An expanding range of wheeled loaders and telehandlers is now available through John Deere dealers. CPM assesses their features and other recent developments across the Deere range.
A number of features across the range allow the operator to focus on getting the job done efficiently, while staying within regulatory working limits.
Tom Allen-Stevens and James Hacker
Three new machines have been introduced by German wheeled-loader specialist Kramer. Two mid-range telehandler newcomers have a specific fit for arable units, while a new large wheeled loader is set find a place on larger arable farms. But have you even heard of Kramer?
Based in Pfullendorf, near the Swiss border, the company has a 90-year history and made a name for itself as a manufacturer of tractors. It now specialises solely in wheeled loaders, with an expansive range taking in telehandlers as well as fixed-boom and telescopic wheel loaders. All-wheel steer and a number of smart handling features across the ranges are claimed to ensure manoeuvrability and safe but speedy working.
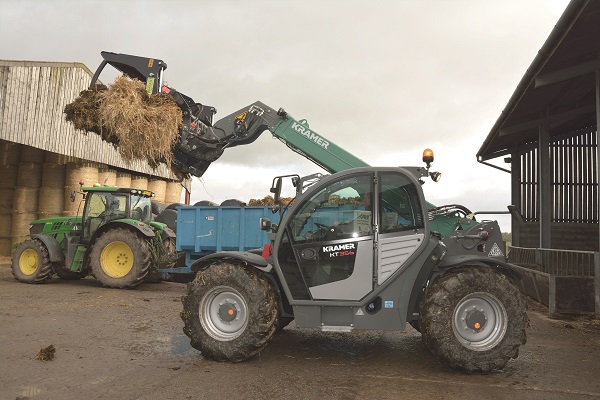
Previously available as Claas Scorpion telehandlers, the full Kramer range is now available under its own brand.
The reason it’s an unknown name is that, until June last year, Kramer was exclusively making the Scorpion loaders for Claas, with just a small number of wheeled loaders and compact telescopic handlers coming into the UK under its own brand. Since then, the whole range has been available, although the telehandlers are essentially a Scorpion under the skin.
There’s now a tie-up with John Deere with Kramer loaders available through around two thirds of the John Deere dealers. The two brands remain distinctly independent – you won’t see Kramer loaders take on the Deere green and yellow livery, and marketing and support are handled separately. But it allows loyal Deere dealers to add a loader manufacturer to their offering without upsetting the global tractor giant, so it’s a complementary relationship, and there’s every indication that its first year has proved a fruitful one.
“Kramer loaders are available through some dealers we already had an existing relationship with,” notes dealer development manager Andrew Dixon. “These will continue, but we’re looking to make new supply arrangements only through John Deere dealers.”
The new arrangement effectively brought eight new telehandlers between 6-9m stacking height onto the UK market in July 2017. The Kramer range has since been developed, with the two additional models, launched in June, bringing the current total to 11. For most, a Level IV-compliant, Deutz TCD four-cylinder 3.6-litre, water-cooled engine puts out 136hp. The top two in the range step up to a 4.1-litre, 156hp variant, while the smallest KT276 has a 75hp Kohler KDI 2504 engine.
Breaking down the model numbers, KT stands for Kramer telehandler, the first two numbers denote maximum payload, and last number the maximum stacking height. So the range starts with the KT276 (2700kg payload, 5730mm stacking height) and tops out with the KT559 (5500kg payload, lifting up to 8750mm).
Kramer’s strapline is “on the safe side”, and it may seem a bit curious to use safety in its marketing. But there are a number of features across the range Andrew claims allow the operator to focus on getting the job done efficiently, while staying within regulatory working limits is handled largely by the machine.
First up is the joystick, with a new operating concept taking in the implementation of the normative new regulations. “It’s an electronically pilot-operated all-in-one joystick that gives you intuitive operation of all functions,” says Andrew. Its sensitivity can be individually adjusted with a jog dial-control element, for example.
A new 7in display puts all relevant vehicle data and settings in front of you, with the option of a reversing camera integrated into this display. There are thoughtful optional additions in the cab, such as a mobile holder and interior rearview mirror, but these are positioned without impairing the line-of-sight in the working area of the loader unit, he says.
The larger models benefit from Kramer’s new ecospeedPRO variable hydrostatic high-speed gearbox. Optional on the KT507 and KT429 and standard with the KT557 and KT559, this brings 370cc capacity for increased tractive force and driving dynamics, says Andrew. “ecospeedPRO drive system allows for a continuous acceleration from 0-40km/h without shifting so there’s no loss of thrust and tractive forces. You also get the known benefits for hydrostatic drives, such as easy reversing, good metering, fine controllability, inching and brake force support.”
