For growers looking to ensure optimum soil pH and therefore maximise yields and enhance overall soil health, LimeX is arguably becoming a go-to product to address this critical aspect of rotational management.
However, scratch beneath the surface and a significant added benefit comes to the fore – the fact LimeX is a co-product of the sugar beet manufacturing process, helping to minimise waste while delivering a unique product.
A division of British Sugar, LimeX is manufactured at the Wissington Factory at King’s Lynn in Norfolk, explains general manager, Elliott Fisher.
Production process
The production process starts once the intake of sugar beet has been de-stoned, washed and cleaned; then sliced, diffused with hot water, and purified. “It’s during the purification process when we remove the non-sugar from the ‘raw juice’ that the LimeX story begins,” he explains.
Following purification where milk of lime and CO2 are produced and combined with water, calcium carbonate crystals and non-sugars can be settled out as solids. “This thick slurry is pumped to membrane presses where a huge hydraulic force presses down, pushing any water through and leaving a dry cake – this is LimeX.”
The product is then stored before being distributed across the country and eventually spread on farmers’ fields. While it’s not a short process, from start to finish, it only takes a few days, adds Elliott.
It’s these origins that also give LimeX its key benefits, explains LimeX manager Glenn Carlisle. “Because LimeX is created in a chemical process rather than a ground rock, it has a very small particle size, which means it is fast acting once it’s spread on a field.
“This is important for its key role in pH correction, but also for targets such as clubroot control in brassicas. Additionally, because of its origins in the sugar filtration process, LimeX has nutrient value beyond calcium. Each tonne of LimeX contains 9kg of phosphate, 7kg of magnesium and 6kg of sulphur.”
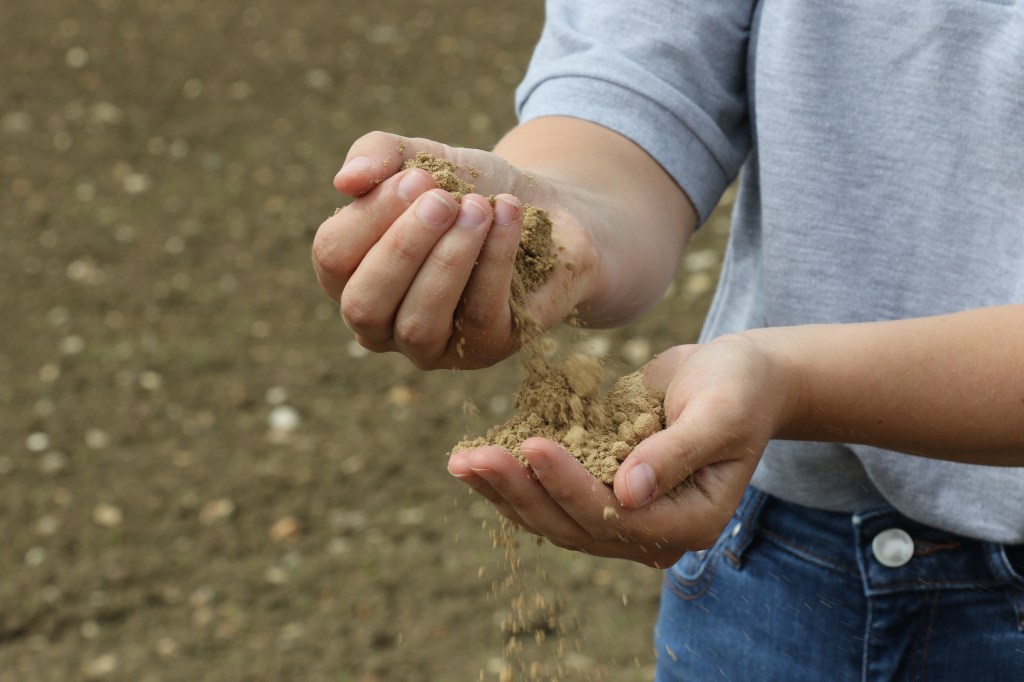
Scottish distribution
Contractor Zander Hughes of Forth Crop Solutions in Fife was first introduced to LimeX through a new customer, who specifically requested the product. With demand accelerating from the off, he’s now distributing LimeX across his region.
