Download pdf
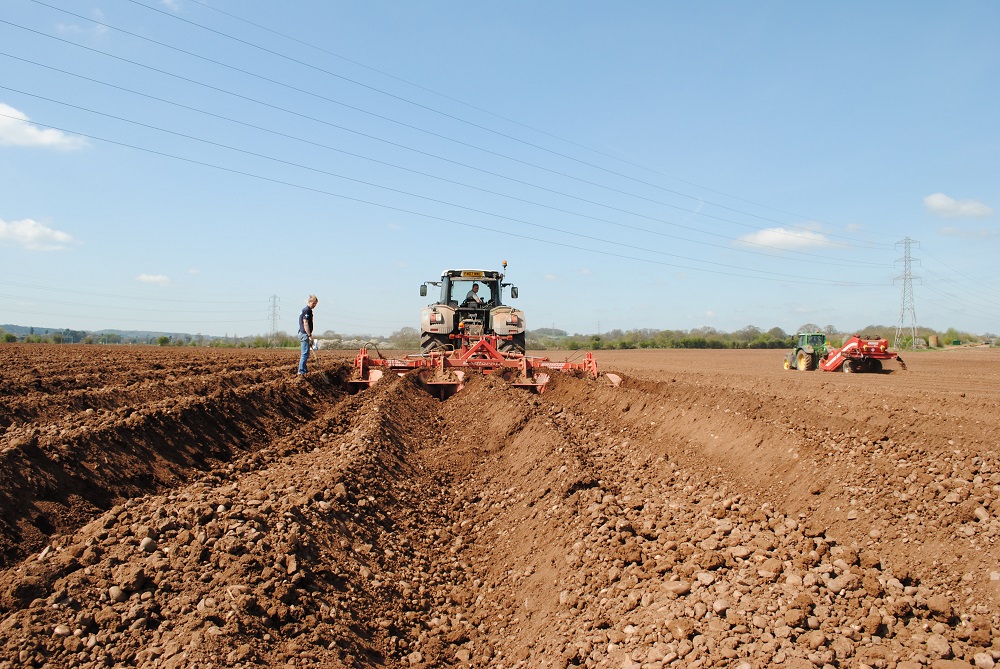
With potato planting just round the corner, now’s a good time to reassess the approach. CPM attended the meeting that reviewed the results of AHDB Potatoes’ Strategic Potato (SPot) Farm.
The idea was also to provide a platform where levy payers and agronomists can interact with and challenge the experts on their views.
By Lucy de la Pasture
The differences between pure research and actual practical application in the field can be huge. AHDB Potatoes has attempted to bridge the gap by showcasing all the latest research in a commercial setting at their SPot Farm in Staffs.
Levy payers fund £1.5 million of research and innovation. That’s a lot of useful information being generated but the problem has always been getting the benefits of research into growers’ hands, explains Dr Philip Burgess, head of knowledge transfer at AHDB-Potatoes.
“The idea was to highlight some of the research that’s going on but also to provide a platform where levy payers and agronomists can interact with and challenge the experts on their views in a practical situation, right through from planting to harvesting.
“At the Strategic Potato Farm we’re scaling up the research work to commercial, field-level demonstrations. At
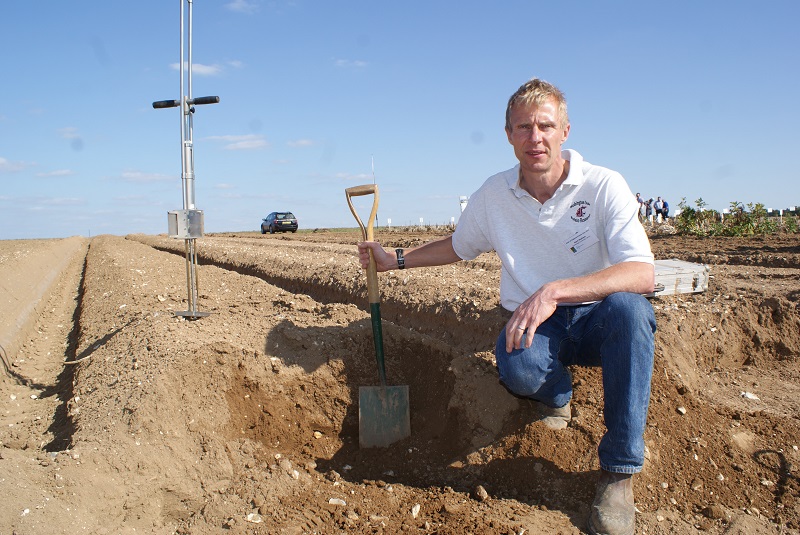
The objective of forming a bed is to get just enough soil to grow a crop of potatoes, says Mark Stalham.
