Advances in tyre technology and the development of on-board inflation systems mean high horsepower tractor users no longer need to make efficiency, safety, comfort and compaction compromises when moving frequently on the road between fields. Claas talks CPM through the operating principles and advantages of the CTIC system for its Axion 900 and 800 tractors.
“When you examine the soil, you can clearly see what it does to reduce soil compaction.”
By Martin Rickatson
Seeing a tyre rapidly losing air isn’t usually an enjoyable experience but watching all four boots on the Claas Axion 950 at the maker’s Manns dealer demo day deflate simultaneously is impressive.
With the controlled deflation stopped automatically, according to the required set pressures on the tractor’s CEBIS terminal, each tyre’s ground contact area is lengthened and slightly widened. And so the tractor sets off down the demo field, with its Grange toolbar and Horsch Joker disc cultivator in tow.
As the tractor makes its return run, the cultivator combination is lifted out of work as it reaches the headland. The compressor kicks into life as the operator activates it from the CEBIS terminal, and within a minute, a compressor air flow rate of 2800 l/min has inflated all four tyres back up to their recommended road pressures.
“That’s how quick this system allows the user to switch between the best possible pressures for field work and road travel,” says Patrick Frawley, sales trainer and demonstrator at Claas UK.
“Watch the tractor on a pass with and without lowered tyre pressures, and you can almost see the difference this makes to workrates. When you examine the soil, you can clearly see what it does to reduce soil compaction – it would be even more noticeable on heavier soils with a higher moisture content. It’s when you’re in the cab, though, that the evidence of reduced slip, reduced fuel use, and increased area covered per hour, becomes clear through the tractor’s CEBIS screen.”
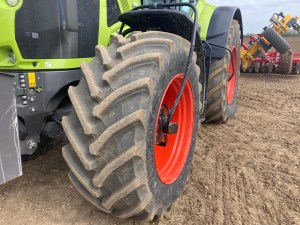
Claas says customers keen to maximise soil protection without compromising road comfort are increasingly specifying its CTIC (Central Tyre Inflation Control) system on larger Axion tractors.
For 2021, Claas upgraded its CTIC (Central Tyre Inflation Control) system, introducing a CTIC 2800 version alongside the standard CTIC system. Both are available for the maker’s Axion 900 (325-445hp) and 800 (205-280hp) series tractors, as well as the Arion 600 (145-185hp) and 500 (125-165hp) lines.
The key difference between the two packages is that the 2800 uses an external compressor mounted on the right-hand side of the cab and offers a higher air capacity and reduced inflation time. The lower-cost standard CTIC system is concealed within the engine compartment, with a lower-capacity compressor and hence slower inflation.
“Depending on the type of tasks carried out, their frequency and how often it’s necessary to travel between fields on the road, each system has its merits,” suggests Patrick.
“There will be situations where, even on a larger farm, the standard CTIC unit may do everything a customer needs. But where businesses are spread over a wide area, necessitating a lot of road travel or doing a lot of regular field/road switching such as working with a slurry tanker, the CTIC 2800 system is likely to soon pay its way because of the speed at which it operates.”
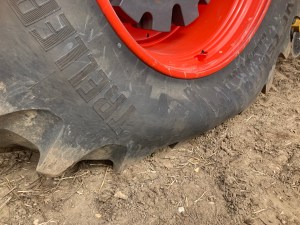
The primary benefit of variable tyre pressure systems is that they lengthen the contact patch of each tyre, with negligible effect on transport width of just a few additional millimetres.
As it’s ISOBUS-based, the CTIC systems can be operated either via the Claas CEBIS touchscreen in the Axion and Arion tractors, or through any ISOBUS universal terminal, including Claas’s own S10 or new CEMIS 700 and CEMIS 1200 terminals. Because all options use ISOBUS technology, plug-and-play functionality means that once the required parameters are entered into the terminal, switching between field and road pressures can be done at the touch of a button.
Claas also makes it possible to add linked regulation of the tyre pressures of trailed implements such as slurry tankers and muck spreaders to the CTIC 2800 systems only, by plugging installed air feed architecture on the implement into an air feed on the tractor, and pressures for these can also be stored.
“On Axion 800 and 900 series tractors with the CEMOS machine optimisation system, it’s also now possible to integrate either CTIC system into this,” says Patrick. “This means we can achieve intelligent dynamic internal tyre pressure adjustment in interaction with other parameters, such as ballast and by taking into account data recorded by sensors on the tractor.
