Deeley selected the Sky EasyDrill primarily for the minimal soil movement it produced on demos at Groundswell and on his own farm.
In his yard at Launton, near Bicester in north Oxfordshire, Peter’s Sky EasyDrill sits ready to tackle its fourth spring. While the business may have been direct drilling for four seasons, this is already its second Sky machine, having been sufficiently impressed to upgrade to a new improved – and wider – model.
A mixed enterprise spread across three farm sites, Peter’s farm business today covers 520ha (1300ac). With beef and sheep as well as the arable, he’s assisted by a team of two, including main tractor operator Wayne Varney.
“We reassessed our crop establishment when Wayne joined a few years ago. We were either ploughing where necessary – usually only when establishing beans – or using a He-Va Combi-Lift loosener for primary cultivations, following with a Kuhn combination drill. It was a non-inversion system, but not cheap.
“So the potential savings in time, diesel and wearing metal were all attractive aspects of moving less soil, and I also wanted to and dip a toe into regenerative principles, making more use of cover and companion crops to protect soils and inhibit weed growth.
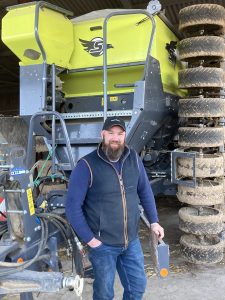
Diesel use for crop establishment as a whole has dropped by more than half compared to when the farm was ploughing and combination drilling, says Wayne Varney.
“We looked at multiple drills at Groundswell, but I felt many – especially the tine models – moved too much ground. The disc-coultered Sky EasyDrill appealed because it produced minimal surface disturbance and closed the slot better than others, while the dual distribution system meant we could plant a companion crop at a different depth.
“It’s also pretty versatile – if it’s necessary to cultivate/plough it will work on consolidated tilth. Subsequently, we arranged a demo through Turney Agriforce, our local dealer, drilling wheat after failed oilseed rape.
“The drill’s performance and that of the subsequent crop, plus the reduction in fuel used, made up my mind, and we bought a 4m EasyDrill 4010 for autumn 2019.”
Designed to work in consolidated ploughed land, cultivated ground, into cover crops or direct onto stubble, the EasyDrill features 435mm notched disc coulters inclined at 1.5° and angled at 3.5°. Up to 250kg of downforce is shifted progressively between the front depth/press wheels in damper conditions and the disc coulters and rear closing wheels in dry, hard soils.
With much of his land having not seen the plough for a number of years, an assessment of the soil structure across the farm’s acreage suggested it was in sufficiently good condition for a rapid move to direct drilling. The weather, though, had other ideas.
“I was expecting to endure some pain while we learned the best ways to manage a new system, but the wet autumn of 2019, and again in 2020, didn’t help the soil surface soil structure. And 2021 wasn’t much better. Of course, summer 2022 left a different scenario. I’d like to think we’re now coming out the other end, but it’s been a learning curve,” says Peter.
“After the first two years we found the ground was pretty tight because of the wet autumns, and we needed to alleviate surface compaction, working shallowly rather than fully subsoiling.”
After talking again with Turneys, in September 2020 the dealer delivered a 4m/8-leg Stealth low disturbance subsoiler from He-Va, imported by Sky agent Opico. Meanwhile, Sky had upgraded the EasyDrill, with the new 20-series featuring an in-house ISOBUS controller capable of variable rate application, plus blockage sensors, individual coulter shut-off and automatic tramline shut-off.
The new controller allows control of more than one metering unit, making possible installation of an optional further hopper, allowing simultaneous application of up to four different seed types or nutrient products. In addition, a new coulter design offers improve trash flow and seeding accuracy, with a two-piece coulter tube and tungsten shoe, plus maintenance-free disc bearings.
“One of the biggest pluses we quickly found with our new system was a big reduction, not only in crop establishment time, but also in overall horsepower and fuel requirements,” says Peter.
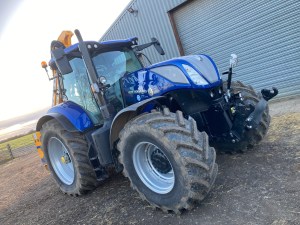
The farm’s 270hp New Holland T7.270 easily handled the 4m EasyDrill 4010, so a 6m model was chosen from the new 20-series to boost capacity and allow contract drilling to be undertaken.
“That meant when Turneys showed us the upgraded EasyDrill drill, we weren’t only interested in the new features, but also considered moving up a size, as our 270hp New Holland T7.270 had easily handled the 4m machine. It would leave us with plenty of spare capacity for our 280ha (700 acres) of drilling, and because some neighbours had expressed an interest, I was also considering taking on some contract drilling.”
A new 6m EasyDrill Pro 6020 I E-Drive Premium duly arrived on farm in March 2021, in time for spring drilling. With a shift to more spring cropping along with the refocus on reduced tillage, its arrival was timely.
“We’re now growing spring oats, beans and linseed in addition to winter mainstays wheat, barley and OSR,” explains Peter.
“We’d dropped OSR because of flea beetle, but it’s made a comeback as a low-input crop, using farm-saved conventional seed and a buckwheat-based companion crop mix.
“The extended rotation from a broader range of crops also helps minimise volunteer development, especially important as we grow a lot of seed crops. We’ve struggled occasionally with wheat volunteers in seed barley in certain fields, though, and where we think it’s necessary, we encourage a chit with a shallow pass of our Kuhn Optimer compact disc ahead of drilling.”
Diesel use for crop establishment as a whole has dropped by more than half compared to when the farm was ploughing and combination drilling, says Wayne.