James Daw and family’s farm, W B Daw and Son, in Staffs we’re examining potato production from a best practice perspective on a 20ha site.”
In 2015, the demonstration site looked at best practice on nutrition, soil management and cultivations, seed rates, greening, crop variability and yield mapping, irrigation scheduling and preventing run-off.
“There has been a tremendous amount of engagement from across the industry in the first year of the project. This year an additional SPot Farm in the East has been proposed and the areas of work we’re showcasing is set to expand,” explains Phil Burgess.
James Daw is a progressive farmer and along with his son, Sam, is at the cutting edge when it comes to gadgets and the latest precision techniques. Soil mapping, crop canopy assessments and the use of drones are some of the areas where precision technology is helping to build a wealth of information.
“It’s helping us better understand the land we’re working with and the areas where we can push the yield potential, as well as the marginal areas where we can make potential savings because they persistently underperform,” says James Daw, explaining the rationale.
Soil tests kick off the planning, with a nutrient and PCN analysis as well as soil electrical conductivity testing. This measures the soil water’s ability to conduct positive charge which correlates with soil properties that affect crop productivity, including water content, soil texture, cation exchange capacity (CEC), drainage conditions, organic matter level and subsoil characteristics.
To make the SPot demo site meaningful, James Daw chose a field with variable soil type to be typical of the real life challenges growers face. The SPot Farm demonstration was situated on Gravelly Bank, a sandy clay loam soil with a clay content between 19-35%. As its name suggests, the field is moderately stoney, largely in the subsoil, giving the site potential for vulnerability to drainage as well as structural problems.
Pracitical headache
Before a potato was even planted, Gravelly Bank threw up the first practical headache for the SPot team, which led to a switch from the primary cultivations intended as current best practice. “The field had been in stubble turnips over the winter and grazed by sheep,” explains Dr Mark Stalham of NIAB CUF.
“Best practice on the farm is to generally go in with the Simba SL as primary shallow cultivations (to 25cm depth) and this is what was planned, but the wet spring and sheep had really caused the soil to slump.”
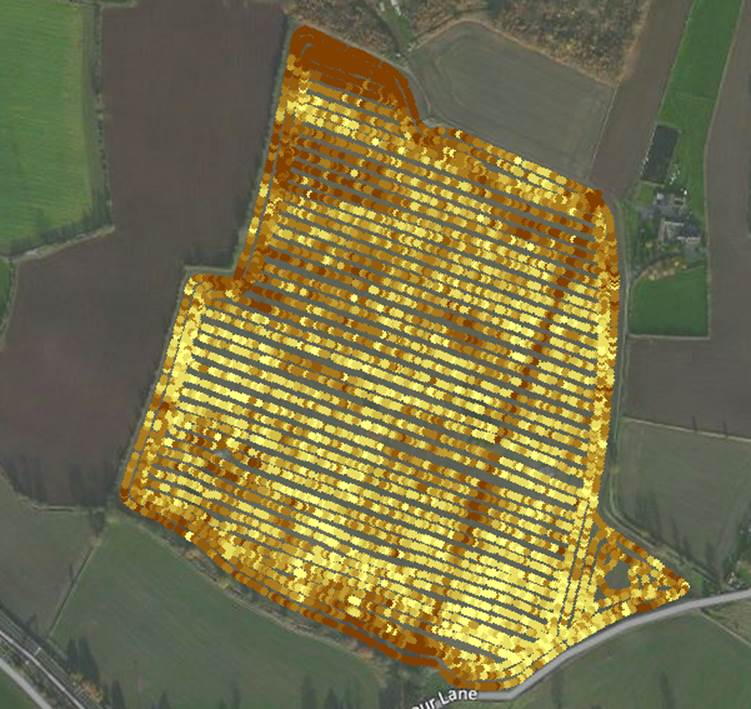
An electrical conductivity scan of the SPot Farm site shows an area of heavier soil as well as an old pipeline across the right-hand section of the field.
