Nature can disrupt even a perfect fertiliser spread pattern with just a gust of wind. CPM tells the story of the system designed to overcome this weakness.
It’s a level of information that’s never been available before.
By Tom Allen-Stevens
Given the investment made in fertiliser, it’s worth making sure it lands in the right place. This is something that’s always been a high priority for the specialists at Amazone and has driven some key spreader developments.
One significant milestone has been the Argus system, which checks the spread fan and automatically regulates the lateral distribution. But what about wind?
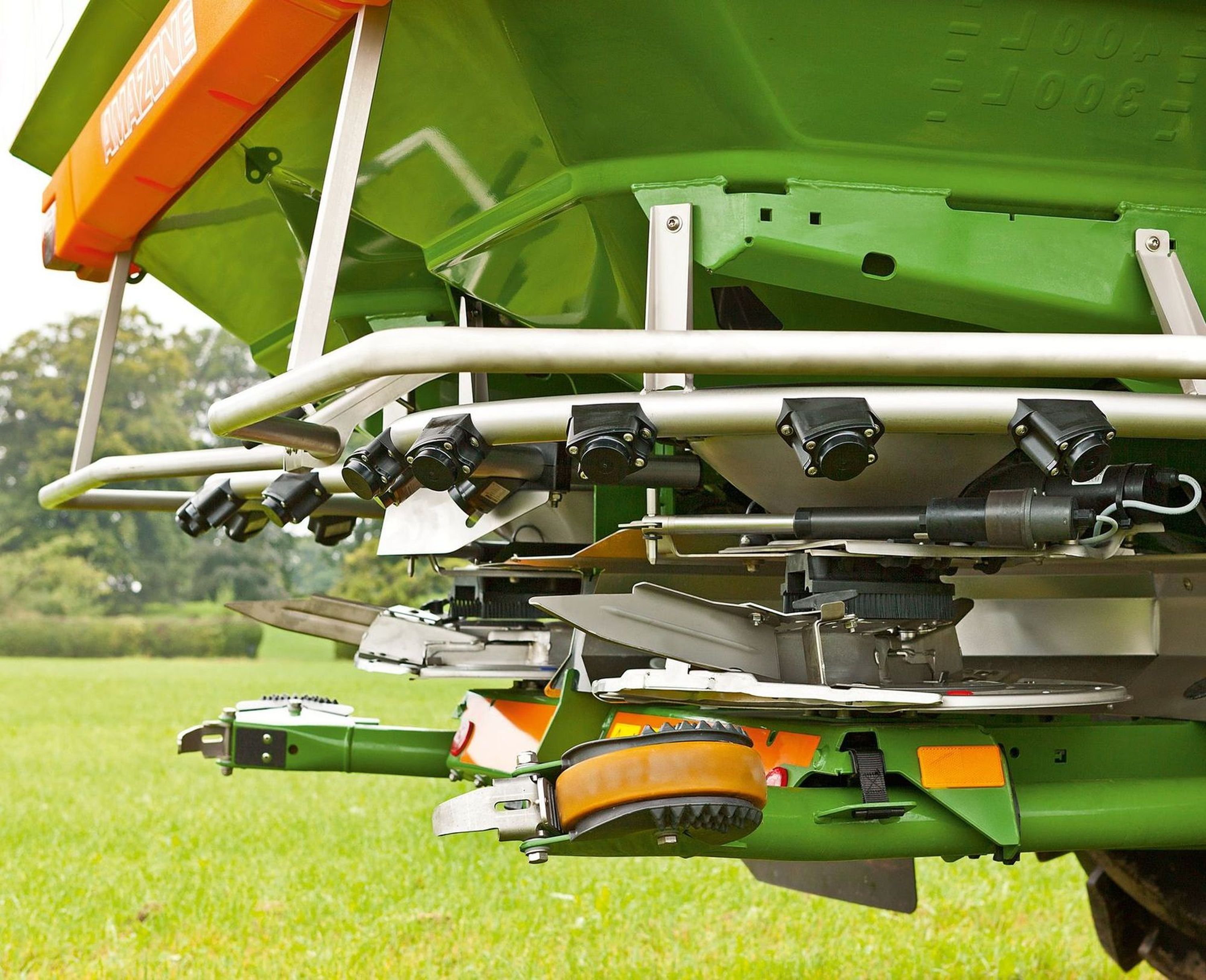
The Argus system checks the spread fan and automatically regulates the lateral distribution.
