Horsch has unveiled new weed control implements to complement its sprayer line, aiming to offer growers a full suite of integrated weed management kit. CPM travels to Germany to preview the range.
I can see a time coming when countries may lose not only more of the selective herbicide products we have, but also quite probably glyphosate.
By Martin Rickatson
The tractor coupled to the front of Horsch’s new Cura ST weed harrow isn’t hanging around. Zipping along at a probable 15km/h, the onlookers watching the machine appear more nervous than the operator as he tears up and down at speed through well-established young plants.
Various members of the audience poke around between the crop rows behind the tractor and weeder combination, looking for evidence of crop damage and inter-row weed removal. There’s very little of the former, and fair evidence of the latter.
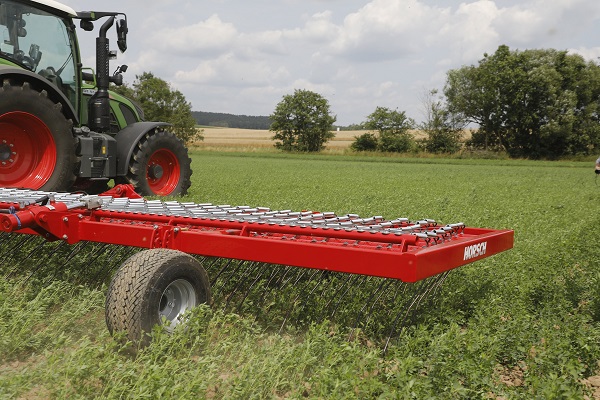
The Cura ST weed harrow features six rows of steel tines, which can be hydraulically angled to provide greater pressure to dislodge tougher-rooted weeds
Marking a departure for Horsch into new territory outside its usual specialisms of tillage, seeding and spraying equipment, this is just one machine in a line of new weed and stubble management products shown at the firm’s recent demo days in Germany, and set to be launched at Nov’s Agritechnica. The company has announced a series of new implements designed to meet head on the growing pressures on crop protection products – herbicides in particular – as they come under scrutiny from environmental concerns, the costs of re-registration and the development of resistance.
“Whether inside or outside the EU, I can see a time coming when countries may lose not only more of the selective herbicide products we have, but also quite probably glyphosate, which will potentially lead to some significant changes in the way farmers establish and manage their crops,” says the company’s Michael Horsch.
“New spraying technology has a role to play in helping to more precisely target the products that remain, and we are committed to sprayer manufacturing of both trailed and self-propelled types, having recently completed a significant expansion of our sprayer factory. The sprayer sector continues to be a particular growth area for us, and our target is to build 800 trailed and self-propelled sprayers in 2019, a figure that’s than 100% up on our 2017 total.
“But we see no downsides, and potentially a number of advantages, in encouraging farmers to look at supplementary methods of weed control, including mechanical. By blending the use of such tools, already proven in organic crop production, with chemical control, you have the benefits of both – what could be described as a ‘hybrid’ system of organic and conventional husbandry.”
To this end, a growing proportion of the recent development work around cultivation and weed control that the firm has been conducting on its own factory test farm and elsewhere revolves around mechanical solutions to weed problems, whether for conventionally-drilled, band-sown or row-type crops. They range from post-crop destruction of stubbles, weeds and regrowth to inter-row cultivators designed for use in different crop types and establishment systems.
Horsch suggests mechanical weed management can begin with stubble hygiene when dealing with the previous crop, to destroy both regrowth and established weeds, and this is where the firm has positioned its new Cultro TC stubble processor. It’s aimed at the rising amount of maize grown across the UK for anaerobic digestion, which leave behind tough stubbles and potentially mats of weeds between rows. Horsch says the new tool is particularly suited to working in such conditions, as well as post-oilseed rape, for many of the same reasons.
With many cereal growers choosing to leave longer stubbles to raise combine outputs and provide some ground cover between harvest and commencement of the next crop’s establishment, it potentially also has a role here, suggests Horsch. And, says the firm, those committed to growing cover crops are also a likely target market, whether seeking to process fresh or sprayed-off vegetation at the end of its useful life.
The implement is available in two very different versions and working widths. Consisting of six independent knife sections across each row of the roller, the 3m model can be mounted either on the front or rear linkage of the tractor. The compact diameter of the roller enables it to achieve a high number of revolutions in relation to the forward speed of the tractor, and therefore a high number of cuts per revolution. The six knives on each section are each arranged at an angle, said to maximise the implement’s slicing and pulverising action when working at speed.
At the other end of the scale, Horsch has also developed a 12m trailed version of the Cultro TC, designed for working at up to 20km/h, with a 200hp tractor reckoned to be sufficient to achieve that sort of speed on flat land. The trailed model is built around a chassis design which, when in operation and under the draft load of the tractor, transfers weight onto the stubble-processing roller, to enhance the level vegetation-crushing capability and lead to faster natural breakdown of material, says Horsch.
The key working elements of the 12m implement comprise the individual roller segments from the 3m machine, and these are suspended independently of each other to enable field contours to be followed on uneven land. Ahead of them, it’s possible to specify the Horsch Crossbar, to carry out light surface tillage and potentially prepare stale or crop seedbeds.
For those looking to conserve moisture in the resulting mix of surface soil and chopped plant material, at the rear there are a number of different packer options, while for customers seeking to distribute material more finely, grass-type harrows can be specified.
Also designed for control of old-crop stubbles, ranging from old cover crops through to thick-stemmed and deep-rooted maize, Horsch has added a shallow-working stubble cultivator to its line.