Kramer’s Smart Driving intelligent engine speed reduction is integrated as standard in the ecospeed and ecospeedPRO drive systems. This optimally adjusts the engine speed to the driving requirements at a constant speed, he explains. “When reaching maximum speed, noise level is reduced, fuel consumption lowered and there’s reduced load on the individual components. With ecospeedPRO, it’s possible to reduce the engine speed to 1550 rpm at maximum travel speed.”
A neat feature across the Kramer range is the Smart Handling system. “This continuously monitors the load state and ensures that the vehicle is in a safe position and cannot tip over forward when stationary.”
There are three functional modes:
- Stacking – while raising and lowering, the telescopic arm moves in a vertical line and the loader unit automatically telescopes in and out, without shifting the load centre.
- Bucket – when lowering, the loader unit is automatically retracted so it never enters the overload range.
- Manual – no automatic movements of the loader unit are carried out, but if the overload limit is reached, the loader unit stops.
“There’s also automatic bucket return, that will bring the bucket position back to a pre-set point after tipping, and a bucket-shake function on the joystick,” adds Andrew.
All-wheel steer gives most models a turning circle of just 3.8m, with the top-end KT559 turning within 4.4m and the compact KT276 less than 3.7m. All telehandlers can be put into crab steer or front-wheel only steer when needed.
The new KT407 increases the payload capacity of the compact telehandlers, explains Andrew. “A bigger counterweight puts an extra 230kg on the back. Otherwise it’s identical to the KT357.”
The KT429 brings much of the capability of the range-topping KT559 into a lighter and less expensive machine. “It’s aimed primarily at large arable units and contractors shifting a lot of straw. It has the same strength, durability and hydraulic speed of the larger model, but it’s 1t lighter with the smaller Deutz engine.”
Launched at Agritechnica, the KL60.8 is Kramer’s largest agricultural wheeled loader, with a total weight over 9t and a bucket tipping load of 6100kg. For those who need a little extra reach, the KL60.8L adds 400mm, bringing the stacking height over 4m.
The engine is the same Deutz four-cylinder 136hp version as the telehandlers, with the option to upgrade to the larger 4.1-litre version. There’s have the same hydrostatic drive with ecospeedPRO and Smart Driving features as the telehandlers. Hydraulic performance can be stepped up from 150 l/min to an optional 180 l/min.
Cab comforts are largely the same with similar controls, display and emphasis on visibility, and there’s air-conditioning. Automatic bucket return is also standard.
All-wheel steer, with crab and front-wheel modes available as standard on the premium 8-series models, have advantages over pivot-steer machines, points out Kramer’s Wayne Freke.
“The payload is always in line with the rest of the machine, and the centre of gravity doesn’t shift. Also there’s a tighter circle, with both front and back wheels having a steering lock of 40°.”
The hydraulic quickhitch facility has a “sturdy” four-point locking system with a 61.5mm wide support as well as a 50mm thick lock pin, with a variety of attachments making the wheel loader a flexible application in agriculture, he adds.
Smaller wheeled loaders in the Kramer range are available with a telescopic loading system. The KL55.8T is due to bring the same capability to the flagship size class in spring 2019, notes Wayne.
New forage harvester promises 10% productivity boost
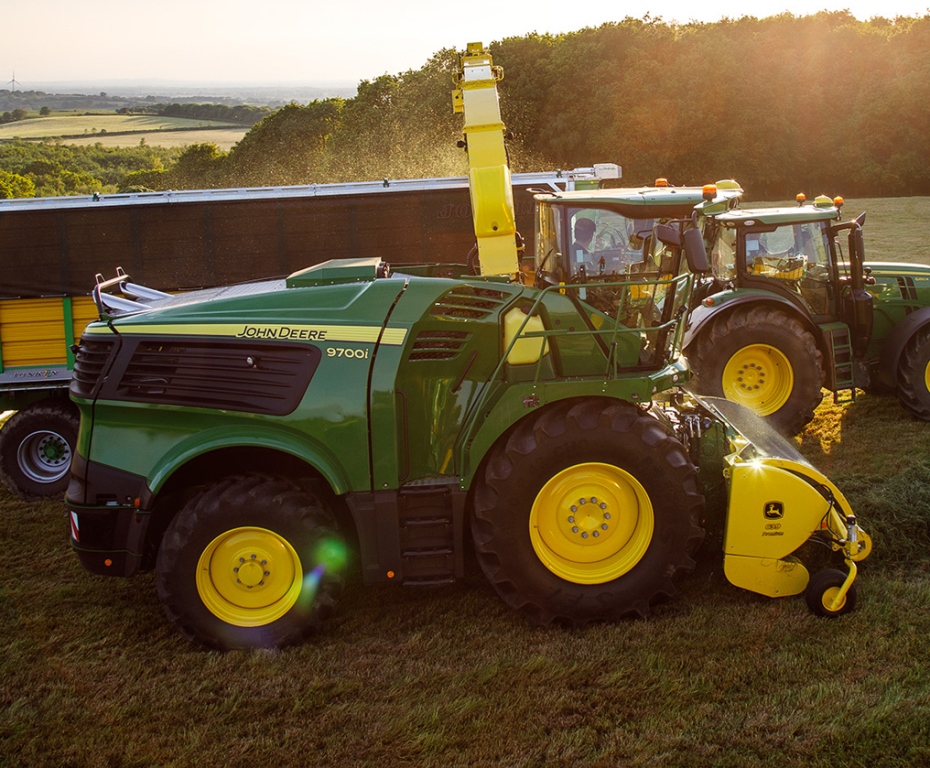
The new forage harvesters can provide
outstanding torque capacity and can easily cope
with peak loads even below an engine speed of
1400rpm.