“We received 3000t into Fife this spring with more on order for post-harvest – so far, it’s worked remarkably well,” he says. “It’s a cost-effective alternative to conventional ground limestone, but you have the added benefits of a formulation which includes key nutrients calcium, phosphate, magnesium and sulphur.”
Zander points out that due to how quickly LimeX gets to work, it means applications can be ‘just-in-time’. He’s also been impressed with the speed of delivery – around a week turnaround from order through to being spread on fields.
“Product comes in and out as required with us receiving consistent loads on a regular basis. While we have a storage facility we can use, customer demand has meant we’ve not had to use it.”
Efficient logistics
He’s also found a way to make his own logistics even more efficient. “By working with some of our customers who are transporting carrots south, we have the opportunity to backload those lorries with LimeX for their return journey north. This makes distribution really easy,” concludes Zander.
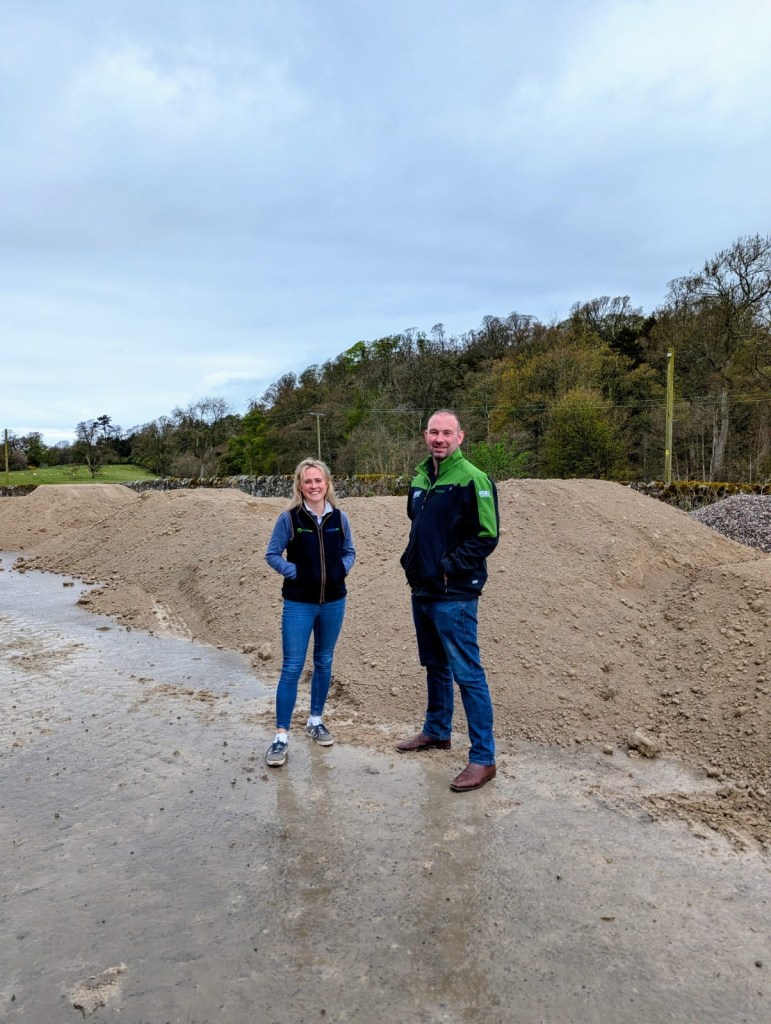
For more articles like this, subscribe here.
Sign up for Crop Production Magazine’s FREE e-newsletter here.