“We had a plan but had to adapt our best practice to suit the season,” adds James Daw. “We ploughed (to 35cm depth) at right angles to the Simba cultivations because the soil was very wet underneath. It was a surprise to us to have to plough. This field has been in potatoes 4-5 times since the 1980s, always from stubble turnips and we’ve not had to plough before potatoes in the past. It just goes to show that you have to have flexibility as every season is different.”
The demo work looked at work rates and costs of bed-forming following the different primary cultivations – best practice plough versus the Simba SL non-inversion. “Bed-forming following the Simba was slower with wheelslip 8.7% higher than on the ploughed land. That equated to an increase in fuel and labour cost of 39%,” explains Mark Stalham.
A closer look at the bed-forming depth, carried out with a John Deere 8360R (360hp) with Sumo Forma behind, showed there was scope for working at a shallower depth than the farm’s current best practice, with savings to be made on fuel, labour, fewer clods and without adverse effects on yield and quality.
Shallow depth
The standard practice was bed-forming to a depth of 45cm but working at the shallower depth of 37cm was 32% faster than the standard, 23% cheaper on fuel and labour and with fewer clods. In contrast, deeper bed-forming at 60cm was double the cost of the standard 45 cm depth, with the highest wheel slip of all at 28%.
Eyebrows were raised at the observation that bed-tilling as a matter of course is a questionable practice on many
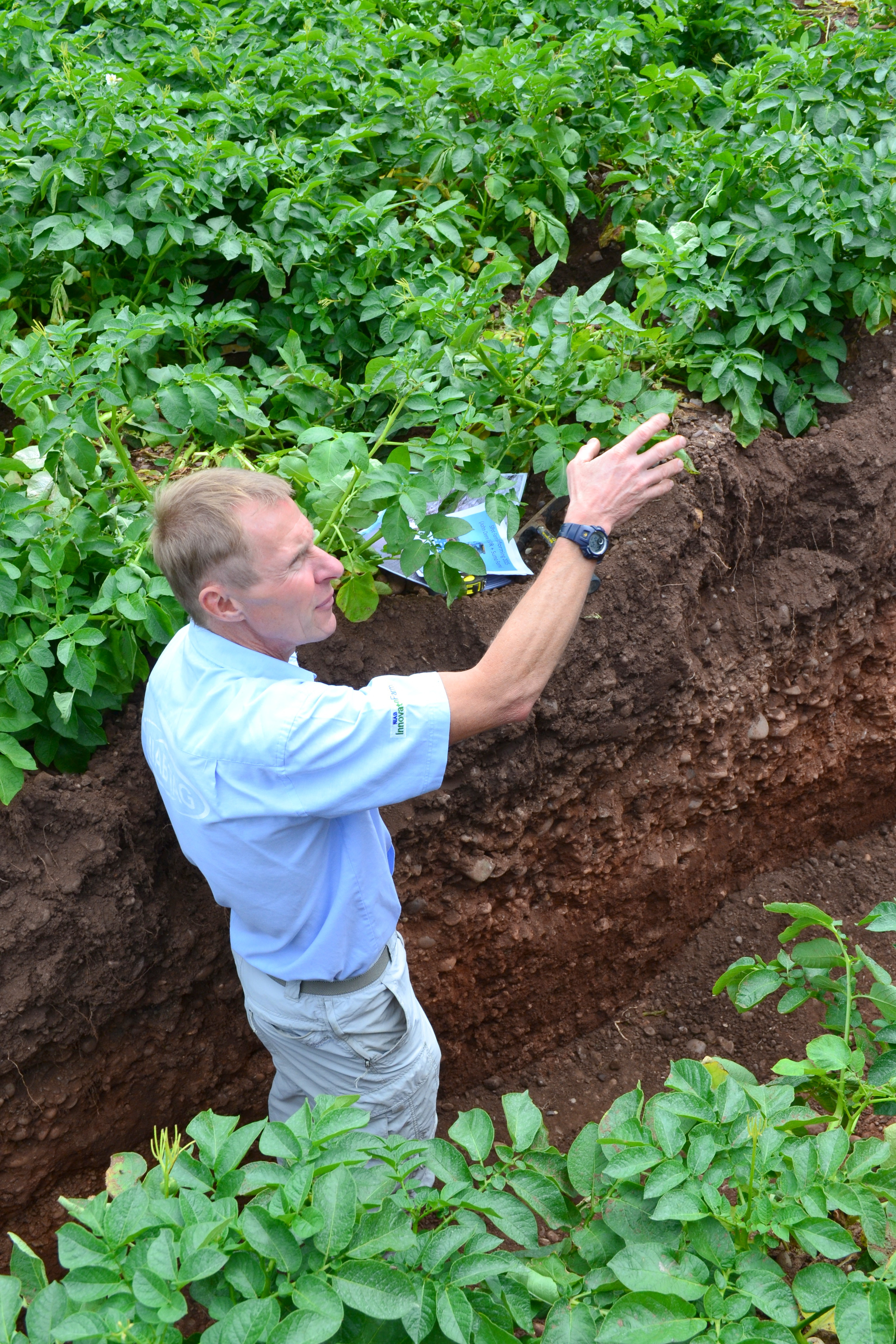
A bed depth of 31cm allows 19cm of soil between the top of the ridge the bottom of the seed tuber, leaving 12cm of soil below the seed.
soils and may not be a necessary operation. Mark Stalham explains, “The objective of forming a bed is to get just enough soil to grow a crop of potatoes – too deep and you may create a fluffy bed with a fine tilth that will be susceptible to slumping.”