It’s something that was playing on the mind of Professor Karl Wild, who teaches agricultural system technologies at the University of Applied Sciences, Dresden in Germany. “It was a windy October day around ten years ago, and I took a group of students into the field to demonstrate the effect on fertiliser spread patterns. We did some tray testing and the results were really quite significant,” he recalls.
A keen canoeist, the following weekend he was once again battling against the wind, this time on a lake. “You paddle harder on one side, and steer in the wrong direction to compensate for cross winds. It was then that it struck me – why don’t we do the same with fertiliser spreaders?”
The concept was to have a wind sensor mounted on the tractor, monitoring wind strength and direction, that could inform the spreader how much it needed to adjust the pattern in real time. He presented his ideas to Amazone, with whom the university has a strong research partnership. “We also have some experience with modelling the effect wind gusts have on straw distribution from a combine chopper, so we could help with some of the mathematics,” notes Karl.
But there were significant hurdles to overcome, explains Amazone product manager for fertiliser technology Arnd Kielhorn, who helped develop the concept.
“The first was to really understand how wind influences the spread pattern. When you stand in an open place and feel the wind, you think it’s constant, but it changes direction and strength all the time. So it would be wrong to think that a bout width that’s shifted by a cross-wind would be filled in with the next pass – it’s not because the amount the pattern is shifted changes all the time when it’s windy.”
Then there was the issue of finding the right sensor. “That was really hard,” recalls Arnd. “There must be 70-80 different sensors on the market. But we needed one that was not only reliable and responsive, but would work on the move, was robust to handle travelling across a bumpy field, that wasn’t affected by dust and dirt nor extreme weather conditions.”
It took around two and a half years, including exhaustive testing in the field, but finally the development team found the sensor they needed. Testing the effect of wind on the spread pattern was an equally meticulous process. “We have state-of-the-art testing facilities, but a test hall can’t replicate the wind you get in the field, particularly strong gusts.”
So they analysed the effect of wind on spread patterns through a gruelling set of in-field tests in a whole range of real field conditions in Germany. “We carried out thousands of measurements over trays. It was important to measure the effect not just in exposed areas near the coast, but on hillsides and in valleys.”
By 2014, they had a system that worked. “It was when we entered the last two years of testing with the prototype and you could see how it really made a difference in the field that I realised we had a product that was going to make a substantial difference to the accuracy with which farmers can spread fertiliser,” notes Arnd.
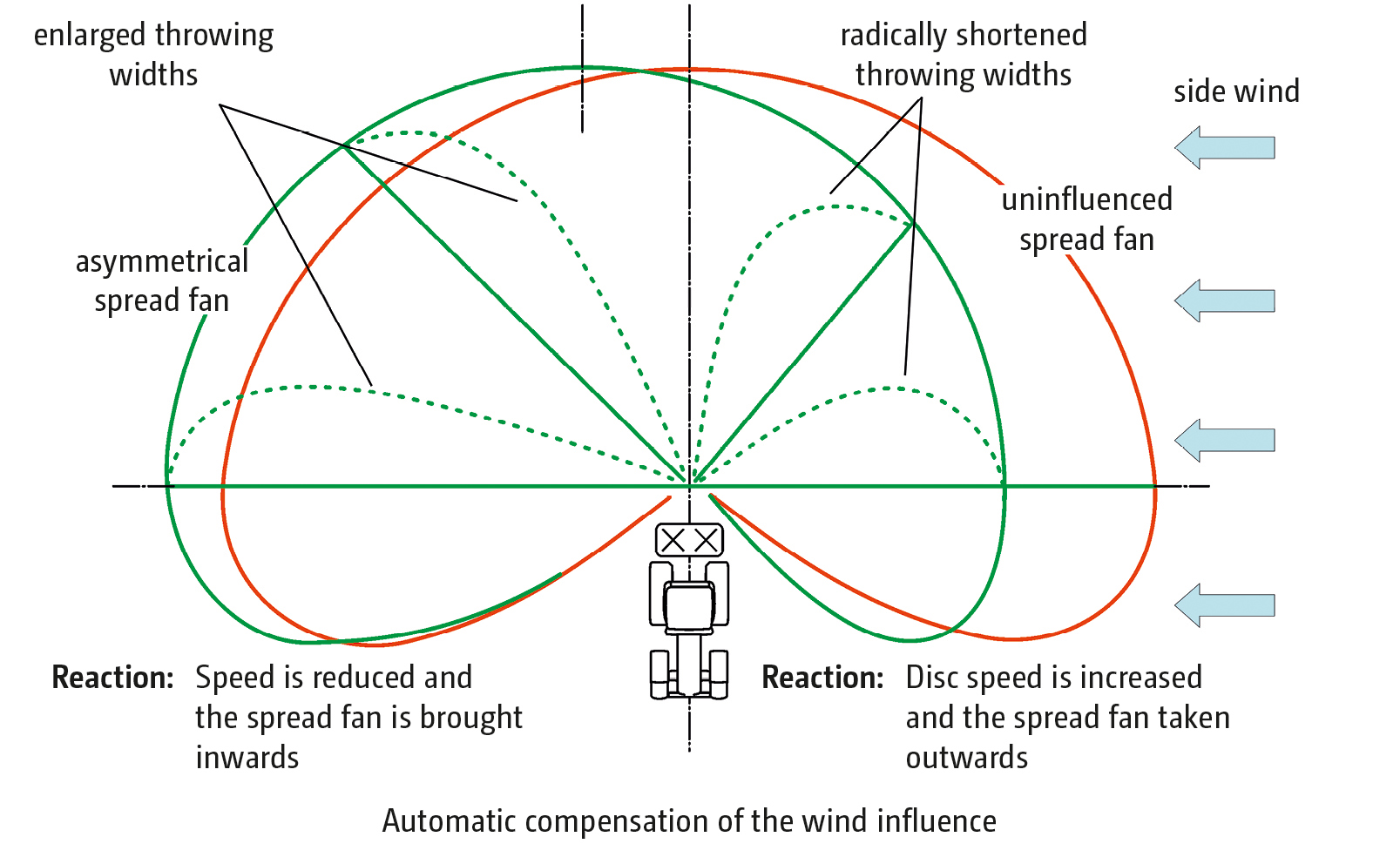
The concept was to monitor wind strength and direction, so as to be able to inform the spreader how much it should adjust the pattern in real time.