“The result is less wheelslip, reduced ground compaction and soil smearing, and lower diesel consumption, plus increased workrates.”
The CTIC 2800 is capable of inflating all four tyres on a tractor equipped with 600/70 R28 and 710/70 R38 tyres from 0.8 to 1.8 bar in one minute and 20 seconds, says Claas. The seals of the rotary unions and the lines are only loaded during pressure changes, with the spool valves that activate the system integrated into the patented rotary transmitters to provide direct high-precision tyre pressure measurement and control. The air lines can be telescoped using quick release clamps and locked in place via a parking position on the mudguards. Tyre pressures are continually monitored and automatically adjusted.
“As an example, the Trelleborg TM1000 tyres on this Axion 950 have been set for the road at 1.4 bar in both the 650/65 R38 fronts and the 750/70 R44 rears. For field work with this Horsch Joker/Grange toolbar combination, we can safely lower them to 0.8 bar in the front and 0.9 bar in the rear.
“CTIC isn’t something every buyer of every tractor in these ranges will find of value, but we are seeing a steadily increasing uptake of CTIC systems among Axion buyers in particular,” says Patrick.
“For primary cultivations, reduced pressures put more lugs on the ground to increase power transfer and enhance traction, improving pulling performance, while in secondary tillage applications that additional ground contact aids flotation, reduces compaction and improves tractor performance on loosened soils.
“One of the factors that has aided our development and compatibility of these systems, as well as the marketing as an integral part of the specification options, is that Claas has invested in manufacturing, having taken a controlling interest in the maker,” he says.
“This enables us to have direct input into design and manufacturing to suit our tractor ranges. In terms of reliability, by not using rotary couplings in the axles, we eliminate any risk of failure here. All architecture for the hydraulic and electrical supply is sited under the cab, so the only external evidence beyond the compressor itself is the air hoses to the wheels and tyres, and these are carefully designed to minimise the likelihood of them getting damaged.
“It’s also a very smart system, with the main feed line supplying multiple different pressure sense lines to each tyre, and the pressures of all four tyres are monitored to ensure they’re balanced. And it’s easy to undo the quick couplers should a wheel need to be removed for a puncture repair.”
Setting field and road pressures across each axle is a matter of tapping the required symbol on the CEBIS or other ISOBUS terminal screen, and inflation or deflation then requires a further symbol tap – for those who prefer it, function keys on the tractor armrest can be assigned to do this instead.
Once the tyres are at the inputted pressure, the compressor stops and the system takes a measurement check on all four tyres to ensure the pressures are correct. Settings for tractor tyre pressures as well as those for any implements, if applicable, can be stored in the CEBIS terminal.
“Different tyre manufacturers and different models and sizes of tyre will have different maximum and minimum recommended values for different axle weights,” points out Patrick.
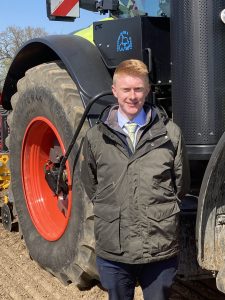
Patrick Frawley: Interest is growing in variable tyre inflation, particularly given the amount of roadwork many tractors have to do today as farms have grown larger.
“Specifying tall diameter tyres will further help to put more lugs in contact with the ground at lower working pressures, improving traction and spreading axle loads to improve flotation and minimise compaction.
“When selecting working or travel pressures, it’s important to take into account the tractor and implement combination weight, along with your intended working speed. Our conventional wheeled tractors are designed with a 50:50 static unballasted weight distribution, so that this is transformed to 60:40 when pulling a draft load, to account for weight transfer to the rear axle.
“The system works well with the full range of tyre options we offer for the Axion 900 and 800 and the Arion 500 and 600 series tractors. For the higher-hp models in particular, investment in the system is an effective way to make the most of modern tyre technology.”
That particularly includes tyres designed with increased flexion (IF) construction, he suggests, where it’s possible to operate at 20% lower inflation pressures for the same rated load, and those with very high flexion (VF) characteristics, where the figure is 40%.
“The obvious primary benefit is that rather than broadening the tractor’s contact patch, as would be the case with wider tyres or dual wheels, the patch of each tyre is lengthened, with a negligible effect on transport width of just a few additional millimetres as the tyre profile changes, keeping tractor width within three metres.
