A larger combine can be preferred to a new drying system, the extra output making it more feasible to wait for ideal cutting days and sub-15% moisture, however, coping with incoming grain can be challenging. CPM learns how a pair of compact-design telehandlers helps to keep ahead of the trailers.
“It just makes logistics so much easier, and the investment soon pays off.”
By Martin Rickatson
What’s a cereal farm’s most important machine at harvest time? Without a combine, of course, a crop can’t be cut. But whatever its capacity, it’s fairly impotent once its tank is full without a decent trailer fleet supporting it.
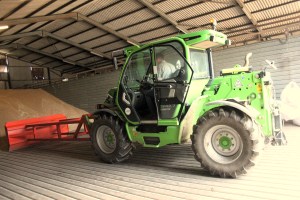
Will James relies on a pair of Merlo TF42.7 telehandlers to keep incoming trailer loads pushed up at harvest.
Arguably one of the most critical tools in many of today’s harvest set-ups is the telehandler. Without one at the store keeping loads pushed up and freeing space, trailers – and therefore the combine – can stand around waiting to be emptied. This can lead to expensive unproductive time which puts the standing crop at risk of the next break in the weather.
Unless in the fortunate position of having a large, modern grain store designed for today’s machinery, many farms also find themselves trying to handle the high hourly output from modern combines using storage built when harvesters were less productive and trailers had less capacity.
It’s a scenario familiar to Lincolnshire farmer Will James, and something he keeps on top of not through the investment which upgrading or changing his storage facilities would require, but via the lower expenditure necessary to run a pair of compact, but high-output, telehandlers.
The blow-away sand to heavy clay land he farms for himself and others around Winterton, near the River Humber, grows crops including sugar beet, vining peas, carrots and potatoes. Each year around 1,200ha of the 1,400ha total is combinable, comprising winter wheat, barley, rye, oilseed rape and beans, plus spring barley and peas.
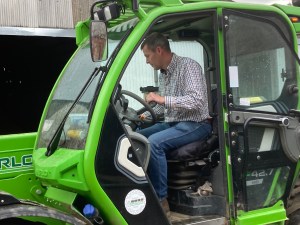
The strength of the tubular steel design structure was something that initially attracted Will to Merlo telehandlers.
It all goes through one machine – a 12m-cut Massey Ferguson Ideal 9T. Bought in partnership with his neighbour James Brown, it’s their second such combine after a successful four years with their first which was purchased in 2019.
“The combine’s capable of covering a lot of ground, but that means we require a good set-up to support it,” says Will. “We have two main farms about nine miles apart each with their own grain stores, and also look after a neighbouring farm on stubble-to-stubble contracts as well as what’s farmed by James.”
Will says most of the land surrounds the farm units so when they’re cutting, the travel distances to store are relatively short. “The grain comes in fairly quickly with a combine of this size. When we’re on more distant runs, we try to keep up the same pace by using more tractors and trailers because I don’t want the combine kept waiting,” he explains.
But on all of the units, the grain stores aren’t the newest or the largest. “We’re fairly tight for space – the buildings were constructed in the 1970s and have been adapted since then. They could do with being a few metres taller, but while we’ve considered replacing them, the size of the necessary investment is difficult to justify,” says Will.
Some of the storage is wooden-floored with recessed ventilation, while elsewhere, concrete floors are in place with pedestals used to circulate air into the stored crop.
“We used to have a pit and conveyor system with the grain dropped into store over laterals, but it couldn’t cope with modern combines, being capable of inputs of 30t/hr at best. This was replaced with the ventilated wooden floor which made life much easier,” he says.
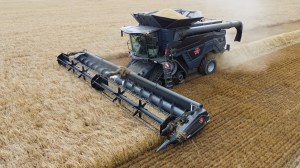
The farm’s combine is a 12m-cut MF Ideal 9T, and with most land fairly close to the two main bases, trailers can come in at a high rate.
“Now, across all of our storage, we simply tip and push up with one person in the store on a telehandler at all times during harvest.”
With the tip-and-go method, the harvest bottleneck potentially lies with the ability to push up incoming grain to full storage height before the next trailer arrives, notes Will. With his sheds considerably older than his machinery, his preference is for a telehandler that despite its capacity, has a compact design.
He says it’s something he’s consistently found from Merlo designs and is why he’s stayed with the marque for well over 20 years. “We’d been Sanderson users for many years, but when the firm folded in the mid-1990s, although we looked at all options, we decided to move to Merlo when the dealer who’d sold us our Sandersons became their agent.
“There were a number of design ideas that appealed, particularly regarding our requirement for a high-capacity machine that’s still sufficiently compact and manoeuvrable, to be operated easily around our relatively compact yards and grain stores.”
According to Will, Merlo hits the spot. “Although larger agricultural-spec machines are now available, offering capacities of 6t+, I’ve found a telehandler with a capacity of around 4t is more than adequate. It seems there’s a trade-off of capacity versus machine dimensions when you go much above this, regardless of the manufacturer,” he says.
“Merlo was also one of the first firms to design a machine with the boom set low when lowered, and I still think the machines offer some of the best all-round vision, which is also important in relatively compact sheds and yards.”
Will says in addition, when they first considered Merlo, there weren’t many other telehandler firms using a hydrostatic transmission and it was something he really liked when he tried it. “Having a true inching pedal is nice as it means you’re not standing on the brakes all the time when having to make small movements. We subsequently bought our first Merlo in 1999.”