At the SPot Farm, the standard practice is to deep bed-till using a Grimme RT6000 behind a Fendt 936 Vario, producing a bed depth post-tilling of 56cm. Shallow and deep bed-tilling were compared within each of the shallow, standard and deep bed-forming demonstrations.
“Deep bed-tilling was very costly in terms of fuel (£34/ha), compared with £13/ha for the shallow. Deep bed-tilling was also not effective at reducing the proportion of large clods,” explains Mark Stalham.
“Where rows were shallow bed-formed and shallow bed-tilled, the operations were 48% faster than the standard best practice but de-stoning work rates (one of the major reasons for bed-tilling) and fuel consumption were only improved where deep bed-forming was carried out.”
According to James Daw, the shallow beds were anecdotally slower to harvest but there was no increase in dirt tare, misshapen or green tubers. In fact, across the cultivation demos, there was actually more tuber greening in the standard and deep beds than in the shallow.
That trend was repeated when the bed-tilled plots were assessed versus the no bed-tilled, there was more greening where the seedbed had had the extra pass. In spite of the possible advantages of moving to shallow secondary cultivations there was a common feeling of nervousness about making the change among the growers present.
When asked directly whether he now had the confidence to set cultivations shallower, James Daw replied that he has doubts because of the variability in depth of soil across his farm.
“Have I always gone in too deep and overworked the seedbed? Yes, I think I have. In 2012 we had a good planting and then had 39 inches (990cm) of rain and the soil slumped. If the seedbed had been left coarser then harvesting would have been easier,” he says.
“I’ll now try not to overwork the soils and I’ll go in shallower, but I’m not confident not to bed-till. What happens before the de-stoner is the important bit.”