Finally, WindControl was ready for commercial roll-out, and it was launched at Agritechnica in 2017. The only bit of extra hardware you need is the wind sensor, that automatically folds in or out when the spreading discs are switched on or off, although the spreader must also be equipped with ArgusTwin.
When in work, the sensor protrudes above the tractor so measurements are not disturbed by turbulence around the tractor. When tucked in, it’s positioned between tractor and spreader and can’t be damaged by low-hanging tree branches during road travel. A protection cap covers the sensor to keep it protected from dirt flying off the tyres.
The clever bit is the software Amazone has developed to run on the AmaTron or other compatible ISOBUS terminal, explains Amazone marketing specialist Stephan Horstmann. “It shows you the wind speed and direction and there’s colour coding to indicate what WindControl is doing. When it’s green, the wind speed is insignificant. When yellow, it’s actively adjusting the spread pattern. When red, it’s reaching its limit, and an audible signal indicates when this is passed, and the operator has to decide whether to stop.”
Stephan points out WindControl is a more cost-effective solution for limiting the effect of wind than a pneumatic spreader. “We’re seeing some growers switch back to a spinning disc. It helps growers meet their environmental commitments, too, reducing the incidents of over-fertilising and spreading over field boundaries.”
The first machine equipped with WindControl came to the UK at LAMMA 2018, and the first few commercial deliveries arrived on farm shortly after, says Amazone brand manager Simon Brown.
“It’s available on ZA-TS mounted and ZG-TS trailed spreaders and these must be fitted with ArgusTwin. WindControl can be retro-fitted to all models built after 2016 – that’s when the ECU was upgraded to cope with the pace of calculations needed.”
For Simon, ArgusTwin was the “crucial development” that put fertiliser properly in its place, in conjunction with SectionControl. “We consider WindControl to be the final piece of the jigsaw in getting fertiliser spatially automated – the precision you now get means that solid fertiliser spreading is much more flexible than liquid. But there are developments we’re working on to make solid spreading even more accurate.”
Growers have been very keen to try out WindControl and the feedback has been good, he reports. “It’s a level of information that’s never been available before, but it makes you think about the effect of wind. The system will reach its limit in less gusty conditions with urea compared with an NPK product, for example, because urea is less dense.”
In practice, though, the main benefit is managing workload – it allows operators larger time windows to spread reliably at the optimum timing. “Here in the UK, we’re spreading to 36m, pushing the system to its limit. When you factor in a forward speed of up to 30km/h, that’s a phenomenal workrate.”
Keeping eyes on the spread pattern
Introduced on the ZA-TS spreader in spring 2016, Argus Twin consists of a series of 14 radar sensors, mounted above both the left and right-hand discs, that monitors the spread fan and readjusts the electric delivery system independently to each other if necessary.