Following on from the success of its 8000 series, John Deere has announced four brand new self-propelled forage harvester models, offering growers a 10% productivity boost with a 10% reduction in fuel use, claims the manufacturer.
The three largest models – the 9700, the 9800 and the 9900 – range from 770hp to 970hp and are fitted with a 24.2-litre V12 Liebherr engine. Optimised to work efficiently at lower engine speeds, these foragers can still provide outstanding torque capacity and can easily cope with peak loads even below 1400rpm, says Deere’s Mike Baker.
The V12 Liebherr operates in tandem with several efficiency-oriented developments – most notably the optimisation of component speeds at low engine rpm – to form the basis of John Deere’s new HarvestMotion concept, he explains. “This significantly increases throughput and enables industry-leading fuel economy.”
The fuel savings, along with productivity gains, have been verified both internally and externally through numerous field tests, he says. The large crop channel width of 850mm is tailored to handle the throughput of these machines. Because of the higher engine horsepower, there’s a reinforced drivetrain and improved mainframe. The speed of both the DuraDrum cutterhead and feed rollers has been increased to handle higher crop throughput but retain the length of cut.
Deere has also put great emphasis on this new range’s maize silage capabilities. The 9000 series’ consistent 10% increase in kernel processing scores is coupled with a new extension to its range of kernel processors: the XStream KP model. Developed with the experienced leader in kernel processing technology Scherer, this model is matched to the 9000 series’ high-performance engines. “The large roll diameter of 250mm and a 50% roll speed differential means processing intensity is increased 10% at all cutting lengths,” claims Mike.
The Premium KP unit offers customers kernel processor roll with a standard sawtooth design. The XStream KP unit comes with either this standard sawtooth design or the new XCut design which features a spiral cut groove across the roll surface. Both of these designs are available with Dura Line heavy-duty coating to increase durability.
The new XStream KP model also contributes to the 9000 series’ increased efficiency, adds Mike. “A new built-in temperature monitoring system informs the operator of the KP bearing temperature allowing for the prevention of unnecessary machine downtime.”
The 9000 series forage harvesters are compatible with Deere’s complete range of AMS precision farming systems. Newly added to the AMS systems’ list of features and functionalities is the HarvestLab 3000 NIR (Near Infrared) Sensor. Operators can view and document real-time measurements of constituents like crop yield, moisture, protein, starch and fibre. This data is available to view as totals or via site-specific maps.
John Deere’s claims of improved productivity and fuel economy are supported by the 9800 model’s DLG certification. Having undergone demanding DLG field tests in high-yielding maize fields in northern Italy and Germany, the 9800 model demonstrated significant increases in performance and efficiency.
Field operations at your fingertips
John Deere has introduced the all-new MyOperationsCentre app. It brings remote management of your field operations and equipment to your smartphone or tablet. The app allows you to monitor completed field activities of any JDLink-enabled machine that occurred over the past 24 hours, including drilling, spraying, harvest and cultivations.
The app makes it particularly convenient to view and alter combine settings as these can now be accessed remotely, and sent to the in-cab display where they can be confirmed by the operator.
The MyOperationsCentre app is available to download now, free of charge to all JDLink users.
6R series tractors get CommandPRO
John Deere’s CommandPRO joystick is now available for all small and mid-range 6R series tractors. These models also feature the new CommandCentre 4200 display, which provides all six ISOBUS functions certified by AEF (Agricultural Industry Electronics Foundation).
CommandPRO allows the tractor to be controlled from top speed to zero with a simple push or pull of the joystick, and lower speeds from 0-2km/h can be achieved with the creeper control function. 11 programmable buttons are also available for the hitch, pto, SCVs, AutoTrac controls etc.
CommandPRO will be available on the wider 6R Series range in combination with John Deere’s AutoPowr transmission, and both features are standard on the 6R Ultimate Edition models. CommandPRO can be ordered in combination with either the 4600 or the new 4200 CommandCentre display.
The 4200 replaces the 7in 4100 unit and features a larger 8.4in screen. This terminal controls AutoTrac, Section Control, data documentation and other applications. It’s also ready for all AEF certified ISObus functions such as joystick control and data transfer between tractor and implements.