Mark Stalham was quick to point out to James Daw that he knows his soil and knows where it’s deep with more clay and where it’s shallower. “Why not run the bed-tiller as usual but only work at depth where you really need extra soil to plant? For the rest of the row, where bed-tilling isn’t essential, just shallowly work the soil as if you were incorporating a nematicide as this is the key to breaking down clods,” he suggests.
With a plethora of maps generated by the precision techniques used on the farm and a very engaged team of tractor operators, it’s an approach that James Daw will consider as it would reduce machinery costs yet keep work rates up.
The best approach for growers is a gradual move towards working shallower on your own soils, suggests Mark Stalham. “Do some controlled strips and come up an inch (25mm) in depth every year until you find your own optimum.”
The general consensus in the room was that the majority of soils are overworked, destroying soil structure. Possibly because of the horse power available in modern tractors makes it easy to pull equipment over-deep, just because they can.
“Soil type will be the major factor influencing how shallow you can work,” adds Mark Stalham. “In sandy soils, there’s a risk of creating a pan if you work too shallow. In sandy and silty loams, if you work too deep then there’s a trend that yields will be lower because you get slumping with rainfall. In heavier soils, it’s important to remember to manage the soil rather than the clod.”
Moving back to the point of how much soil is just enough in a bed, Mark Stalham points to the shallow de-stoning treatments where the bed measures 28cm from the top of the de-stoned bed to the depth where the harvesting share will operate.
“When bedded up this will give you a depth of about 31cm. If you plant tubers so there’s 15cm of soil between the top of the seed tuber and the top of the ridge and 19cm to the bottom of the seed tuber, then this still leaves 12cm of soil in the bed below the seed. That’s more than enough and when questioned, harvester drivers often only request 5-6 cm below the deepest tuber.”
Summing up the event, Phil Burgess notes that perhaps the real value of the SPot Farm lies in the discussion and not just bridging the gap between research and farm practice. “The SPot Farm helps everyone involved in the industry interact, which highlights the gaps in communication where information needs to be more available. There’s also a sharing of knowledge as well as the latest researched-based thinking to take back to their own potato enterprise.”
Seed age key to tuber size
Another of the areas being explored at the Spot Farm is seed rates and how best to meet the size requirements of the target market. One of the points made was that not all varieties behave in the same way when it comes to the relationship between stem production and age of seed.
As a general rule, older seed produces more stems than younger seed of the same size, explains Dr Mark Allison, NIAB CUF. “The interval from emergence of the seed crop to planting the ware crop determines the seed age. Early emerging seed is ‘older’ than later seed when planted on the same date.”
So what’s the practical application of this knowledge? “As seed becomes older it becomes more precocious, producing more stems, and has a shorter growing season. That means you need to adjust the planter to a wider spacing,” he explains.
“A key aspect is to know the characteristics of the variety you’re planting because there can be big differences between the response of different varieties to age and this can influence optimum spacing by as much as 25%.”
“A variety such as Innovator (planted at the SPot Farm) isn’t as effective at opening its eyes to produce stems as a variety such as Estima, so for Innovator there isn’t such an important relationship between age and stem production,” adds Mark Stalham.
“According to the work done by CUF, most commercial seed is planted too close together, reducing marketable yield. It’s actually better to have some seed left over at the end of planting than to make what you have fit, so monitor seed at planting to see if you’re achieving your target spacing.”
“The results of a PhD thesis being carried out at Cambridge University show that the important thing to get right, in terms of seed rate, is the overall number of tubers planted per ha. The average spacing in the row probably doesn’t matter as much in terms of overall yield, but avoid double-dropping seed pieces,” adds Mark Stalham.
In general discussion, one of the points universally agreed upon by the growers in the room was that they needed to have more information supplied to them when their seed is delivered. James Daw outlined the current scenario.
“Seed grown under contract arrives on the farm with tuber counts, but we don’t know its age, whether or not chits have been knocked off and it’s virtually impossible to find it out. It would be helpful to have this information.”
Representatives of the seed trade assured growers that things were getting better. According to HZPC’s Richard Baker, the breeders of Innovator, one of the best ways to find out the age of the seed is to ask for the date of herbicide application by the seed grower and add seven days.