The new implement, the Finer LT, is available in models covering working widths from 6-12m. Spaced at 15cm, tines are spread across four angle-adjustable rows for effective trash flow, which is also aided by a 55cm under-frame clearance. The final element of the implement is a two-row following harrow.
Moving on to in-crop weed control, Horsch has developed a number of new tools for mechanical removal, whether for use in crops sown in conventional, band-sown or precision-drilled rows. Chief among them is the aforementioned Cura ST, a three-point linkage-mounted tine weeder available in working widths from 6-15m.
The Cura features six rows of steel tines, which can be hydraulically angled to provide greater pressure to dislodge tougher-rooted weeds, with a range from 0.5kg to 5.0kg. The tines are designed in such a way that they apply a consistent force throughout their deflection path to maintain their force and do a full weed removal job. Individually secured, side deflection is prevented to ensure the units maintain a precise path to minimise the risk crop damage.
Meanwhile, turning to more commonly mechanically-weeded crops in both conventional and organic systems, such as maize, beet crops and other precision-drilled rowcrop types sown on row crop spacings, Horsch has also introduced its first toolbar, the Transformer VF, designed to accommodate rowcrop cultivation tine arrangements and create an inter-row hoe. A wide range of different tools/tines is available for the implement, and options include covering discs for the hoeing tools to protect young crops from damage.
Key to the implement’s versatility is the variable frame (VF) design that allows the tool clamps to be infinitely adjusted across the frame to accommodate the particular row widths in question, with a minimum of 25cm and a maximum of 90cm. Horsch offers a range of tools for fitting to the parallelogram-type mounting arrangement. Working depth is regulated by a simple lever-altered arrangement on the cultivator frame, and for tackling tough ground or large, deep-rooted weeds the units can be hydraulically pressured.
Arguably the most interesting aspect of the new machine is the adoption of a section control system to minimise the possibility of twice-worked land in triangular field areas. Horsch says the technology to do this is broadly similar to that used in other areas of farm equipment, and the principle is exactly the same. As the implement meets triangular work in field corners by the headland, for example, units that are meeting already-worked ground are progressively raised individually and automatically according to the GPS or similar signal being used by the tractor’s guidance system.
This, says Horsch, further ensures that above and below-ground crop damage risk is minimised, and tool wear is also kept to a minimum, while also making sure moved surface soil is not over-stimulated, potentially resulting in a further weed flush. In its basic format, guidance can be by tractor steering and operator judgement alone, but there is the possibility to equip the Transformer VF with an ISOBUS-operated camera system to detect the plant rows and ensure the implement’s tine attachments are kept between them.
There is a four-model range of Transformer VF toolbars, with 6m and 8m implements that fold in three sections, and 9m and 12m versions that are constructed with five, folding in a similar way. All models come within a width of 3m and a height of 4m for transport.
One of the key design aspects is that the wings on all versions lift automatically when the implement is raised at headlands. Horsch claims this increases possible workrates and eases operator strain, as well as the likelihood of incurred damage to either the implement or field objects around it. The feature enables fast end-of-row turns, says the firm, to get quickly back into work without fear of a misjudgement causing an outer edge to catch on a hedge or fence. The implement can work relatively late in spring-sown crops, courtesy of a 660mm clearance beneath the frame.
Sprayer news set for Agritechnica
Formerly Horsch had offered both front and mid-cabbed sprayer options, although the latter were not sold in any significant quantity in the UK, For its latest self-propelled sprayer development the firm has switched fully over to a front cab configuration, having based its decision on weight distribution characteristics as well as demand.
There are two models in the new Horsch Leeb self-propelled range. The Leeb 8.300 PT is an 8000-litre capacity model with stainless steel tank, while the Leeb 6.300 PT has a 6000-litre polyethylene unit, the latter representing the firm’s first foray into the 5-6000-litre self-propelled sector that is the key UK market. Tank specification includes rapid filling via a 1000 l/min stainless steel rotary pump, plus the CCS Pro continuous inside cleaning system and automatic washing programme.
At the rear, it’s steel booms only, as is the Horsch way, with the firm pointing to the strength, cost and ease of repair advantages of steel. Boom widths up to 42m can be specified, with up to with 42 individual sections. Horsch BoomControl suspension is standard, and this can be upgraded to Pro Plus specification to allow each boom section to independently follow ground contours.
FPT Industrial provides the power for both models, courtesy of a 6.7-litre 6cyl engine producing a maximum 310hp and meeting Stage V emissions regulations without exhaust gas recirculation. The powerplant drives a hydrostatic transmission said to provide 30% more torque than its predecessor. The Horsch ComfortDrive chassis concept incorporates new hydro-pneumatic individual wheel suspension, and the machines can now take tyres up to 2.15m diameter.
Key selling points of the old range of PT mid-cabbed machines that made them popular to mainland Europe buyers growing rowcrops was their ground clearance and adjustable track width. On its new models, Horsch uses a design which offers clearance of up to 2.0m, and an adjustable track width of 2.25-3.00m. The operator gets a new Claas-sourced cab protected by Category 4 filtration, with control features including a new ErgoControl armrest.
Horsch has also revealed that, at Agritechnica in Nov, it will be entering the market for a ‘five-figure capacity’ trailed sprayer, with the unveiling of a 12,000-litre tandem-axle unit. Booms will be the same steel units of up to 42m as found on the new Leeb 6.300 and 8.300 PT self-propelled machines. The firm’s current trailed flagship Leeb trailed model holds 8000 litres.