The application rate, as well as any other relevant fertiliser data from the setting chart, can be stored in the ISOBUS terminal. For the Argus system, however, the throw off angle, which is needed to give the optimal lateral distribution pattern, is also taken care of in the setting chart.
On the basis of this value, ArgusTwin constantly checks whether the predetermined direction of throw for the fertiliser is in fact being maintained by the spreading disc. When the actual spreading angle deviates from the “desired” spread pattern due to inconsistencies within the fertiliser, worn spreading discs, travelling on slopes or starting and stopping procedures, the ZA-TS spreader automatically readjusts the delivery system – and that of each side individually.
The system can be started immediately, with no calibration necessary. It operates even when spreading on headlands and when part-width sections are switched off and on. In hilly terrain, Argus even provides a slope compensation of the spread pattern via the automatic readjustment of the delivery position of the fertiliser.
Whilst Argus optimises the lateral distribution, the applied spread rate is taken care of with the on-line weighing system on the ZA-TS. This checks the correct rate is being applied to the discs 200 time a second, with an optional tilt sensor to ensure this is maintained precisely, even in hilly terrain.
WindControl takes the ArgusTwin spread pattern monitoring system to the next level, says Amazone. This uses a high frequency measuring wind sensor, fitted to the machine, which registers both the wind speed and also its direction and transfers this information to the machine’s Electronic Control Unit (ECU).
According to this data, the job computer then calculates, in conjunction with the information from ArgusTwin, any new settings for the delivery system and the spreading disc speed which are then automatically acted upon. For side winds, the disc speed to the windward side is increased and the delivery system advanced whereas, at the same time, the disc speed on the leeward side is reduced and the delivery system retarded.
The spreader achieves this by adjusting the drop point, at which the fertiliser falls on the disc. The closer it falls to the back, the greater the force with which the fertiliser leaves the disc. The angle of throw can also be adjusted by changing the drop point. In this way the influence of wind is automatically compensated for and an optimum lateral distribution is ensured.
Top technology but simple to use
When David Hall came to upgrade the fertiliser spreader for J&D Hall, based near Pickering, N Yorks, he was keen to take advantage of the latest technology.
“When you’re changing one of your main pieces of application kit, you have to go for the machine that’s the most up-to-date. What we have now is very simple to use – you just drive it once round the field so it establishes the headland and then the rest is taken care of – the accuracy is remarkable.”
The all-arable business has 650ha of combinable crops – winter wheat, winter and spring barley and winter oilseed rape – on land that ranges from low-lying ground to “topside”, hilly and undulating fields on the edge of the N Yorks moors. Some of the land is exposed, which can limit the number of days suitable to spread fertiliser.
“It was the local dealer, Wilfred Scruton at Foxholes, who told me about WindControl,” recalls David. “This was last autumn and we had a Kuhn spreader at the time. So we decided to put in an order for a new Amazone ZA-TS 4200.”
This arrived in spring 2018 – one of the first in the UK fitted with WindControl. “It also has ArgusTwin, SectionControl and the on-board weigher is very accurate. You just plug in the type of fertiliser you’re using and the desired rate, and away you go.”
The farm uses a Topcon X35 terminal to control the spreader and there’s a CropSpec crop canopy sensor that allows variable-rate spreading. Both work seamlessly with the Amazone spreader, reports David.
“The Topcon display shows up what WindControl is doing. It’s amazing how it adjusts the pattern when you get a cross-wind. You can’t really see any change in the pattern out the back, but the disc speed can vary by up to 200rpm – it’s very responsive.”
As soon as the spreader starts up, the wind sensor moves automatically into position above the tractor cab, and then folds down at the front of the spreader when the field is finished. This means there’s no worry about knocking it on low-hanging branches between fields, he says.
“We have the confidence to spread in conditions we wouldn’t have risked before. The system tells you if the wind is gusting too strong for WindControl to adapt, so you can be sure you’re always getting a good result. It’s increased the number of days we apply fertiliser, which really helps when planning jobs.
“I’m fairly sure we’re also getting better results. We used to get one or two lodged areas, especially in shortwork, but the bouts don’t appear to overlap anymore. We also previously had lodging on exposed sides of hilly fields, that I think resulted from an uneven spread. It’s been a funny year, so it’s hard to tell for sure, but I’m expecting in a more normal year we’ll get a yield benefit from the greater accuracy of spread we’re now achieving.”
Innovation Insight
CPM would like to thank Amazone for kindly sponsoring this article, and for providing privileged access to staff and material used to help put the article together.