A right Royal crop
Last year was a year of record-shattering, bumper yields. Although the achievements in the combinable crops sector grabbed the headlines, a Yorks-based British potato grower is also flying the flag, having harvested a whopping yield of the processing variety, Royal.
According to the Guinness Book of Records, the world record for a crop of potatoes stands at 72.9t/ha. Although Ibbotsons Produce’s director, James Hopwood, isn’t claiming a new record, the transport tickets are proof enough that his processing crop of Royal has performed extremely well, producing 79.64t/ha on contract to McCain Potatoes.
Asked what he attributes the huge yield to, he quickly points out that Royal is a naturally high yielding variety, reflected in the contracted tonnage of 59.3t/ha. “However, the yield in itself, I believe, is through taking a holistic view to production and therefore productivity.”
As part of that approach, good soil management forms the linchpin of the farming enterprise. “It’s important to retain and build soil organic matter to enable improved moisture and nutrient management. This field was planted with a stubble turnip cover crop over the winter, grazed by sheep which helps us achieve this while also keeping volunteer weeds down,” explains James Hopwood.
He also uses hot radish as a cover crop on the farm, which he incorporates in mid Nov, because its biofumigant activity helps reduce populations of PCN.
“We have our cattle muck analysed which this year was applied at 20t/ha, using spreaders with weigh cells to make application as accurate as possible. We use soil mapping and analysis over the farm to optimise the accuracy of P and K applications, which we apply at a variable rate according to the mapping information. I believe this has helped us increase the uniformity of our soil indices across this field over a period of years.”
All James Hopwood’s potato ground is flat-lifted before ploughing to 30cm. A base suspension fertiliser is applied onto the ploughing, before deep ridging and bed- tilling (if required depending on soil conditions) prior to a pass with Grimme CS150 de-stoner.
“We’ve moved to rotavating behind the de-stoner to incorporate nematicides, when required, with a small set of ridging bodies behind,” he adds.
Part of James Hopwood’s ethos is to prevent his crop from coming under stress. To help achieve this, neutron probes are used to monitor soil moisture deficits and manage irrigation accordingly, with only 3 passes required in 2015.
He believes one of the key factors influencing the performance of the crop is supplying nutrients throughout the crops rapidly changing growth stages to avoid any hidden hungers.
“We use the Optiyield nutrition management plan throughout the crop’s development. This helps us meet the crop’s requirements for nutrients in a strategic and targeted manner. We also apply biostimulants when the Optiyield model suggests and have increased our marketable yield by an average of 12% over the past three years.”
As a further management tool, James Hopwood uses a drone to help identify any areas of concern in the crop. “In this field, the drone picked up an area of 0.25ha of nitrogen-rich canopy, which turned out to correspond to an old muck midden. This had the potential to effect the dry matter content so we were able to manage this small area appropriately as a result,” he explains.
The making of a bumper crop
Harvest date | 23 Oct – 03 Nov |
Yield | 79.64t/ha |
Average tuber count per 10 kg | 37 |
Planting date | 18-21 April |
Nutrition | |
Available nitrogen/t | 0.75kg |
Available phosphate/t | 2.0kg |
Available potash/t | 7.4kg |
FYM applied | 20t/ha |
Fertiliser suspension/liquid broadcast | 1925kg/ha of 13-9-22 |
Optiyield programme | |
GS3 tuber initiation (early hooking) | Activator, Base, Ful-zinc, Ful-man |
GS4 tuber initiation (swelling) | Phi-diamond, Activator, Seaspray 45, Ful-mol, Optiyield K |
GS5 50% of swellings are twice stolon width | MagPi, Ful-K |
GS6 50% ground cover | Seaspray 45, Activator, Base |
GS7 All tubers formed, rapid growth ends | Aqui-S |
GS8 100% ground cover, tuber bulking begins | MagPi, Optiyield K, Seaspray 45 |
GS9 Mid tuber-bulking | Phi-diamond, Seaspray 45 |
Irrigation | 18mm on 14 June
22mm on 28 June and 15 July |