While the rain didn’t let up from dawn until dusk, the first day of January’s LAMMA machinery show was busy throughout, thanks perhaps to the now-established indoor venue and the fact few arable farmers could do much else except workshop and office chores. CPM was there.
By Martin Rickatson
The strong attendance at this year’s LAMMA suggested there was some serious window-shopping happening. Will they be spending in 2023, though? Those launching new machinery were certainly hoping so…
With largely good harvest results and decent commodity prices having softened some of the pain of high input costs over the past season, many arable farmers could be forgiven for considering opening the chequebook and renewing worn-out equipment or investing in the kit needed to adopt new systems such as minimum tillage or direct drilling.
How much of that will translate into expenditure, though, remains to be seen, particularly as farm business advisers were sounding a note of caution to those considering investing recently-gleaned profits in machinery and equipment. At its LAMMA show press briefing, consultants Andersons urged farmers to think about more than minimising their tax liabilities when considering machinery investment.
“Machinery and equipment purchase decisions are often driven by the desire to reduce tax liabilities,” noted the firm’s Jamie Mayhew.
“Decision-making based on this as the priority can often result in production costs increasing rather than decreasing, and as such investments are often built into the business for the long-term, the effects can be long-lasting.
“Cash surpluses may be better used to reduce borrowings, especially with further interest rate increases looking likely. But one of the under-utilised options, that many farms are still not considering, is the value of pooling machinery, and machinery investment capabilities, via collaborative ventures,” he highlights.
“The savings from working together, from an informal arrangement to a full joint-venture company, can be massive, and may provide the justification for more efficient equipment investment.”
Some of the farm equipment industry’s larger names, including John Deere, Claas, New Holland, JCB, Kuhn, Amazone, Kverneland, Horsch and Lemken, continue to spend their marketing money elsewhere, so LAMMA visitors were unable to compare a full array of tractors, combines, handlers, drills and sprayers. But there were plenty of other firms in attendance, particularly among the British drill and sprayer makers, and some key international suppliers.
Combine upgrades
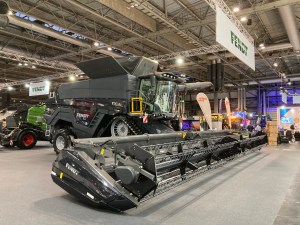
Fendt Ideal combines for 2023 benefit from upgrades in areas including unloading augers, tracks and automated turning.
At the top of its combine range, Fendt has made a number of revisions to its Ideal line-up for harvest 2023. Among them is the brand’s VariotronicTI Turn Assistant, which automates the headland turning process. In bed mode, the combine works the field in small sections, and keeps the unloading auger always on the cut side to ease unloading. For smaller fields there’s a ‘keyhole’ turn mode, while if several machines are working on one area it’s possible to programme U-turns to match the workflow and ensure the combines don’t end up on the same way line. By eliminating any likelihood of imprecise turns, the system is reckoned to save time, reduce driver fatigue, eliminate unnecessary manoeuvring, and minimise trafficking and fuel consumption.
Meanwhile, new 7.0m, 8.4m and 9.9m unloading augers replace the existing 7.6m, 9.15m and 10.6m units, and provide respective unloading heights of 4.55m, 4.95m and 5.35m. Depending on the header width and auger length, this enables better tractor/trailer placement when unloading, says Fendt. It means trailers can drive above or next to the swath and high trailers are loaded precisely and quickly even in uneven terrain.
Further upgrades include a heavy-duty drive option for Ideal 8T, 9T and 10T tracked models, featuring a hydraulic pump and a hydraulic motor that each have greater capacity for hilly ground and for high-speed roadwork, especially when towing a header, says Fendt. Operators also benefit from the upgrades, with improved noise insulation, new storage options and a new cooling box.
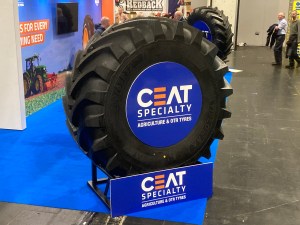
Available in 650/75 R32 or 620/75 R26 sizes, characteristics of CEAT Specialty’s Yieldmax combine tyres include a high lug angle around the centreline for maximum side stability.
New track and tyre combinations include 76cm (30in) tracks or 800/70 R38 front tyres in combination with 520/85 R30 rear tyres, keeping machine width to 3.49m. The combination is claimed to provide more footprint and hence reduce ground pressure, while also increasing manoeuvrability through a greater steering angle.