“When drilling OSR, the T7.270 uses 19 l/hr, and for wheat it’s around 38 l/hr. Where compaction needs addressing beforehand, working with the Stealth uses 54 l/hr at maximum depth, although where compaction is shallow, we work at perhaps 12.5cm deep and cut that to 20 l/hr. It’s only used in areas where we’ve identified compaction and confirmed it by digging,” says Peter.
“Pulling the drill is more about traction than horsepower and strangely, the 6m seems to pull better than the 4m, perhaps because of the chassis changes. We’ve a few banks but are mostly on flat land, although it’s largely heavy. On easier soils I reckon you could pull a 6m machine with 150hp in good conditions. You don’t want to go too fast as you’ll move too much soil and may as well have a cultivator drill.”
With all straw contractor-baled, later returning to the land through muck from the farm’s cattle enterprise, slugs are not a significant issue. Land for spring cropping is generally put under a cover crop over winter. “That’s probably our bigger residue challenge,” says Peter.
“Where we’ve used a mix with tall species, we’ve found it relatively easy to drill into after spraying off. Slugs haven’t tended to be an issue in this situation, but the land can stay wet beneath the residue.
“But the worms pull it in and gradually it disappears. Added to the cattle muck, and some poultry litter and Fibrophos we also apply and disc in, our organic matter levels have risen considerably in recent years and our soil structure and composition have improved noticeably.”
As planned, moving from the original 4m drill to the revised 6m has brought the ability to get the farm’s own ground covered more quickly and take on some contract work in the time freed up.
“We’re over-capacity for our acreage, but that means not only can we afford to wait for ideal soil conditions, but we can also make the drill pay for itself by contract drilling once ours is done. We covered our own acreage in good time last year and covered nearly 250ha on top. With a 6m drill, if someone wants 20ha drilling, we can start mid-afternoon and knock it off that day,” says Peter.
While the farm didn’t previously put down fertiliser at drilling, the shift to more spring cropping has seen full use made of the EasyDrill’s split hopper to give spring oats and spring linseed an early boost.
“I can get three tonnes of seed up front and a tonne of fertiliser in the back, so capacity is good,” says Wayne.
“Depending on how close I’m working to one of our farm bases, I’ll often run back to refill, as it’s a pretty quick process to fold up and go, and the drill runs well on the road.
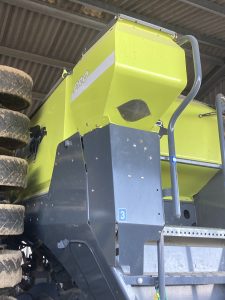
Specifying the additional 120-litre Pro Hopper allows companion crops or slug pellets to be applied in the same pass as the primary crop.
“We also specified the additional 120-litre ‘Pro Hopper’ up front for companion crop or slug pellet application. With the combination of all three compartments we can, for example, put down OSR, a buckwheat companion crop and Kickstart fertiliser in the same pass, with the coulters configured to plant two buckwheat rows between each OSR row.
“The beauty of the drill configuration and the control terminal is that you can go to one farm for a particular job and 10 minutes later be doing something totally different on another farm, whereas on the old drill you had to manually shift everything over.
“The tramlining system is also easy to work with, especially for different tramlines on different farms. It’s a simple matter of entering the wheel width and the tramline width, and the drill does the rest.”
At the heart of the design changes for the latest EasyDrill range was a remodelled chassis, and Wayne rates this as a significant improvement.
“The old machines used a broad, square frame which impeded the view to the middle section. With the new tapered design, it’s easier to see if a blockage occurs. That’s rare, though, as with the redesigned coulters trash flow is excellent, and even bean stubble is a doddle to work into.
“The redesigned coulters have improved soil flow and penetration, and there’s no issue getting down to depth – getting beans to 12.5cm isn’t a problem. The coulter pressure is plenty high enough – it will split some biggish stones at maximum. And it copes well with the soil type range across our area, with good ground penetration, slot closing and consolidation on our clays as well as brashier, stonier contract land.
“There are multiple adjustments to suit the circumstances, but key among them is the five-minute task of altering the weight pitch onto the front tyres or the rear press wheels, depending on the soil type and moisture level I’m working on,” comments Wayne.
“The drill will go when perhaps the ground isn’t quite ready, but with the extra capacity of the 6m, we can afford to wait. You have to drill by the conditions and not the calendar. And when it’s drier, rolling is important – initially we didn’t bother, but we soon realised its value, and now roll everything after drilling unless it comes wet. With 8.2m rolls we can cover ground fairly quickly.”
In terms of grassweed control, the farm has an issue with sterile brome creeping in from the hedgerows in some fields, so care is needed working around the headlands, says Peter.
“We do some border spraying where necessary. Our two worst fields have been ploughed and put into AB15 stewardship, which has helped.
“I think our blackgrass is as under control as possible, although it’s more evident this year where the dry summer meant long dormancy that was broken in some areas when we finally got some autumn rain. There’s a bit in the barley but we’ve been quite lucky,” he says.
“One of the key lessons we’ve learned is that you can’t go half-heartedly down this road, and there’s no doubt we’re still learning. Things like pre-drilling compaction loosening and post-drilling consolidation are essential.
“But I think last autumn our winter wheat went in as well as it ever has done, and it’s clean. Yields are averaging as well as under our old system, with feed wheats at 7.5t/ha. But our fuel, labour and machinery costs have been cut significantly, which is especially pleasing given how much they have risen generally.”
This article was taken from the latest issue of CPM. Read the article in full here.
For more articles like this, subscribe here.
Sign up for Crop Production Magazine’s FREE e-newsletter here.