Getting the best out of North Norfolk sandy loam soils requires the balance of a good finish without compromising soil health. CPM visits the Stody Estate to find out how that’s being achieved.
When we do plough, it needs to produce an excellent result.
By Tom Allen-Stevens
Mike Wilton holds up the cross-shaft in the workshop to make the point. This is the Cat3 cross-shaft for the plough that hasn’t been used in several years.
“Every time we’ve upgraded the plough, we’ve used it less and it’s lasted longer,” he says. “They’re also getting bigger as our tractor horsepower has climbed. When we upgraded our 7f plough, it was too much for the cross-shaft and it snapped. So we spoke to Lemken and upgraded the linkage to Cat4, and never had a problem since.”
It’s fair to say the ploughs are put to the test on the Stody Estate in North Norfolk. Owned by the MacNicol family, there’s 2000ha under cultivation and the soil type is a sandy loam Grade 3 or worse. But with a 10M gallon capacity reservoir and one of 46M gallons on the way, field vegetables, including carrots, parsnips, onions as well as potatoes, form an important part of the rotation. These are placed one in six years and interspaced with winter wheat, oilseed rape, spring and winter barleys and sugar beet. There are also vining peas and dwarf beans in the rotation, while maize and rye are grown for an anaerobic digester.
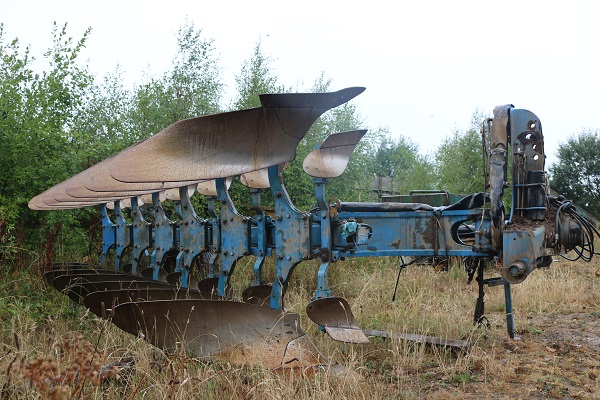
The Juwel plough is fitted with longer W52 mouldboards that ensure a better finish.
“The plough’s a rotational tool,” explains Mike, the estate’s farm manager. “Go back 14 years and everything was ploughed. These days, it’s not quite one in six years, but more frequent than one in four. Now the plough serves a far more strategic role.
“There are some crops in the rotation with very limited weed control options. The plough gives you that lovely clean start, which helps enormously for root and vegetable crops. It also helps with blackgrass control, although that’s not the number one driver.”
It’s a balance, however, as Mike’s keen to ensure the soil integrity’s maintained. “We are working these soils hard. So we’re trying to use the plough as little as we can to help organic matter, which has improved from 1.5-2% to 2.5-3% today, and also to maintain structure. It means when we do plough, it needs to produce an excellent result.”
When he arrived on the estate 14 years ago, a Lemken 6f plough and a 5f Kverneland turned over the entire arable area. “The crops we grow as well as the soil afford us a big cultivation window – dwarf beans can be drilled as late as June.”
A Väderstad TopDown and Sumo Trio were brought in and the area ploughed soon began to reduce. At the same time, tractor horsepower was going up, and the purchase of a New Holland T8 in 2005 prompted the purchase of a 7f Lemken Euro 8 plough.
“It was a fixed-width plough, fitted with solid C40 mouldboards and we always pull a furrow press. One thing we did change, though, was a move to on-land or in-furrow ploughing.”
Whether to plough on-land or in-furrow can be a contentious issue. There are benefits, especially for those on wide tyres or tracks, while keeping the wheel out of furrow bottom also keeps the compaction out and results in less slathering of the freshly exposed soil. But as conditions turn more marginal, some tractor/tyre set-ups can struggle to maintain traction on-land.
“Every operator you try to persuade to come out of the furrow are reluctant to do so. But once they’ve tried it, they never want to go back in. We aim to plough everything apart from the headland on-land,” says Mike.
The new plough proved so successful an identical one was purchased a couple of years later. By the time of the next upgrade, however, tractor horsepower had increased and requirements had again moved on. “We stuck with the seven furrows, but wanted to change from the C40 mouldboards to W52. This was to improve the finish, especially in front of sugar beet where we generally spread pig muck, so there’s plenty to bury. And it creates a wider furrow for when we’re ploughing in-furrow.”
The plough that replaced the Euro 8 was the estate’s first Lemken Juwel. “We also moved to a vari-width model. Many of our fields change soil type from one end to the other and the range of furrow widths we typically work in now is 350-500mm. The longer mouldboards ensure the standard of finish is maintained. We also added some subsoiler tips to save a pass where deeper loosening is needed.”