Elsewhere in combines, tyre manufacturer CEAT Specialty highlighted its harvester tyre technology in the form of its Yieldmax combine tyre, shown in conjunction with UK distributor Nordic Tyres. Aimed at the OEM and replacement combine front tyre market, with models also suited to forage harvesters, Yieldmax radials are available in 650/75 R32 or 620/75 R26 sizes. They can be specified in either steel- and fabric-belted configuration, with both using a high denier textile casing plus an advanced rubber compound for the sidewalls and tread – a combination said to maximise tyre life.
Specially-designed lugs have a high lug angle around the centreline for maximum side stability, and a sharp shoulder angle provides enhanced grip and good self-cleaning characteristics when working on soft, damp ground, claims CEAT. A rounded lug base provides good stubble resistance and a lower lug angle around the shoulders enhances traction, aided by a large footprint with a high number of lugs in contact with the ground, which is reckoned to also ensure smooth on-road performance.
Spraying technology
Farm and land monitoring specialist Metos UK, the UK arm of Austrian firm Pessl Instruments, chose LAMMA to launch its DropSight spray coverage tool. The portable system works with a mobile phone to give spray operators instant information on deposition efficiency. Claimed advantages include improved crop protection product performance, reduced risk of drift and plant run-off, reduced risk of exceeding maximum residue limits, plus minimised crop and sprayer damage risk.
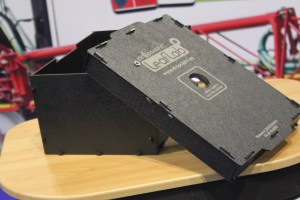
The DropSight spray coverage tool from Metos works with a mobile phone to give spray operators instant information on deposition efficiency.
After making a short pass with the sprayer to apply a solution visible under ultra-violet light, crop leaves are then selected and photographed using a smartphone. The DropSight software recognises and quantifies the deposition of solution on each leaf and measures and calculates the deposition efficacy of the spray application.
By checking spray deposition during sprayer set-up, operators can optimise nozzle selection and calibration, water volume, adjuvant selection, boom height, and sprayer speed for best results, suggests the maker.
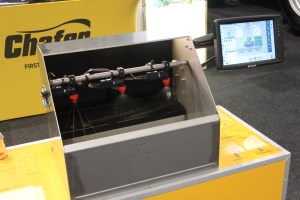
Available on all Chafer trailed and self-propelled sprayers, the firm’s new pulse width modulation system uses an electric solenoid within each nozzle body to pulse its output.
Sprayer developments included a display of the pulse width modulation system from Chafer, now available on all its trailed and self-propelled sprayers. Because it fluctuates application pressure to maintain application rate as forward speed changes, conventional pressure-based rate control has to make compromises with droplet size and therefore efficacy and drift characteristics, acknowledges the firm. This means nozzle choice is a compromise, often requiring multiple sets.
The PWM system uses an electric solenoid within each nozzle body to pulse its output on and off multiple times per second, from 10-40Hz (pulses per second), with rate changes achieved by varying the duration the nozzle is in the ‘on’ position, which is changed in relation to changes in forward speed. This allows instant rate control at each spray nozzle, and with the pressure constant, the result is said to be a consistent droplet size across the whole field. Further benefits include turn compensation, individual nozzle control and the ability to change droplet size from the operator’s seat.
The 2023 show was the first LAMMA for Sands’ new two-model Infinity flagship sprayer range, built on a new chassis that allows larger wheel equipment to be fitted and provides up to 1.2m clearance. A new hydrostatic transmission comes with traction control, and there’s fully-independent suspension. Headland manoeuvrability is aided by a foot-engaged multi-option steering system, which produces a 7.6m turning circle, while track width can be adjusted from 1.8-2.2m (72-88in).
Tank capacities are 5000- or 6000-litres, and the tanks are steel rather than the firm’s traditional GRP, with fixed internal pipework. Steel booms are said to have been redesigned for a combination of greater strength and lower weight, and are available in sizes up to 40m. The spraypack incorporates a new side-mounted filling station with 40-litre induction hopper.
Drilling developments
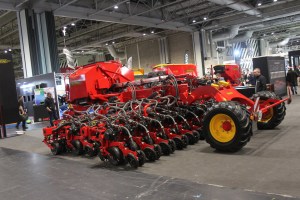
Still undergoing development trials and likely to be heavily revised before a launch, Vaderstad’s Proceed hybrid drill uses many components from the Tempo precision seeder.