“This makes this arrangement especially ideal for UK roads, avoiding potential road travel difficulties caused by wide tyres or duals. Additional traction and flotation is available at the touch of a button, and a further button press means you’re good to go again on the road at the end of a job in only around a minute.
“Tyre pressures are always at the optimum level for the task or the travel at hand, and the operator also benefits from tyre pressures that provide the best possible ride in the situation, without causing the tractor to bounce or wallow.”
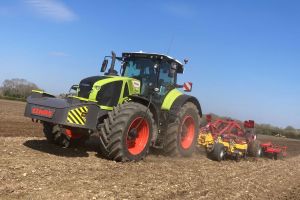
For users seeking even greater ground contact, Axion 930 and 960 tractors are available with Terra Trac rear tracks, which can be supplemented with a CTIC system on the front axle.
The cost of a CTIC 2800 system, as ordered through Claas dealer parts as a dealer-fitted option, is in the region of £12,000, depending on tractor model. Installation charges to plumb in the pipework and compressor then need to be factored in, but a tractor ordered dealer-ready for installation comes ready-prepared with the hydraulic and electrical architecture beneath the cab, and with pre-drilled wheel rims to accommodate the valve and line-feed equipment.
“We now have a number of Axion 800 and 900 UK customers with installed CTIC systems, and interest is increasing, particularly given the amount of roadwork many tractors have to do today as farms have grown larger.
“Putting more tyre lugs in contact with the ground means reduced wheelslip, translating to increased output covering a greater area per hour from the same amount of fuel. Variable tyre pressure technology like this produces direct benefits in terms of operating efficiency, in addition to the pluses of reduced soil structure damage from minimised wheelslip.”
While it doesn’t bear direct comparison in every set of circumstances, a growing number of farmers seeking greater in-field traction and efficiency over and above on-road performance are increasingly specifying rear track units on Axion 960 and 930 tractors, says Patrick.
“The length of the Terra-Trac belts obviously takes the amount of ground contact provided by two belts and two tyres to a much high level than on a CTIC-equipped fully wheeled 960 or 930. For applications where frequent switching between road travel and field work is less common, Terra Trac specification offers the combination we believe provides the best blend of abilities in work and when turning on the headland.”
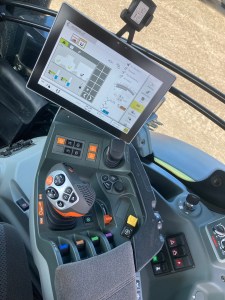
Setting field and road pressures across each axle is a matter of tapping the required symbol on the CEBIS or other ISOBUS terminal screen, and inflation or deflation then requires a further symbol tap.
While none of the units so far supplied in the UK have yet been specified with the system, it’s possible to fit CTIC to the front axle of a Terra Trac-equipped Axion 930 or 960, and Claas may consider running a demo unit with the standard UK configuration of 735mm-wide belts and 710mm-wide front tyres – a combination which puts 3.6m2 of rubber on the ground – fitted with an optional CTIC system for the front tyres.
“With only the two tyres to inflate, this configuration would require only the standard CTIC system with the engine-based compressor rather than the separate external 2800 unit. For an owner seeking to operate a 930 or 960TT to 100% of its tractive capacity across a big workload, it’s definitely something to consider.
“There are a number of reasons we believe the combination of front tyres and rear tracks is the best solution for this tractor type and power level, but among them is that the tyres evenly consolidate the soil surface to provide the rear tracks with the ideal surface on which to gain full grip. Unlike a conventional tractor with a 60:40 unladen weight distribution, a 900 series in TT specification is designed with a 60:40 unballasted weight ratio, which shifts to 70:30 under load,” he says.
“A Terra Trac machine is capable of a 40km/h top road speed rather than the 50km/h of wheeled equivalents in the Axion 900 series. But for requirements where the tractor’s focus will almost exclusively be on heavy cultivations, topwork and drilling, the Terra Trac price premium – which is three to four times that of specifying a CTIC 2800 system – is likely to be favourable over a wheeled machine with CTIC. This is because it offers further reduced slip levels – down to just 1-2% at 100% engine load – and further enhanced workrates and efficiencies.”
This article was taken from the latest issue of CPM. For more articles like this, subscribe here.
Sign up for Crop Production Magazine’s FREE e-newsletter here.