With a nine-mile journey between the two main bases, and each having its own grain store, Will has since adopted a policy of having a handler on each farm to avoid excessive road mileage, fuel use and travel downtime.
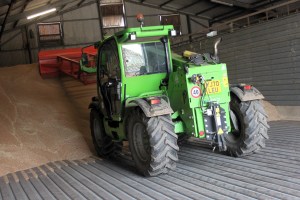
At 4.73m long, 2.31m wide and with a turning circle of just under 4m, Will rates the dimensions and manoeuvrability of the TF42.7.
Both are Turbofarmer TF42.7 models, with a lift capacity of 4.2t and maximum lift height of 7.0m. A Deutz 143hp four-cylinder engine provides the power for a 150 l/min hydraulic system operating at 200 bar pressure.
“There are bigger machines now available but this size copes with what we ask of it. More capacity would mean bigger dimensions which is something I want to avoid, especially as the store on our other farm is even more compact than the one here at home,” says Will.
“Even in our larger stores it’s necessary to negotiate the stanchions within them, so manoeuvrability and compactness are again important.”
Will explains they’ve run a machine at each farm since the days of the Sandersons, primarily because they were slow on the road and therefore it was more cost-effective compared with travelling between the sites. He says covering nine miles at 15mph wasn’t much fun.
“It just makes logistics so much easier, and the investment soon pays off. If we went to one machine we’d probably also be reliant on one pusher, which is a pain to move. With two machines, we have a pusher at each farm, both locally-fabricated units that give us plenty of reach when combined with the telescopic boom,” he says.
“We aren’t pushing too high or too far, so these 7m machines can easily manage – three pushes pretty much deals with a load from an 18t trailer. We use the same combination for pushing up beet on pads through the autumn and winter.”
After being happy with the first Merlo, with its 25mph top speed an improvement among other advances, Will subsequently bought another. The first machine was moved to the other farm to replace the remaining Sanderson 726 Solo.
“We don’t follow a rigid replacement policy, but as a general rule, each machine probably does five years before being replaced.
“At the outlying farm we currently run a 61-plate TF42.7 while on the home unit we use a newer 70 plate model – a slightly upgraded version with a little more horsepower plus optional wider tyres to provide more road comfort,” he says.
“Beyond that, we haven’t tended to specify other options when we’ve ordered a new machine, finding Merlos are well-specified for most of the features I’d expect.”
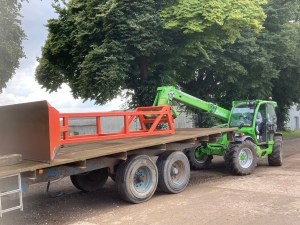
Each of the two farm bases has its own handler to save road travel downtime, and each has its own locally-fabricated grain pusher.
There’s been notable franchise movement during recent years as changes occur among manufacturers, importers and dealers, particularly because of the influence of dominant tractor franchises. This meant back in 2016, Will faced a decision over whether to commit to his primary dealer or his favoured manufacturer when the former switched to another handler franchise.
“The Merlo franchise moved from the dealership we use for our tractors and combine to an independent dealer dedicated to telehandlers and the Merlo brand. I only saw that as a positive and was sufficiently happy with what I’d experienced so that when Agriscope, the new dealer, took over the franchise for the area, I switched to using their services,” he says.
“We’ve rarely required anything from them except routine servicing with no reliability or breakdown issues to speak of. To be fair, we’re not high hour users. We run two machines and don’t have any livestock, so although our machines do a lot of work at certain times of the year, they probably aren’t under the demands that they could be. That said, they perform a very important role when we’re combining in keeping the whole harvest chain operating.”
Will admits he occasionally looks at what else is available. “We tried at least one big-brand alternative before committing to our most recent machine replacement, but the price quoted was higher and there was nothing that especially compelled me to swap.
“The farm where we share some machinery runs one of the same make, so we use it a bit. However, I keep returning to the point that Merlo always seems to design a machine which offers the blend of compactness and capacity that we require,” he confirms.
Will says with some of the alternatives, the comparable models seem to be much larger in dimension for the same lift capacity and he believes that would slow down the speed of work around the store at harvest. For him, a smaller machine is much more nimble, and the size of the machine for the amount it can lift is a key attribute.
With the farm using liquid nitrogen through its Fendt Rogator RG655 self-propelled sprayer, when it comes to handling fertiliser, the Merlos are only required for loading bagged phosphate and potash products. Loading lorries out of store is their other key task, along with shifting seed and loading drills in autumn.
“We have one farm where the grain storage is bin-based and we load directly from them, but for everything else we use the Merlos with 2.5t-capacity buckets. Good visibility and compact dimensions again help, meaning while they may not have the biggest capacity available, they can load a lorry pretty quickly,” he says.
“We sell most of our straw for power station and mushroom compost use, trading used mushroom compost back for organic matter replacement so there’s no bale handling. All the bale work is done with chasers by the contract baling crew,” explains Will.
“Not chopping helps to keep combine fuel use down and output up, but with more than 1011ha to put through one machine, the telehandlers still have an important part to play in ensuring we keep the trailers moving, which in turn means the combine isn’t kept waiting. That’s an essential harvest role.”
This article was taken from the latest issue of CPM. Read the article in full here.
For more articles like this, subscribe here.
Sign up for Crop Production Magazine’s FREE e-newsletter here.