All of this extra work proved too much for the headstock, however, which is when the cross-shaft showed up as the weak point. “Upgrading this to Cat4 wasn’t a problem. The difficulty was with the top link – at that time, Lemken didn’t do a true Cat4 top link.”
Working through their local dealer, Ernest Doe at North Walsham, they arranged with Lemken to upgrade the headstock. “The service from the dealer was exemplary and I was impressed with how Lemken managed to solve the problem. We ended up with their first ever plough with true Cat4 linkage.”
Confident he now had the plough the estate needed, a second of the same model was purchased in 2015. “This has quite a neat, standard arrangement on the top link so you can have either Cat3 or Cat4 linkage.”
So why has Mike stuck with Lemken? “Whenever we’ve upgraded the plough, we’ve always aimed for the best one on the market. Lemken have always had the market leader – there’s plenty of steel in it, it’s well made and well engineered.
“It’s also easy to set up, and to adjust the skimmers. Changing the wearing parts is especially easy – there’s a clever arrangement of hooks and clips, which cuts downtime and means you don’t spend your life fiddling around with nuts and bolts.”
A set of mouldboards lasts about five years on the sandy loams, while wearing parts need changing every 50ha, says Mike, with two sets of points needed for every set of wings.
For main plough operator Tom Loundon, the finish he achieves is the stand-out. “It’s a really good tool for burying the trash, even through standing grass. The finish is fantastic. With the subsoiler points fitted, it takes a lot of pulling and shakes a bit, but it’s a sturdy piece of kit.”
It’s not all positives, though. “The hydraulic ram for depth adjustment is a bit small, which is a worry, although we haven’t had any problems with it.”
He works on-land or in-furrow at about 10km/h to achieve the best result, covering around 14ha/day, depending on field shape and size. “I like the fact you have good control of the plough from the tractor seat. You can alter the depth on the move through the hydraulics, as well as vary the width.”
For Mike, it’s critical that Tom does a good job with the ploughing. “It’s the first pass in a chain of events. The better the job from the plough, the better the finish is overall and the more even establishment you achieve.”
That’s particularly important for sugar beet. “We plough in spring, just in time for the crop. That allows overwinter stubbles for Higher Level Stewardship, but it also results in less slumping, which can be a problem on our soils.”
This is followed by a pass with a 6m Lemken Kompaktor in front of the 18-row Vicon drill, aiming to drill at the end of March. “If the soil needs additional work, we’ll go through with a Unipress. But the aim is to minimise the number of passes to keep the structure, provided the surface finish is good.”
It’s this careful attention to the soil that Mike believes is paying dividends in terms of higher yields. “Last year we budgeted for 75t/ha on the sugar beet and achieved 98t/ha average delivered,” he reports.
“I’m convinced it comes down to the appropriate use of the plough. Through most of the rotation we follow non-inversion tillage, which contributes the most to building soil organic matter and maintaining structure. But the plough is still an essential tool and increasingly complements other parts of the arable toolbox as we lose more chemistry. With the right plough, used strategically, you can get the best of both worlds – a good soil structure and an excellent finish.”
Farm Facts
Stody Estate, Melton Constable, N Norfolk
- Arable area: 2000ha
- Cropping: Winter wheat, oilseed rape, winter and spring barley, dry combinable beans, sugar beet, potatoes, carrots, parsnips, onions, vining peas, dwarf beans
- Soil type: Sandy loam
- Mainline tractors: New Holland T9.560; John Deere 8360, 7290R, 7930, 6175R; NH T7.210, TS 135A
- Combine harvester: NH CR 9090 with 12.5m header
- Ploughs: 2x 7f Lemken Juwel vari-width
- Cultivation: 4m Vaderstad TopDown; 4.5m Sumo Trio; 7-leg HeVa subsoiler; 8.2m Simba Unipress; 6m Lemken Kompaktor
- Drills: 8m Väderstad Spirit; 18-row Vicon for sugar beet
- Staff: 6 full time including Mike
Diamint upgrade pulls plough in line
More than half the semi-mounted ploughs sold in the UK are made by Lemken, and with Brits preferring these larger variants, the new Diamant 16 may be set to find favour.
A number of upgrades have been made to the current version, the Diamant 11, which has seen over 4000 models sold, says Lemken’s Peter Baumgärtner. “Previously, you couldn’t adjust the draughtline of a semi-mounted plough, but now Optiline now provides the first and to date only adjustment system for this type of plough and prevents lateral pull during ploughing.”
Awarded a DLG Silver medal, OptiLine compensates lateral pull arising from the plough’s asymmetrical position behind the tractor through a pressure-controlled cylinder which transfers additional torque to the tractor. This adjustment system shifts the tractor/plough traction line towards the centre of the rear axle, resulting in a fuel saving of up to 10%, claims Peter.