Still undergoing development trials and likely to be heavily revised before a launch – suggested to be at least a year away – Vaderstad nevertheless gave UK farmers a chance to preview its Proceed hybrid drill development. It uses many components from the Swedish firm’s established Tempo precision seeder, including the hopper and the coulter arrangement.
Designed as a multi-crop drill – for everything from cereals to oilseed rape and traditionally precision drill-sown crops such as maize and sugar beet – the Proceed can be fitted with a wide variety of quick-change metering discs featuring different hole sizes and spacings. Such greater seed spacing precision enables cereals seed spacing within the row to be far more accurately set, with trials suggesting wheat seed rates could be halved for reduced seed cost and greater crop light interception without yield penalties, suggests Vaderstad. The firm says its trials have shown winter wheat drilled at 150 seeds/m2 produces 102% more plant biomass, 72% more root biomass and 62% more tillers compared with a crop sown with a conventional drill.
Row units can be adjusted to form 225 or 250mm spacings for cereals, 450 or 500mm for sugar beet or OSR, or 750mm for maize. In each row, a consolidation wheel features hydraulically-adjustable, 0-350kg downforce to allow direct drilling where possible or desired. This is followed by a debris-cleaning wheel and then an opener. Seed from the 3000-litre hopper is metered via a PowerShoot air pressure-based singulation system, similar to that on the Tempo. It’s then fed down single disc coulters and firmed in by rubber press wheels before angled pairs of closing wheels follow up.
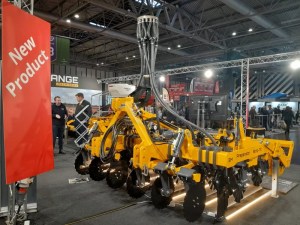
The Grange Preparator strip-tillage cultivator has been designed particularly with maize in mind, but with other potential crop applications. Granular or liquid fertiliser applicators can be fitted.
Cultivation kit
Available in 3m, 4m and 6m models, the new Preparator cultivator from Grange Machinery is now in production after a period of prototype development. Designed particularly with maize in mind, but with other potential crop applications, it works on the strip tillage principle of only tilling the soil ahead of the rows where the crop will be sown, to minimise fuel use and soil disturbance.
Key components comprise hydraulically depth-adjustable straight discs ahead of low-disturbance legs, with a maximum working depth of 30cm and possible spacings of 45/50/60/75/80cm according to the planned crop row spacing. There are then two rows of wavy-edged discs for tilth creation, again hydraulically adjustable for depth. Guttler roller units then follow to crush any remaining clods, consolidate and preserve moisture. Grange says granular or liquid fertiliser applicators can be fitted to distribute behind the legs.
Drying and haulage
Among the trailer launches at LAMMA was the GX from Krone, a self-unloader which the firm is keen to promote for uses wider than forage crops. The trailer is available in GX 440 (44m3) tandem axle and GX 520 (52m3) triple axel versions, with an ‘intelligent’ mechanical or optional electronic forced steering system controlling the rear axle on the former and the front and rear axles on the latter.
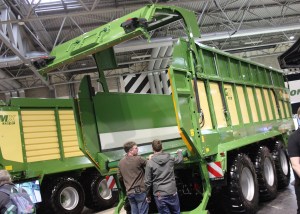
Krone’s GX self-unloading trailer has applications in root crops and vegetables, as well as maize and even combinable crops.
Both models feature standard ISOBUS operation. Cargo is unloaded by a hydraulically-powered, chain-driven fabric belt floor, an arrangement which results in gentle discharge without squeezing of the load, claims the maker, an attribute it suggests will appeal to vegetable and root crop growers.
The unloading unit is driven by two hydraulic motors of 200cm3 capacity on the GX 440 and 250cm3 on the GX 520. These operate a pair of flat-link chains with a break strength of 25 tonnes at selectable unloading speeds of 8m/min or 16m/min, with the latter emptying the GX 440 in 40 seconds. Rubber strips seal the sides for loss-free fillings, and Krone suggests the GX is capable of hauling grain and oilseed crops.
Mobile grain dryer developments from Opico for 2023 include a ‘smart’ control system for its Magna automatic models. Via a smartphone or similar device, it allows operators greater connectivity and remote control of machine operations, suggests the firm. Features include a 9.7in touchscreen display offering on-screen crop selection and management, and the ability to customise machine operation to suit individual installations. It can send batch progress reports and machine alarms via text or email, and provides real time remote monitoring of dryer operation and adjustment of settings as required. Remote monitoring and fault diagnosis support is available from Opico.
This article was taken from the latest issue of CPM. For more articles like this, subscribe here.