“Demands on the operator are also reduced, as there’s no need for counter-steering,” he adds.
It combines with OptiTrack, claimed to boost traction. “This allows higher system pressures, which result in even more weight being shifted from the plough and front tractor axle to the rear tractor axle.”
The dimensions of all main bearings have been enlarged and the on-land version has also been updated, allowing the implement to be used with tractors with an external width of up to 4m.
“Working depth can be set from the tractor seat by adjusting the hydraulic ram on the depth wheel, and the Hydromatic overload protection ensures disruption-free ploughing in stony soil conditions.”
Production of the new Diamant 16 will be start in Jan 2019 and will be available with Dural or DuraMaxx plough bodies up to nine furrows.
Rubin “keeps improving”
The new Rubin 10 disc harrows have a number of design features set to improve mixing efficiency and field throughput, claims Lemken’s Lukas Voss. “It started with the Rubin 9 in 2001, and a number of improvements came with the Rubin 12 in 2014,” he notes.
“The Rubin 10 delivers a wide range of improvements, most striking of which is the new disc arrangement on both implement sides. This brings directional stability, with no lateral pull, reducing fuel consumption. It also allows precise pass alignment, using GPS.”
The discs are arranged to produce symmetrical forces on both implement sides, with the first row angled at 17° and the second at 15°. The three central discs on the Rubin 10 have been offset along the longitudinal axis to ensure that they are able to work collision-free across the full width at a line distance of 12.5cm. This optimises the flow of soil and results in even cultivation across the full working width, says Lukas, with the discs engaging across their full surfaces from a working depth of 7cm up to a maximum of 15cm. An undercut of 20° to vertical maintains penetration.
The discs now have a diameter of 645mm (25mm more) and are DuraMaxx surface-hardened as standard, giving them a 30% greater service life, he adds. “The new legs are 30mm thick – substantially more robust – and each disc now has an overload protection with damped return to minimise frame loads.”
All folding versions feature hydraulic depth adjustment as standard (optional on the 3m mounted). The semi-mounted compact disc harrows are optionally available with depth control wheels, designed to ensure even working depths in variable soils and precise pass alignment along slopes.
“An integrated harrow behind the first row of discs has come in from the Rubin 12, which improves the crumbling effect and helps distribute soil and organic matter. The mounted Rubin 10 is available with a Uni wheel which takes 800-900kg off the back end of the tractor – it’s a purely mechanical wheel system as the implement is raised, so no additional spool valve is required,” Lukas points out.
The new Rubin 10 with working widths of 2.50 to 7m will go into series production from 2019.
Fertiliser hopper boosts Azurit output
Lemken has launched a seed trailer for holding fertiliser when working with the Azurit single-seed drill on large farms. The Solitair 12 SW has a capacity of 5800 litres and can be filled using a telescope loader, big bags or a loading auger.
The precision seed drill is coupled directly to the hopper via a standard three-point coupling. An electric motor drives and controls two seeding shafts, each with four cellular rotors. These dispense fertiliser at the set rate to the Azurit fertiliser coulters, carried by a hydraulically driven fan. An electro-hydraulic part-width section control can be integrated on request.
The Azurit 9 single-seed drill itself was launched five years ago and has been “trickled” into the market, says Lemken’s Lena Büsch. “Its DeltaRow technology puts seed either side of the row line and brings 70% more space in the row, providing improved access to light, air and nutrients for increased yields. It has a forward speed up to 20km/h, although 12-13km/h is usual, covering 60ha/day with an eight-row unit.”
The new seed trailer will be available from autumn 2019, while the Azurit 9 is available with four, six or eight rows and 75 cm distance between rows.
Solitair 23 in front
The new Solitair 23 front tank adds to Lemken’s range of pneumatic seed drills. The hopper passes seeds or fertiliser to the Azurit drill or it can be used for sowing rapeseed and cereals in conjunction with a power harrow and mounted coulter bar. Additional applications include simultaneous fertilisation when working with a seed drill, catch crop cultivation and application of basal dressing in soil cultivation.
“The Solitair 23 has a generous 1900-litre volume tank, while a low profile ensures good visibility,” says Lemken’s Lukas Bonus. “It allows seeds or fertiliser up to 500kg/ha to be metered even over large conveyor distances via four metering units.”
Optional tank scales tell the operator about current tank levels and application rates and a pressure system is optionally available. Seeds and fertiliser are transported to the distributors located on the combination implements via hoses routed underneath or along the side of the tractor.
With a weight of 750kg, the Solitair 23 can be combined with a front tyre furrow press or modular case weights to optimise the balance of the tractor/implement combination.